Photogrammetry and light scanning
3D Scanning, like 3D printing, is a broad term that describes many different processes and applications. I’m starting a short series on Talk to discuss all the basics of 3D scanning technologies, relevant for 3D printing. I would love to have your feedback and comments, so we can make it the best 3D scanning series of the internet! Let’s go
3D Scanning technologies allow for the creation of of 3-dimensional objects. By using 3D scanning you will be able to capture a digital copy of a physical real world object. To exemplify the extent to which 3D scanning will have impact, imagine for example the reconstruction of a severely damaged human skull, that was scanned and replicated in titanium. Or the fact that we can digitize cultural heritage and art, making it timeless and immune to the effect of wars. Moving forward, one can imagine a world where basically everything has a digital counterpart. A world where the difference between physical and digital no longer exists, where VR is just as real as anything else. Things can get crazy.
Now let’s get practical. For 3D printing, there are roughly two relevant techniques of 3D scanning:
- Photogrammetry
- Light-based scanning
Photogrammetry
Photogrammetry is the easiest way to get started in 3D scanning. The method is based on taking 2D pictures around an object, from different angles, and stitching them together into a single 3-Dimensional image. The last part being handled by software. It only requires a camera to do so and that means that you can go ahead and do it right now, even with your smartphone!
Photogrammetry
Next step is to stitch your photos together to create a 3 dimensional mesh of the object you captured. 123D Catch 22, Trimensional 16, or Trnio 15 are all great apps for this. The software will match all overlapping points of the images and create a 3D model.
Light-based scanning
There’s two common types of light based scanners used for 3D scanning - “structured light” and “laser scanning”. Structured light scanners send patterns of light onto the object to capture. Based on the deformations of the pattern it determines the model form and creates a 3D mesh, or digital replica.
Laser scanning uses a slightly different method. It measures the angle of the reflected lasers which it can translate into coordinates of an object and therefore into a 3D mesh.
Laser scanning
Most of the current hand-held scanners use the laser scanning technology. Some of them like Structure.io 15 or iSense 4are simply a laser with a sensor that you can mount on your smartphone or iPad. While others use a small spinning platform, to place an object on and scan while it is the object that turns. This is how the Makerbot digitizer 17 works, for example.
That’s it for now! I will continue this series and dive into different aspects of scanning. Please do leave your comments and critics so we can make this a great resource! Also tell us which topics you would like us to cover and we will.
Happy scanning!
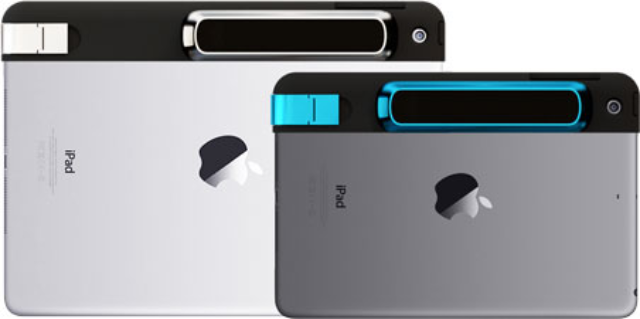
created
Jun '15last reply
Jul '15- 6
replies
- 6.2k
views
- 5
users
- 28
likes
- 8
links