Surface finishes
Powder coating services
We offer several powder coating finishes that improve the strength and wear-resistance of your metal parts. Powder coating is compatible with all metals and available in glossy or matte gloss.
Surface preparation | Colors* | Glossiness | Cosmetic availability | Thickness | Visual appearance |
---|---|---|---|---|---|
As machined (Ra 3.2μm / Ra 126μin) | White, Black, RAL and Pantone | Glossy (Above 70 GU) | No | 50μm to 150μm | Parts are powder coated directly after machining. |
As machined (Ra 3.2μm / Ra 126μin) | White, Black, RAL and Pantone | Matte (Below 30 GU) | No | 50μm to 150μm | Parts are powder coated directly after machining. |
Color options for powder coating




Gloss options for powder coating

16 to 25 units

80 to 95 units
Example of a powder coated part


Design considerations for powder coating
Design considerations for powder coating
Hanging and jigging marks:
Powder coating involves suspending parts via a “jig” or “rack.” This will leave marks on your part where powder coating wasn’t possible. If there are areas where you can’t accept “jig” marks, please remember to include a technical drawing indicating these areas.
Masking:
Remember to indicate in your CAD file whether you want specific part areas to be masked or plugged.As material is applied to the surface during powder coating, all threaded and reamed holes or other critical-to-function surfaces are plugged or masked as standard.
Tolerances:
Tolerances are met before the coating finish. We recommend that you ask for clarifications about masking as needed.
The Protolabs Network powder coating process
The Protolabs Network powder coating process
Powder coating is a strong, wear-resistant surface finish that is compatible with all metal materials.
Here’s how to apply powder coating:
Clean parts to remove inorganic contaminants To enhance performance and quality, pretreat parts with a conversion coating Rinse and dry parts in an oven Mask critical areas to prevent tolerance issues Coat parts with an electrostatic spray gun Dry parts in an oven to cure the coating
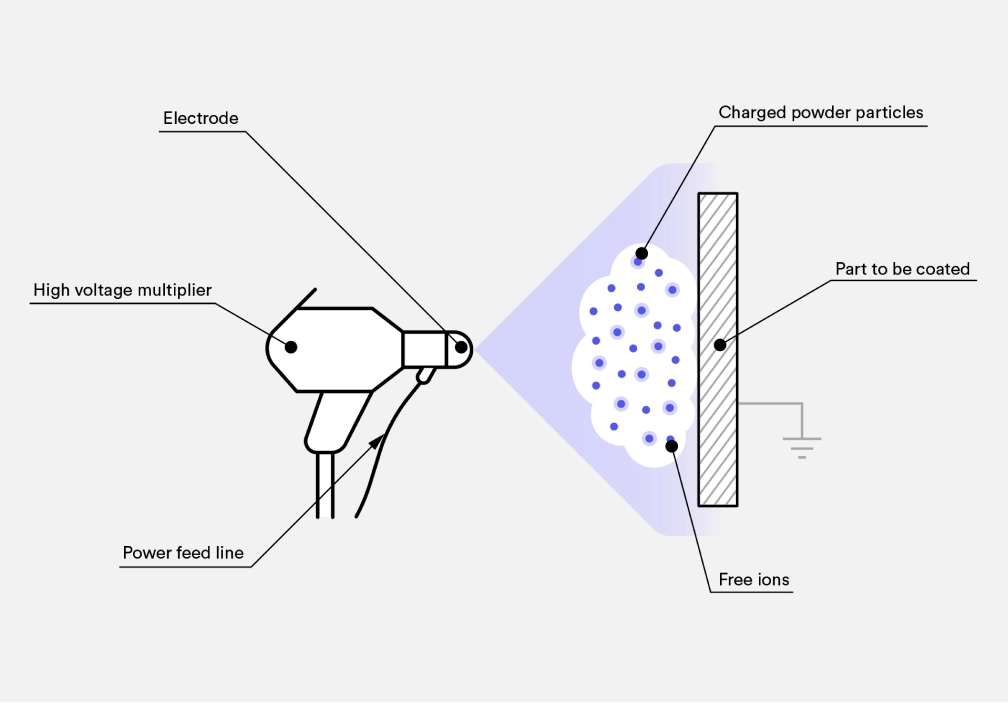
How does powder coating work?
FAQ's
When should you apply powder coating?
What are the best applications of powder coating?
How durable and resistant is powder coating?
How will powder coating affect the price of my part?
What are viable alternatives to powder coating?
Put your powder coated parts into production today
Get instant quote