The Protolabs Network Standard
Quality control
How Protolabs Network controls the quality of your parts
We’ve reinvented cross-docking for quality control
Cross-docking is mostly used to make shipping more efficient. We’ve added a crucial quality control element to our cross-docking process. In addition to extensive quality checks conducted on-site by manufacturing partners, parts of shipments are reassessed by Protolabs Network's source inspectors and/or QC teams at our Amsterdam and Chicago cross-docks when deemed necessary. This applies to many globally sourced orders with an emphasis on critical line items.








Quality control from design to delivery
To ensure our parts always meet the Protolabs Network Standard, we have in-house and on-site quality control (QC) systems and protocols in place. Every custom part gets checked on site by our manufacturing partners according to our guidelines. Depending on the manufacturing location and the complexity of the order, many parts undergo a second-inspection by Protolabs Network's source inspectors and/or at our cross-docks before delivery.

We extensively audit all of our manufacturing partners (MPs) before they can manufacture your parts. All MPs perform in-house quality checks before sending custom parts to our facilities or to their final destinations. We have teams responsible for regular audits across the supplier network, to ensure that every MP is consistently following our standards for production as well as QC.

Alongside our cross-docks in Amsterdam and Chicago, we also have teams actively performing quality checks across the manufacturing network. Our on-site teams in China and India (with more on the way) inspect all outgoing orders, following our comprehensive quality guidelines. If you’d like to receive a full QC report, you can request one when you order your custom parts.

One of the reasons engineers use Protolabs Network is that we take on all the risks for you. If your parts aren’t up to spec, you can file a dispute claim and we’ll remake your components or refund your order. For more detail on how we handle disputes, you can contact our Customer Success Team at networksales@protolabs.com.
Meet the quality control experts
We have a dedicated team of quality control engineers and support staff at our cross-docks in Amsterdam and Chicago and on-site in China and India. These QC teams make sure that all of Protolabs Network's processes run smoothly and efficiently, from quote to production to final delivery.

"I make sure that our quality management systems are aligned to deliver for customers, and to make sure that we meet both internal and external standards as well as regulatory requirements."

“Whenever I get a part in that’s not up to spec, I don’t just solve the part issue, I also help update processes with the team so that we don’t run into the same manufacturing problems in the future.”

“As our manufacturing capabilities evolve, we’re always continuing to improve our quality standards to offer customers the assurance of high quality parts.”

“I make sure that your parts go through rigorous checks here and with our manufacturing partners, so that all components are up to spec before shipping out to you.”
Our cross-docks are equipped to inspect any part
Our cross-docking teams inspect for surface finish quality, threads and gauges, packaging and much more, ensuring your parts meet your exact specifications. To offer the highest grade inspection capabilities, both cross-docks are equipped with state-of-the-art tools.
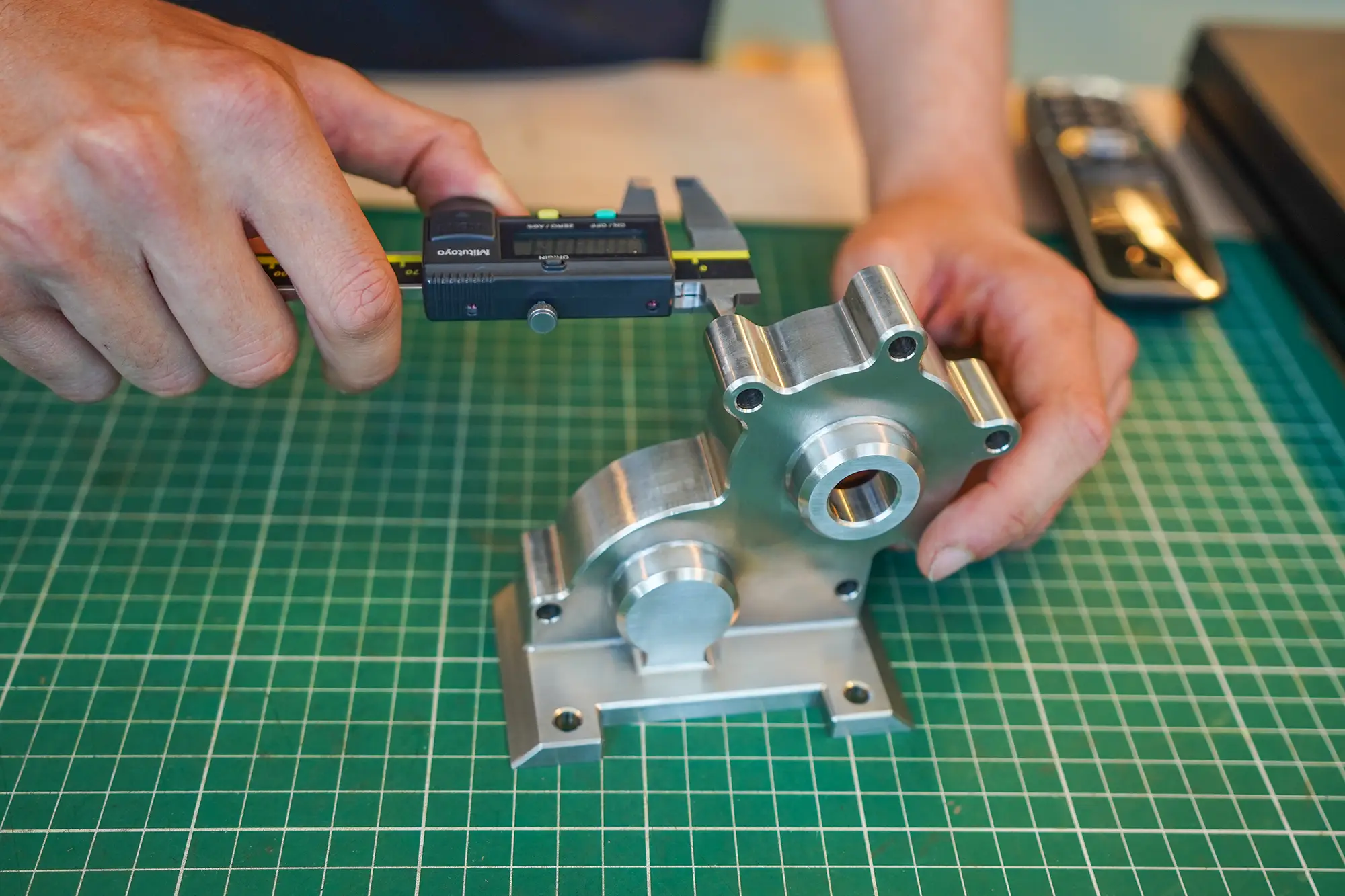
Equipment we use
-
Micro-Vu (optical measurement machine)
-
Calipers and micrometers
-
Gauge blocks
-
Height gauge
-
Feeler gauge
-
Surface roughness meter
-
Pin gauges
-
Protractors
-
Gloss unit meter
-
RAL/Pantone color charts
-
Granite block inspection table
-
Thread, ring and plug Go/No-Go gauges
Your parts are in good hands with us. Start a production project today.
Get an instant quote