Powder coating is a durable and wear-resistant surface finish that you can apply to a huge variety of metal CNC parts. Powder-coated parts appear across tons of applications, including metal furniture, industrial shelving and racking, and more high-performance industrial applications like brake calipers and coil springs for automotive.
Powder-coated metals are durable, corrosion-resistant and cosmetic, and the surface finish is more resistant than paint to chipping, scratching and peeling. However, powder coating is not appropriate in all situations.
This article covers the concepts, parameters, design considerations and process steps of powder coating to make your next CNC machining run swifter and more valuable.
What is powder coating?
Powder coating uses powdered plastic material combined with chemical agents including pigments, flow and leveling agents and other additives to add a robust finish to metal parts.
This powder is sprayed onto a part and adhered electrostatically. The powder coating tool applies a charge to the powder particles, and the part is grounded. This attracts the powder particles to the part. The part is then baked to fuse the powder into a continuous solid coating that is hard, durable, corrosion-resistant and cosmetic, as a wide variety of pigments and surface finishes can be achieved. In some processes, parts are preheated prior to spraying.
A simple way to help understand powder coating is by comparing it to painting. Let’s compare the steps of both finishing processes.
Powder Coating | Spray Painting | |
---|---|---|
Application | Powder particles | Liquid droplets |
Adhesion | Electrostatic | Wetting (some processes utilize electrostatic charge) |
Process endpoint | Particles physically melt and fuse under heat to form a solid coating | Liquid paint dries and chemically cures to form a solid coating |
What are the types of powder coating?
There are three main categories of plastic materials that can be applied via powder coating: thermoplastics, thermosets and UV curable powder coatings.
Thermoplastics are a family of polymer materials, such as PET, Polypropylene and polyester plastics. Thermoplastics are used widely in manufacturing as they melt and flow as liquids, then solidify when cooled. This property makes many manufacturing processes, such as blow molding, injection molding and polymer additive manufacturing possible. This also makes thermoplastics recyclable.
-
Application: not suitable for environments where the temperature is likely to reach their melting point (typically 100-150°C) as upon re-exposure to that temperature they will melt again
-
Materials: nylon, polyvinyl chloride (PVC) and polyester
-
Process: Thermoplastic powders are applied to the work surface and heated, or cured, during which process they melt and flow into a smooth sheet that hardens upon cooling.
-
Can be remolded and reshaped
-
Superb corrosion resistance
Thermosets are the most commonly used category of powder coating materials. These resins are commonly found in automotive parts, such as covers, housings and tires. Thermoset polymers differ from thermoplastics because once set, they can’t be re-melted and flowed into new shapes. This chemical difference is caused by crosslinking to form new thermally stable compounds.
-
Application: used in high-temperature environments, not suitable for sun exposure
-
Materials: epoxy, acrylic, epoxy-polyester and silicon-based powders
-
Process: once melted into a smooth coating on a workpiece, does not melt upon re-exposure to the original melting temperature, because the chemical change it undergoes, called cross-linking, chemically bonds the separate components together during the curing process to create new compounds
-
Cost-effective
-
Cannot be remolded or reshaped
Then you have UV curable powder coatings. With these materials, UV curing replaces the high-heat oven curing used in other powder coating processes. This is useful for materials that can’t withstand high oven temperatures. One key benefit to UV curable powder coatings is a faster curing cycle time.
-
Application: used on heat-sensitive substrates such as wood, plastics and heat-sensitive alloys
-
Materials: photo-polymerized materials with a chemical photoinitiator that instantly responds to UV-light energy, starting the reaction leading to cure.
-
Process: to cure a UV-powder coating, a separate melt stage precedes the curing stage, which typically takes 1-2 minutes or longer, depending on the substrate. UV curing is almost instantaneous.
-
Fast curing, higher line speeds and higher productivity can be achieved.
-
Metal parts can be combined with heat-sensitive parts.
Curious about the cost and capabilities of powder coating at Hubs?
What are common applications of powder coating?
Today, powder coating is one of the most common finishing processes, used in building construction, automotive parts, furniture, appliances and even road signs. Powder coating may be more expensive for some applications than paint, but if the part requires a high-durability finish, powder coating will perform better over the life of the product than paint.
Thanks to its resistance to high temperatures, corrosion and cleaning products such as alkaline chemicals and abrasive scouring products, powder coating is ubiquitous on consumer appliances such as stoves, washing machines and refrigerators.
What’s the ideal thickness for powder coating?
Powder coating thickness is measured in mm, with 1 mm = 25.4 μm or approximately 1 thou (1/1000”). And while it may be intuitive that a thicker coating delivers better durability, this is not always the case.
Thicker coatings exceeding 6 mm can lose flexibility, causing undesirable orange peel effects and increasing the chance of failures such as chipping and cracking. On the other hand, coatings too thin (less than 2 mm for most coatings) may result in incomplete coverage, exposing the substrate to corrosion and reducing resistance to abrasion and other damage.
For most coatings, the ideal coating thickness is between 2 mm and 3 mm, with some coatings reaching up to 6 mm. These thicknesses deliver the best performance and appearance, depending on your application.
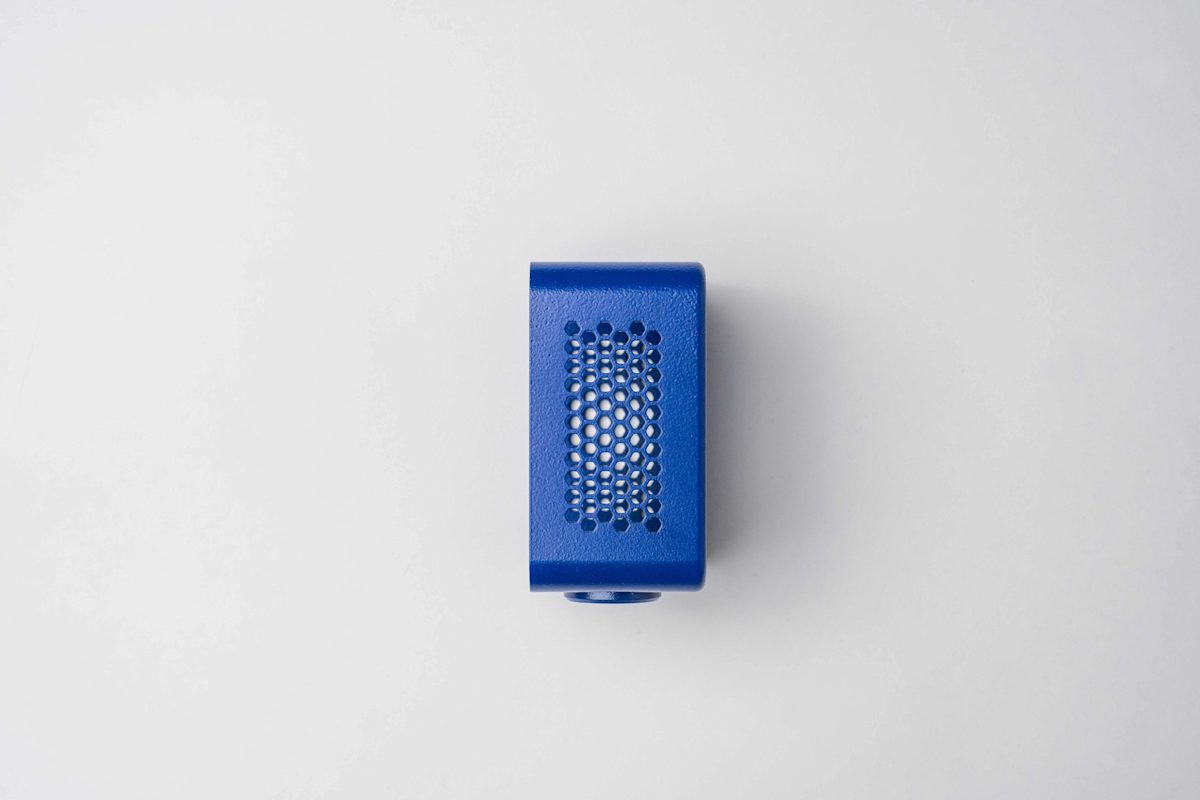
What equipment do manufacturers need for powder coating?
The basic pieces of equipment required for powder coating include a powder coating booth, power feeder, electrostatic gun, power unit and powder coating oven.
While these pieces of equipment may have higher initial costs than some painting processes, the cost may be lower than painting in the long run as the powder can be used more efficiently than paint, with less waste, and fewer costs related to solvents, primer, surface coatings and sealants.
Because of the high durability and toughness of powder coating, it is often used for white goods, some automotive and heavy equipment parts, furniture, and other heavy-duty parts and products that have to withstand the elements and resist damage to the coating.
How does powder coating work? A step-by-step guide
These steps overview the basic process of powder coating. Of course, this isn’t the only way to powder coat parts. Other powder coating processes may involve preheating, dipping parts in a tank of fluidized powder, or other methods. However, the fundamentals remain the same: coat the part in powder and flow the powder into a cured, continuous coating.
Pretreatment
-
Chemical treatment: Parts are first cleaned using an alkaline, acidic or neutral cleaner. Pretreatments most often used in powder coating are:
-
iron phosphate for steel (pH 4.5-5.5)
-
zinc phosphate for galvanized or steel substrates (pH 1.5-3.5)
-
chromium phosphates or non-chrome treatments for aluminum substrates
-
-
Mechanical treatment: sand or shot blasting can be used to develop an anchor pattern on the part that improves the adhesion of the powder coating to the substrate.
-
Particularly useful for removal of inorganic contaminants such as rust, mill scale and laser oxide.
-
-
Parts are dried in a low-temperature dry-off oven and are ready to be coated
-
To remove any chemical used to clean and treat the surfaces, parts are rinsed. In a dip tank or wash line this will typically be done with neutralized water and then a slightly acidic solution to seal the surface. If parts are cleaned manually, a solvent like acetone is suitable to be used after the sandblasting
Powder application
Let's break down the different types of powder application methods in greater detail.
Fluidized bed coating
-
Used for coatings between 10-15 mm (255-380μm)
-
The film can be applied in thickness from a minimum of 8 to 125 mm (200-3170μm)
-
This process requires pre-heat temperatures of at least 180° C
-
Normal immersion times: 2-8 seconds
-
Thick coatings: 10-30 seconds
-
Typical Uses: bus bars, fabricated wire, metal furniture, raceways
-
Steps:
-
Part pre-heated to 200°-230° C
-
Initial deposit melts onto part
-
Film builds from residual heat
-
Coated part with desired film
-
Electrostatic fluidized bed coating
-
Coatings range: 0.8-3 mm (20-76μm)
-
The effective coating range is only 7-10 cm over the bed and will not coat parts with deep recesses
Electrostatic spray
-
Used for coatings between 0.8-10 mm (20-250μm)
-
Spray device with a powder delivery system and electrostatic spray gun
-
High transfer efficiency
Curing
-
Thermoset powder:
-
Temperature: 150-200°C
-
Time: 10-20 minutes
-
-
Thermoplastic powder: no cure time
-
UV curable powder:
-
Temperature: 90-150°C
-
Time: seconds
-
What are the cosmetic options for powder coating?
Color
Colors in coatings are created with combinations of chemical pigments to the base formulation (color match is usually done using RAL paint color codes). The pigment itself isn't enough to describe the color of a coating, as variables like gloss and texture influence that too.
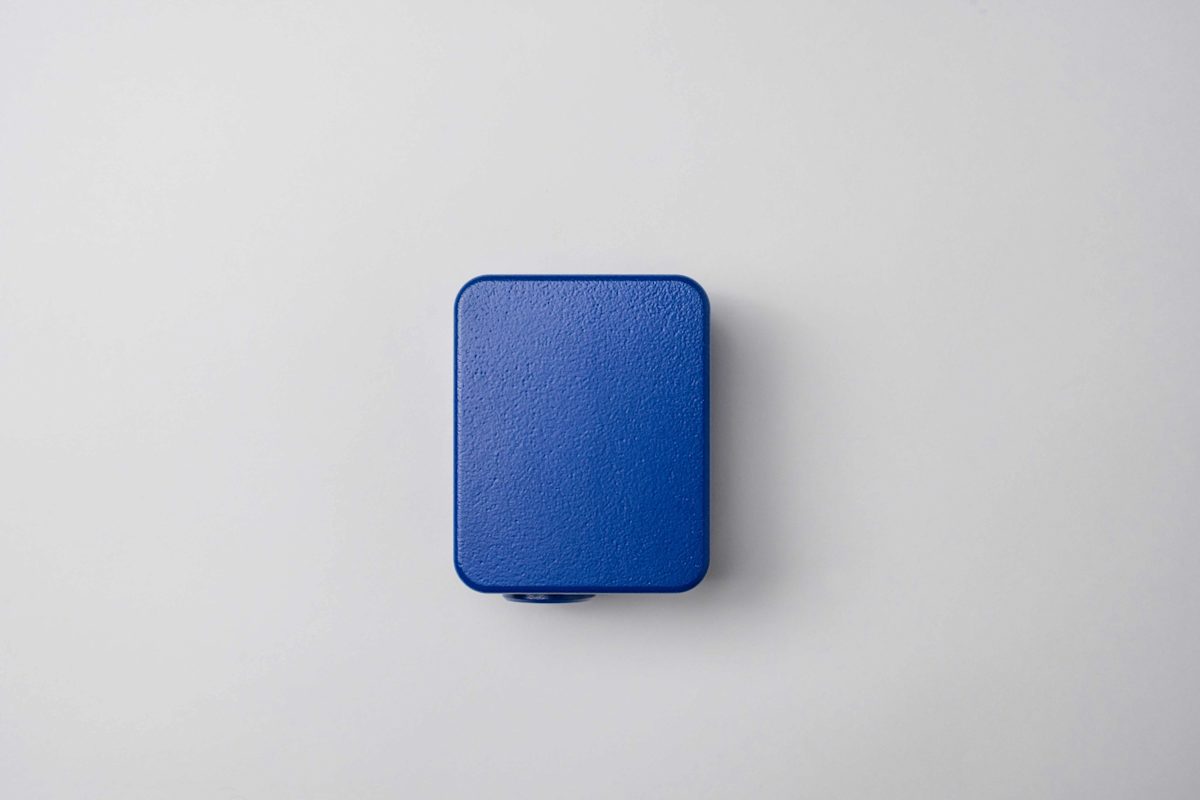
Gloss
-
Gloss level: amount of unscattered light reflected from the surface of the object
-
Measurement: measured using a gloss meter by directing a constant intensity light beam, at a fixed angle, onto the test surface and then monitoring the amount of reflected light from the same angle
Different surfaces require different reflective angles. An incident angle of 60° is often used, although 20° and 80° measurements have limited use too. Gloss level is often described as a percentage, however, Gloss Units (GU) is the more accurate description.
Gloss is directly related to the PVC (Pigment Volume Concentration) of the product. As the percentage of the pigment in a coating increases, the gloss level decreases. The lower the percentage of pigment in the coating, the higher the gloss will be.
Matte
-
Gloss level: <30 (+/- 5%)
-
Flat coatings diffuse light and help to hide surface imperfections
-
More prone to dirt pickup and staining so they are typically used in areas that are not exposed to a high degree of dirt or staining compounds, reducing the amount of cleaning required and extending the life of the coating.
Glossy
-
Gloss level: ~70(+/- 5%)
-
It is easier to clean that a matte finish and provides less surface friction
-
Gloss coatings contain more resin (binder) and less pigment than a matte coating. Semi-gloss coatings bring improved resistance to stain, dirt pickup, and have a higher resistance to abrasion than a flat coating.
High gloss
-
Gloss level: above 80 (+/- 5%)
-
Very shiny and reflective and also not too suitable for hiding surface imperfections
-
Full gloss coatings contain the most amount of resin
-
The high gloss surface is much smoother and is the most resistant to abrasion when being cleaned. While a gloss coating tends to enhance surface imperfections, they are more durable and are resistant to staining and dirt pickup.
What finishes are available for powder coating?
Standard
-
Various colors and gloss levels are achievable
-
No signs of orange peel
-
Most powder-coated finishes are between 60-80 μm thick (after cure)
Wrinkles
-
Typically a polyester or urethane chemistry, occasionally an epoxy
-
Decent weathering, good hardness, corrosion resistance, chemical resistance, great special effect for covering up surface imperfections
-
Wrinkle textures are not compatible with glosses
Sand texture
-
Fine textures(as sand texture) are powders with a texture added in alongside the pigmentation
-
Not compatible with glosses above 20 GU
Hammer texture
-
A hammer texture looks similar to a golf ball or an orange rind
-
More likely to be paired with a higher gloss
-
This textured surface is more resistant to abrasion, chipping, scratching, fading, chemical corrosion and wearing than other finishes
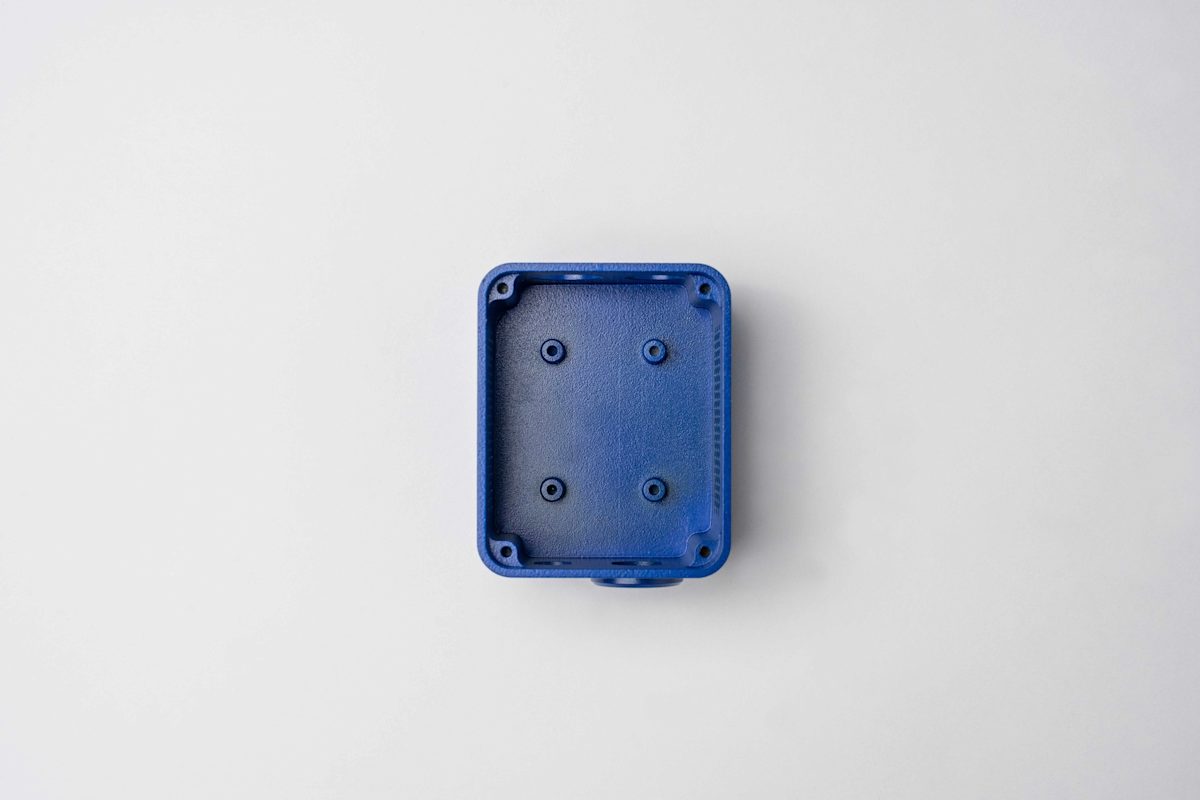
How do you design parts for powder coating?
Part geometry
Part geometry impacts powder coating feasibility. For example, as with painting, it can be difficult or impossible to coat surfaces that are not easily accessible with the spray pattern. For example, if the inside surface of the tubing or a blind hole needs to be coated, it may be better to consider a dipping process over a spraying process. Areas to be coated must have a “line of sight” to the gun.
Typically, the design process for powder coating includes breaking all sharp edges with a radius or chamfer, as electrostatically charged particles may not properly adhere to sharp corners. The thickness of the powder coating must also be considered in the design, especially for moving parts or parts with precise tolerances in assembly.
Because of the physics of the electrostatic application, some areas of certain part geometries may not properly attract the negatively charged particles. This defect is known as a “faraday cage.” This effect commonly occurs on inside corners or partially closed geometry, where the electrical charges can’t uniformly move through the metal. This effect can occur to parts with perfectly acceptable geometry for the powder coating process, however, and requires skilled operators and correct process parameters to overcome.
Masking
It’s necessary to mask areas that are not to be coated, such as mating surfaces or tapped holes. Masking is also important for features with tight tolerances, given the thickness of the coating. However, masking for powder coating differs from masking for painting, mainly because the parts will be baked at high temperatures.
Typically, areas to be masked are cleaned, either mechanically by media blasting or with chemical agents. Next, high-temperature masking tape is applied. Masking tape is removed immediately after baking. Holes to be masked can be plugged with silicone plugs, sealing and protecting the threads. Bosses, bolts, caps rods and studs can be capped.
Mounting parts for spraying
It’s also critical to consider the design of the racking which holds parts for spraying. For example, parts must make good contact with the electrical ground. Electrostatic forces are fields and can interact in unexpected ways. For example, if parts are too close together, the powder may not adhere evenly to the part.
How will parts be hung for spraying? Areas where mounting hardware, such as wire or hooks, contact the part will of course not be fully exposed to powder coverage. In designing your part, consider the placement of holes for hanging, airflow, and access for the gun. These holes may be added for the explicit purpose of coating, or existing holes in the design can be used.
Ready to start sourcing custom CNC-machined parts?
Our online CNC services Upload a CAD file for a free, instant quote
Frequently asked questions
What are the advantages of powder coating?
Powder coating is a surface finishing option with many distinct advantages. It uses coating material very efficiently, especially as overspray is collected and reused. It doesn’t release VOCs like some paints and solvents and has high durability compared to other finishes. Powder coating protects against corrosion and is a one-step coating.
Does powder coating have disadvantages?
Despite its robustness and versatility, powder coating does have disadvantages for certain applications. It’s often challenging to apply thin films of the coating, depending on the machining material, and may not perform comparatively well as a fine aesthetic finish. On the manufacturing side, powder coating comes with high startup costs related to equipment, such as specialized ovens, spray guns, booths and the powdered resin material itself.
What are viable alternatives to powder coating?
An alternative to powder coating is wet painting, however, paint doesn’t offer quite as many resistances as powder coating.
Is powder coating a better surface finish than paint?
Overall, powder coating performs better than paint. Thanks to thermal bonding and thicker layers, it’s more resistant to wear and tear like chipping and scratching.
How long does powder coating last on metal parts?
Powder coating can last quite a while (up to 20 years), though different types of coatings vary in just how long they remain pristine and protective. Factors like consistent use (both indoors and outdoors) and exposure to UV light will reduce how long powder coating lasts on your parts.
When should you apply powder coating?
Powder coating provides a cost-effective, tough and durable finish on your parts that increases their longevity and resistance to harsh environments, such as marine applications.
What are the best applications of powder coating?
Powder coating makes metal parts resistant to outdoor conditions, such as heat, cold damage and corrosion. You’ll likely find powder coating on tractors or other farming equipment, industrial machinery parts and high-use automotive parts.
How durable or resistant is powder coating?
Powder-coated parts typically resist 20 years of wear, but due to the consistent use, exposure to UV light, and outdoor environment, the finish may break down faster.