SLA (Stereolithography) 3D printing can produce plastic parts with high resolution and accuracy, fine details and smooth surface finishes. Thanks to the variety of resins available for SLA, this manufacturing process is popular among many industries for a variety of applications.
Standard resins, for instance, are often used for general prototyping and engineering resins are chosen for applications requiring specific mechanical and thermal properties. Dental and medical resins come with biocompatibility certifications,
In this article, we explore the most common SLA material options to highlight the key advantages of each and give actionable guidelines to help you choose the right one for designing custom parts with SLA.
What materials are available for SLA 3D printing? What do SLA resins do best?
SLA uses a UV laser to cure liquid resin into hardened plastic in a process called photopolymerization. Different combinations of monomers, oligomers, photoinitiators, and various other additives that comprise a resin result in different material properties.
SLA produces parts from thermoset polymers. Here are the main benefits and limitations that are common to all SLA materials:
Pros
Cons
In the following sections, we will go deeper into material properties that are specific to each SLA resin.
Curious about the cost and the available material options of SLA?
What are the standard SLA resins? Common 3D printing materials
Standard resin
Standard resins produce high-stiffness, high-resolution prints with a smooth injection molding-like finish. Their low cost makes them ideal for prototyping applications.
The color of the resin affects its properties. For example, grey resin is better suited for parts with fine details, and white resin for parts that require a very smooth surface.
Standard resin is ideal for concept modeling, rapid prototyping and using 3D printing for more artistic endeavors.
Pros
Cons
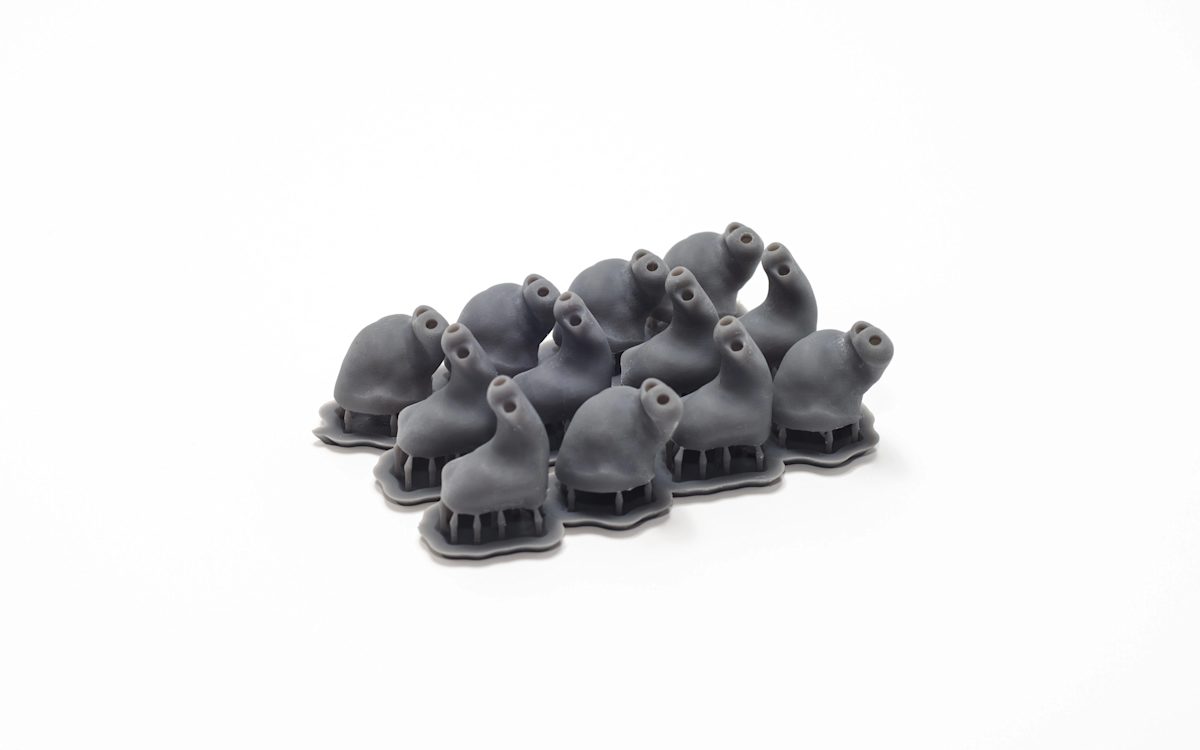
Clear resin
Clear resin has similar mechanical properties to standard resin but can be post-processed to near optical transparency. More information on post-processing SLA parts can be found here.
Clear resin is ideal for showcasing interior features, housings for LEDs and fluidic devices.
Pros
Cons
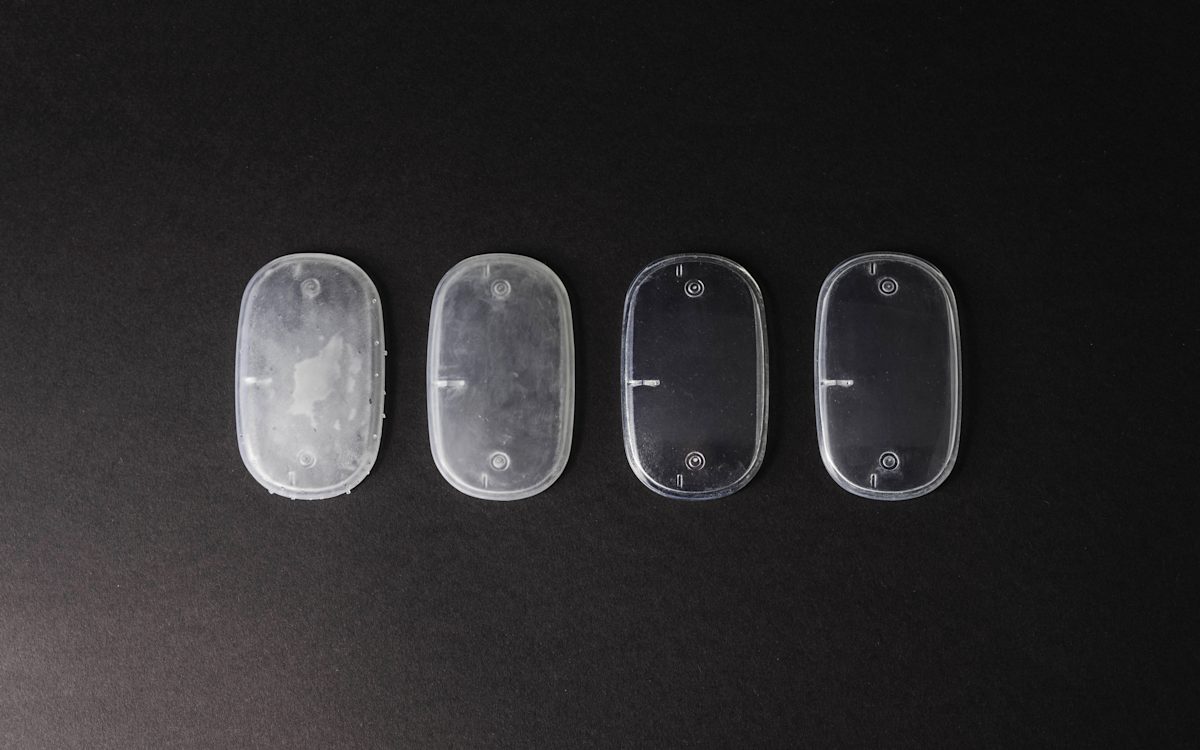
What are engineering SLA resins? 3D printing materials for production
Engineering resins simulate a range of injection-molded plastics to provide engineers with a wide choice of material properties for prototyping, testing and manufacturing.
All engineering resins require post-curing under UV light to reach their maximum mechanical properties.
Tough resin (ABS-like)
Similar to ABS, tough resin was developed for applications requiring materials that can withstand high stress and strain. Parts printed in tough resin have tensile strength (55.7 MPa) and modulus of elasticity (2.7 GPa) comparable to ABS.
This material will produce sturdy, shatter-resistant parts and functional prototypes, such as enclosures with snap-fit joints, or rugged prototypes.
Tough resin is ideal for functional prototypes and mechanical assemblies.
Pros
Cons
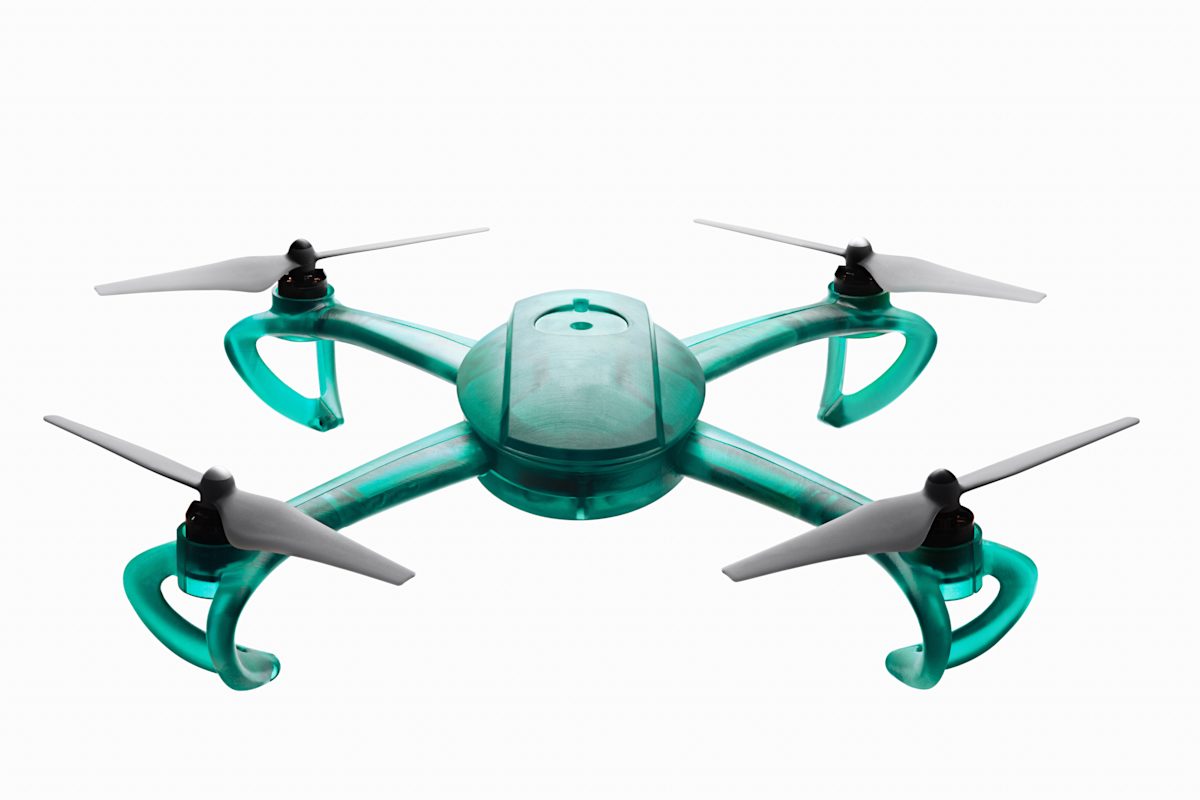
Durable resin (PP-like)
Durable resin is a wear-resistant and flexible material with mechanical properties similar to Polypropylene (PP).
Durable resin can be used for parts that require high flexibility (high elongation at break), low friction and a smooth surface finish. Durable resin is particularly fitting for prototyping consumer products, snap fits, ball joints and low-friction moving parts.
This material is optimal for functional prototypes, consumer products, and low-friction and low-wear mechanical parts.
Pros
Cons
Heat-resistant resin
Heat-resistant resin is ideal for applications that require high thermal stability and the ability to operate at high temperatures.
These resins have a heat deflection temperature between 200-300°C and are ideal for manufacturing heat-resistant fixtures, mold prototypes, hot air and fluid flow equipment, and casting and thermoforming tooling.
Heat-resistant resin is ideal for mold prototyping, casting and thermoforming tooling.
Pros
Cons
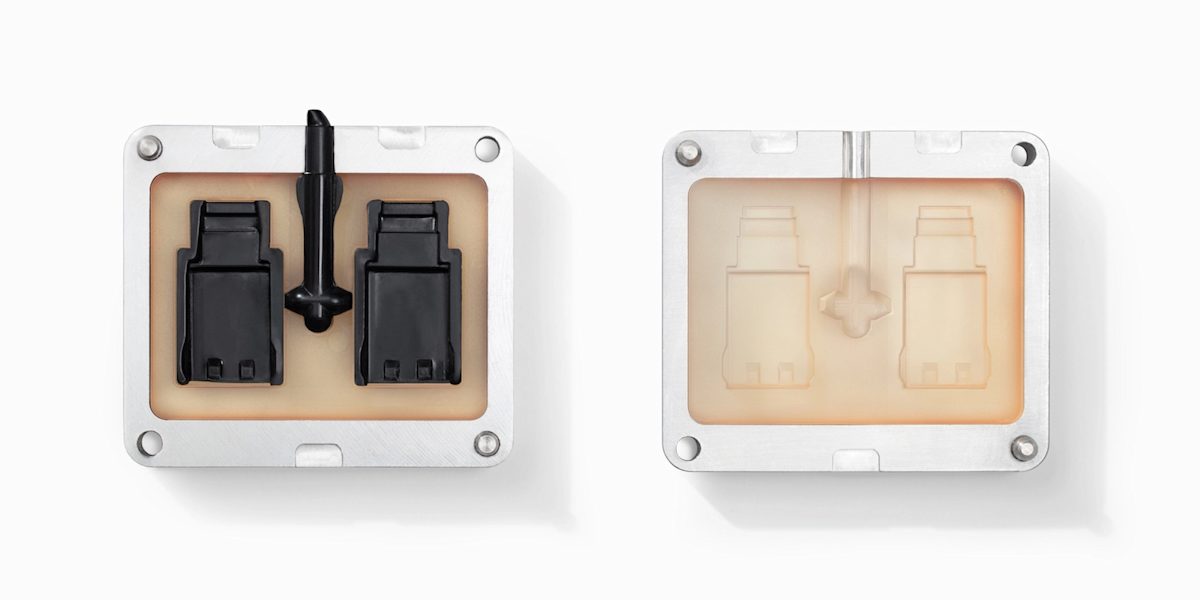
Rubber-like resin (flexible)
Rubber-like resin allows engineers to simulate rubber parts that are soft to the touch. This material has a low tensile modulus and high elongation at break, and it is well-suited for objects that will be bent or compressed.
It can also be used to add ergonomic features to multi-material assemblies, like packaging, stamps, wearable prototyping, handles, overmolding and grips.
Rubber-like resin can produce parts with low hardness and high flexibility but lack the performance of true rubber. This material is ideal for wearables prototyping, multi-material assemblies, handles, grips and overmolding.
Pros
Cons
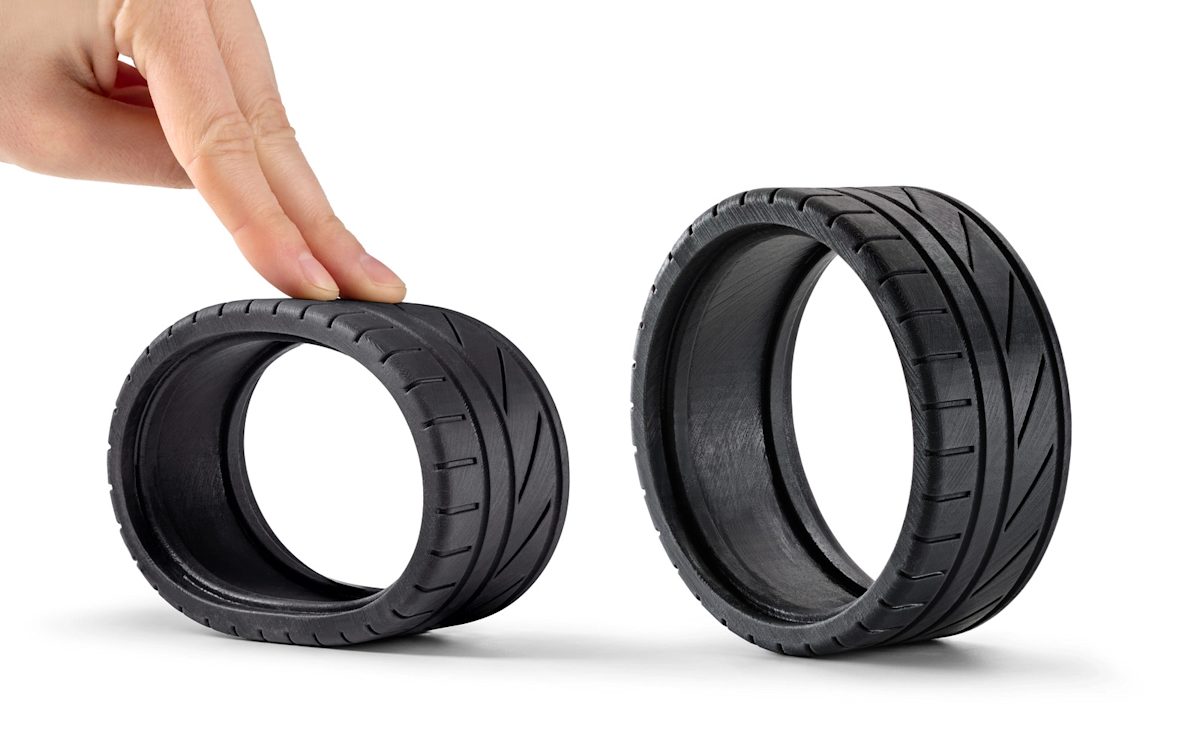
Ceramic-filled resin (Rigid)
Rigid resins are reinforced with glass or other ceramic particles and result in very stiff and rigid parts, with a very smooth surface finish.
Rigid resins offer good thermal stability and heat resistance (Heat Deflection Temperature HDT @ 0.45MPa of 88°C). They have a high modulus of elasticity and lower creep (higher resistance to deformation over time) compared to other SLA resins but are more brittle than the tough and durable resins.
Rigid resin is also suitable for parts with thin walls and small features (the recommended minimum wall thickness is 100 µm).
It's ideal for molds and tooling, jigs, manifolds, fixtures, electrical application housings and automotive parts.
Pros
Cons
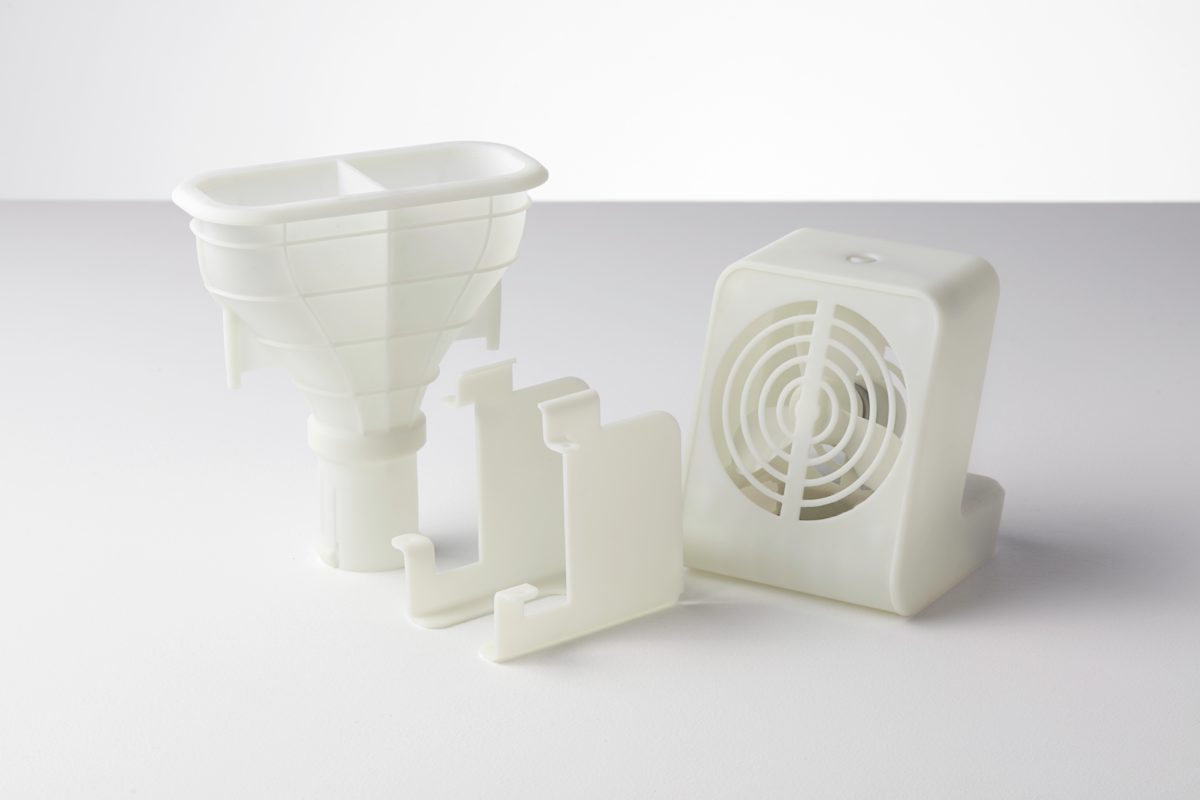
What's the right resin for your application? Comparing 3D printing materials
The table below summarizes the basic mechanical properties of the common SLA materials.
Standard & Clear | Tough | Durable | Heat resistant | Ceramic reinforced | |
---|---|---|---|---|---|
IZOD impact strength (J/m) | 25 | 38 | 109 | 14 | N/A |
Elongation at break (%) | 6.2 | 24 | 49 | 2.0 | 5.6 |
Tensile strength (MPa) | 65.0 | 55.7 | 31.8 | 51.1 | 75.2 |
Tensile Modulus (GPa) | 2.80 | 2.80 | 1.26 | 3.60 | 4.10 |
Flexural Modulus (GPa) | 2.2 | 1.6 | 0.82 | 3.3 | 3.7 |
HDT @ 0.45 MPa (oC) | 73 | 48 | 43 | 289 | 88 |
Standard resin has high tensile strength but is very brittle (very low elongation at break), so it is not suitable for functional parts. The ability to create fine features makes it ideal though for visual prototypes and art models.
Durable resin has the highest impact strength and elongation at break compared to the other SLA materials. It is best for prototyping parts with moving elements and snap-fits.
Tough resin is a compromise between the material properties of durable and standard resin. It has tensile strength, so it is best suited for rigid parts that require high stiffness.
Heat-resistant resin can withstand temperatures above 200 degrees Celcius, but has poor impact strength and is even more brittle than standard resin.
Ceramic resin has the highest tensile strength and flexural modulus but is brittle (poor elongation at break and impact strength). It should be preferred over other engineering resins for parts with fine features that require a high stiffness.
The following graphs represent the mechanical properties of the most common SLA materials (courtest of Formlabs).
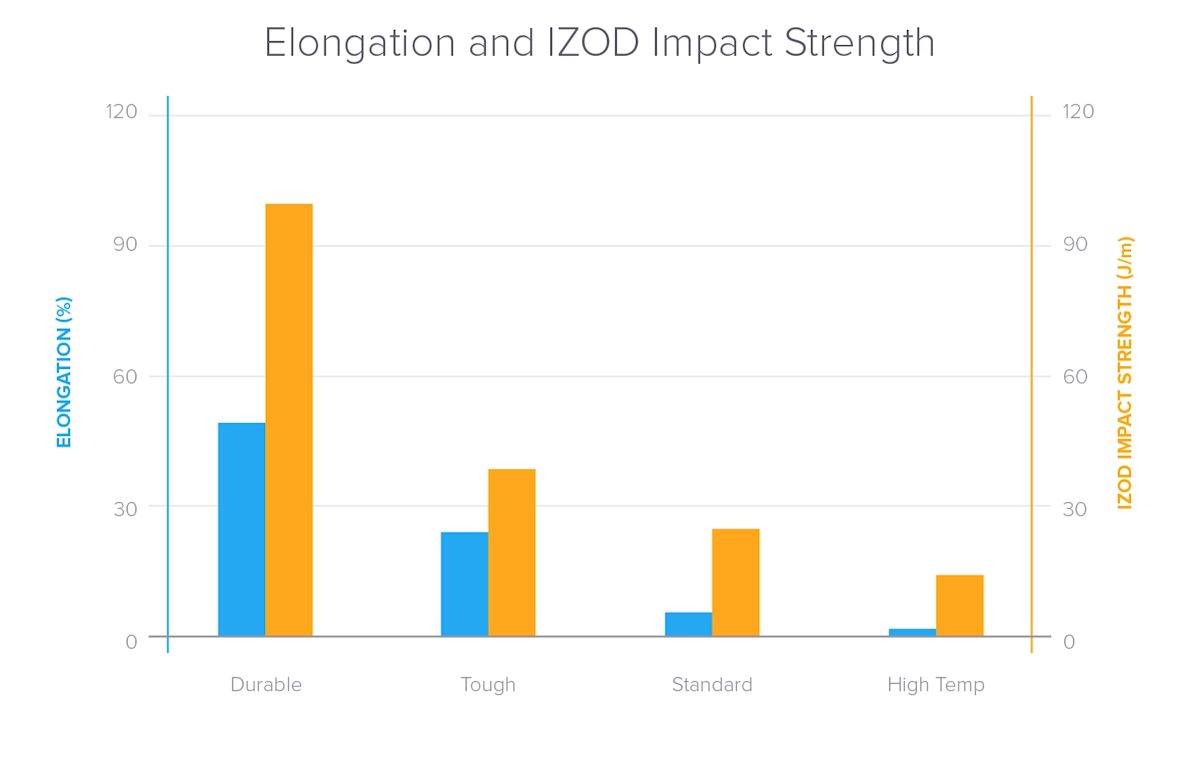
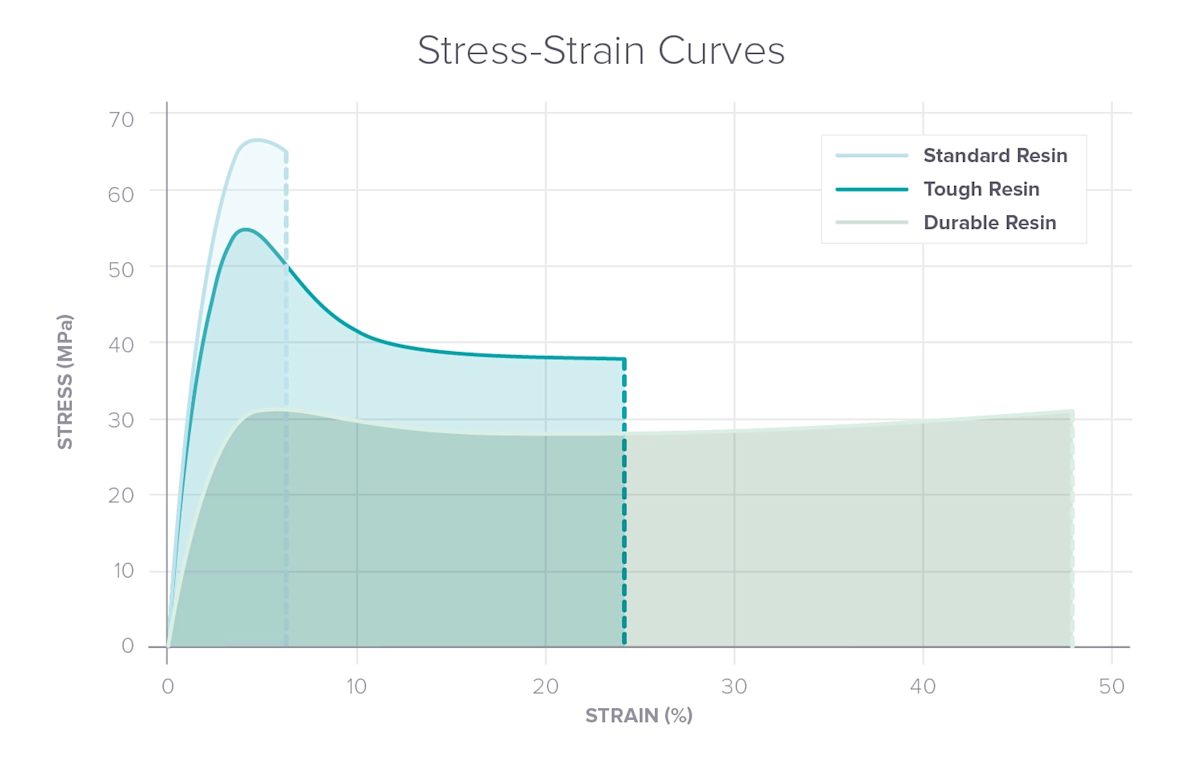
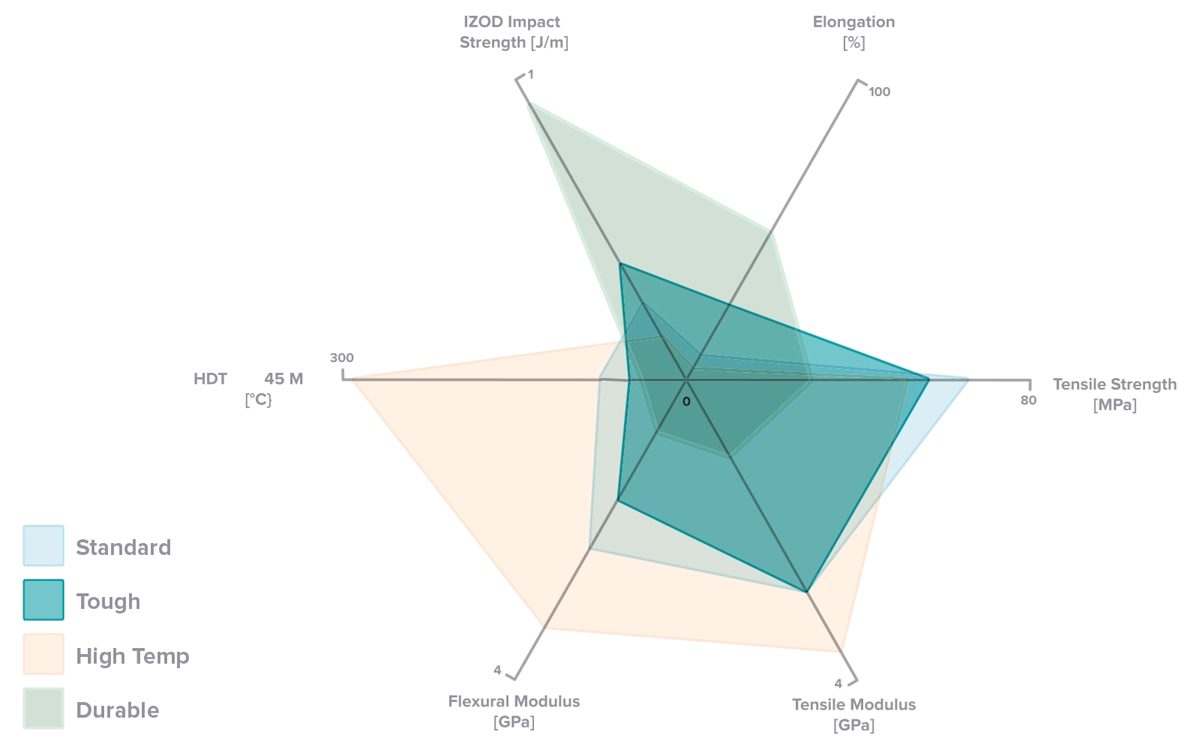
What are dental & medical SLA resins? 3D printing materials with biocompatibility
Custom medical appliances resin (class I biocompatible)
Class I biocompatible resins can be used to make custom medical equipment, such as surgical guides. Parts printed in this resin can be steam sterilized using an autoclave, for direct use in the operating room.
These materials are optimal for producing surgical aids and appliances.
Pros
Cons
Dental long-term biocompatible resin (class IIa biocompatible)
This resin is specially engineered for long-term orthodontic appliances. Class IIa biocompatible resins can be in contact with the human body for up to a year.
Their high resistance to fracture and wear make them perfect for producing custom hard splints or retainers.
It's ideal for manufacturing long-term dental appliances, fracture- and wear-resistant medical parts, hard splits and retainers.
Pros
Cons
What's the difference between Class I and Class IIa biocompatibility?
Class I biocompatibility regulations refer to materials that are allowed to be used for:
-
non-invasive devices that come in contact with intact skin
-
appliances for transient use or short-term use in the oral or ear canal or in nasal cavities
-
reusable surgical instruments
Class IIa biocompatibility regulations refer to materials that are allowed to be used for:
-
devices that come in contact with body fluids or open wounds
-
devices used to administer or remove substances to and from the human body
-
invasive short-term devices, such as invasive surgical elements
-
long-term implantable devices placed in teeth
What are castable SLA resins?
Castable resin for jewelry making
This material enables printed parts with sharp details and a smooth finish and will burn out cleanly without leaving ashes or residue.
Castable resin allows the production of parts directly from a digital design to investment casting through a single 3D-printed part. They are suitable for jewelry and other small and intricate components.
As the name suggests, this castable resin is great for investment casting and producing jewelry.
Pros
Cons
Ready to start 3D printing custom parts?
Our SLA 3D printing services Upload your design for a free quote
Frequently asked questions
What’s the best SLA material for prototyping?
We recommend that you choose standard resin for prototypes with a smooth injection molding-like surface finish.
What’s the best SLA material for functional prototypes?
For functional prototypes, choose tough resin if stiffness is your main design requirement, durable resin for parts that need higher impact resistance or have moving parts and ceramic reinforced resin for parts with fine features.
What temperatures can heat-resistant resin withstand?
Heat-resistant resin can withstand temperatures above 200 degrees Celsius but is brittle.
What SLA materials are safe for medical and dental applications?
Class I biocompatible resins are suitable to come in external contact with the human body, while Class II biocompatible resins are suitable for short-term use devices.
What are SLA materials and resins made of?
While FDM raw materials come in spools of solid filament, SLA materials combine short chains of carbon molecules into lengthier chains to become hardened plastic, thanks to a photochemical process. These are photosensitive mixtures of oligomers and monomers that make up liquid resins.