In this article, we’ll help you do so, focusing on how different manufacturing methods – namely CNC machining, injection molding, and die casting – have different advantages and disadvantages when creating large quantities of parts. This will help you lay a foundation on which you can develop a plan for high-volume production.
What is high-volume production?
Higher-volume or mass production involves the large-scale manufacture of standardized parts or products. Higher-volume production usually involves production or assembly lines, which can be continuously active, 24 hours per day, seven days per week (this would be known as “continuous production”). This type of manufacturing is used to create a huge variety of parts intended for end-use from cars to smartphones – or anything else that is sold or used by the thousands (or even millions).
What are the characteristics of high-volume production?
High-volume production is generally efficient, consistent, and allows manufacturers to scale up production to meet high demand. Below are several of its major characteristics, which can be both
-
Economies of scale. Large batches of parts result in reduced cost per unit. This is because fixed costs are spread across the entire run.
-
Automation. Machinery and automated processes increase production speed and reduce the need for manual labor – and are thus hallmarks of high-volume production.
-
Standardization. High-volume production works best for products that don’t require frequent changes or customization.
-
Consistency and quality control. Standardized processes help result in parts that are uniform and of the same quality.
-
Supply chain efficiency. High-volume production often involves streamlined supply chains, which help reduce waste and optimize resources.
-
Up-front investment. Manufacturing large quantities of parts usually requires a significant initial investment in machinery, equipment, and infrastructure. This is typically offset by lower production costs in the long run.

What manufacturing methods are best for high-volume production?
When choosing a manufacturing method for high-volume production, the material you want to use, your part’s complexity and properties, the amount you need to manufacture, and any cost considerations will all play a factor in your decision. Here, we’ll take a look at three manufacturing methods we see our customers use for high-volume production, providing you with scenarios in which they could be viable options.
When to use injection molding for high-volume production
Injection molding is perhaps the most common form of manufacturing for high-volume production. Here is when you should use it.
-
Plastic parts. Injection molding is the go-to method for producing large quantities of plastic parts. It can handle a wide range of plastic materials, and is used for applications that run the gamut, from consumer products to industrial components.
-
Undercuts. Plastic parts with undercuts – as well as thin walls or otherwise complex geometries – may be challenging to achieve with other manufacturing methods, but injection molding can more easily handle them. You can also use multi-cavity molds to create multiple parts in a single production cycle.
-
Consistency and uniformity. Injection molding can ensure that each part in a production run is identical, as molds are very precise and the process is highly repeatable.
-
High-quality surface finish. Parts produced by injection molding can have excellent surface finishes straight out of the mold, reducing the need for post-processing. You can also directly apply textures and surface patterns to parts.
-
Speed and efficiency. Once you have designed and created a mold, the injection molding process itself is very fast, meaning you can rapidly create large volumes of parts. This makes injection molding a great choice for industries with high demand and tight production schedules.
When to use die casting for high-volume production
Die casting offers many of the benefits of injection molding, but is better suited to metal parts. Let’s take a closer look.
-
Metal parts production. Die casting is ideal for producing large quantities of metal parts, especially with non-ferrous metals like aluminum, zinc, and magnesium. It is often used to create parts that are strong, durable, and lightweight.
-
Thin walls. You can use die casting to create metal parts with thin walls or other intricate details that would be difficult to achieve with other metal forming processes.
-
Dimensional accuracy and stability. Die casting offers excellent dimensional accuracy and stability, which means it’s a great choice should your parts need to exhibit precise and consistent dimensions, such as in applications where parts must fit together very accurately. For parts that require exceptionally high degrees of accuracy, however, consider having your parts CNC-machined after casting.
-
Strength and durability. Die cast parts are known for their strength and durability. Parts created with the process can withstand high stress and harsh conditions, making them suitable for demanding applications in industrial environments. However, parts created with CNC machining are often stronger and more durable.
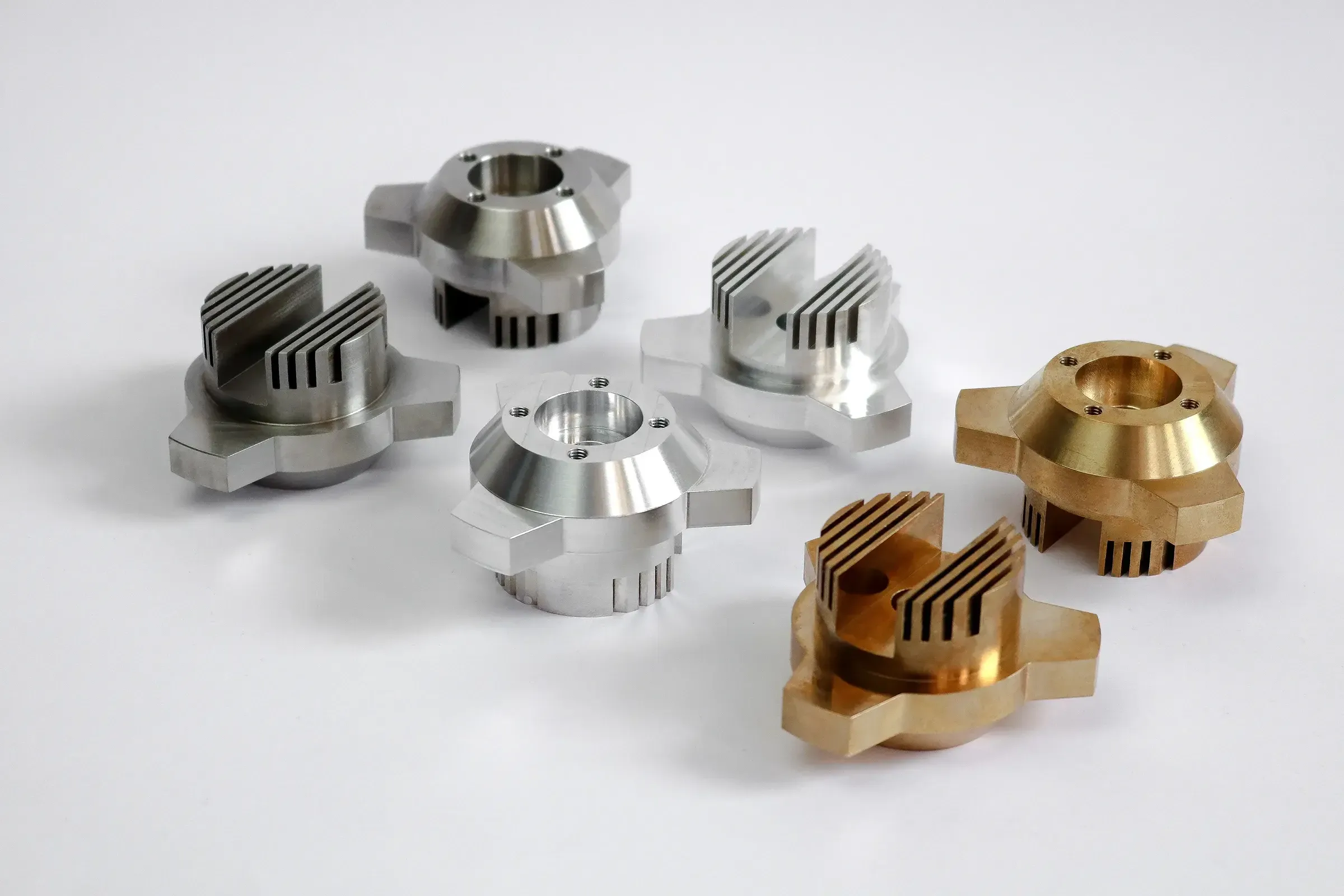
When to use CNC machining for high-volume production
CNC machining is typically used for low- to medium -volume production, as it is more costly and has longer lead times compared to injection molding and die casting. That said, you may want to consider using CNC machining for high-volume production in the following cases.
-
High precision and tight tolerances. If your parts must be extremely prices, or have very tight tolerances, you may want to consider CNC machining, as it is capable of degrees of accuracy that even injection molding can’t achieve.
-
Material variety. Whereas die casting and injection molding require different molds for different material types, CNC machines can handle a wide variety of materials, including metals and plastics. If your parts need to be made of different materials (for instance, a part which is half made of steel and half of nylon), CNC machining can offer the versatility you need.
-
Customized or changing parts. Similarly to above, in cases where your parts require frequent modification or customization, CNC machining is more adaptable. Unlike injection molding or die casting, where altering the design requires expensive and time-consuming modifications to molds or dies, CNC machining can accommodate changes quickly and cost-effectively.
Order parts at high-volume production
Do you want to create large batches of parts? Find out how we help you to scale up to production quantities. You can also read more about designing for product scalability and design for manufacturability (DFM). For single parts, get an instant quote and lead times by uploading a CAD file to our Quote Builder.
Frequently asked questions
What role does automation play in high-volume production?
Automation can boost efficiency, precision, and speed in high-volume production, as well as significantly reducie human error.
What are the challenges of high-volume production?
High-volume production presents challenges: high initial capital investment (unless you are working with a manufacturing partner), machinery maintenance, and supply chain management.
How is quality control maintained in high-volume production?
Quality control in high-volume production is maintained by implementing statistical process control (SPC) and automated inspection systems.
How is inventory managed in high-volume production?
Inventory in high-volume production is often managed using just-in-time systems, which helps minimize storage costs and waste.