Medical device manufacturing: Best practices, applications and regulations
Learn about the processes used to manufacture medical devices and which applications they're relevant to, as well as best practices to follow when designing medical devices.

Introduction
The term medical device covers an extensive range of applications from tongue depressors and latex gloves to x-ray machines and further to custom hearing aids and biomedical implanted devices such as heart valves. Traditional manufacturing processes including CNC machining and injection molding are typically used for the many existing medical devices such as prosthetics, surgical tools, and general equipment/tools used by medical professionals.
The field of medical device manufacturing is rapidly growing and, given the advantages offered by additive manufacturing – highly customizable geometry, low-cost, and a wide variety of possible materials – these processes are well suited to fill the demand for the emerging needs of medical device manufacturing.
This article covers the processes commonly used to manufacture medical devices, as well as applications, best practices to follow and regulations to pay attention to when designing and manufacturing medical devices, in addition to a quick look forward to what the future of medical device manufacturing could look like in a few years. Feel free to skip through to specific sections using the list below.
Skip to
Processes used to manufacture medical devices
Whether additive manufacturing or traditional manufacturing processes is the best solution for medical devices depends on a number of factors including overall schedule and application. Critical questions should be considered such as:
- Is this a unique or low volume part?
- Is the part geometry complex or custom for each patient?
- Is this a [prototype](https://www.hubs.com/blog/rapid-prototyping/), proof-of-concept, or final product?
- What is the expected material to be used? The answers to these critical questions will aid in determining the best choice for your project – [additive manufacturing](https://www.hubs.com/knowledge-base/additive-manufacturing-technologies-overview/), CNC machining, or injection molding.
In general, traditional manufacturing processes such as CNC machining or injection molding are best suited for higher volume parts because of the higher start-up costs and longer lead times for tooling. Additive manufacturing is better suited for unique or low volume parts as well as prototypes or proof-of-concept designs.
The part geometry and required material properties should also be considered. Injection molding and additive manufacturing are typically more advantageous for complex part geometries and the material properties vary between all three categories. More information on common processes used to manufacture medical devices, covering CNC machining, injection molding, and additive manufacturing, is summarized below.
CNC machining
Specifics for each CNC machining category are beyond the scope of this article but factors that impact the type best suited for your application include part geometry and part material. CNC machines cover a wide range of cutting tools/machining processes and have applications suitable for all part geometries and materials found in medical device manufacturing. CNC machining for medical devices is best suited for higher volume and final products due to the high start-up cost. Read more about CNC machining →
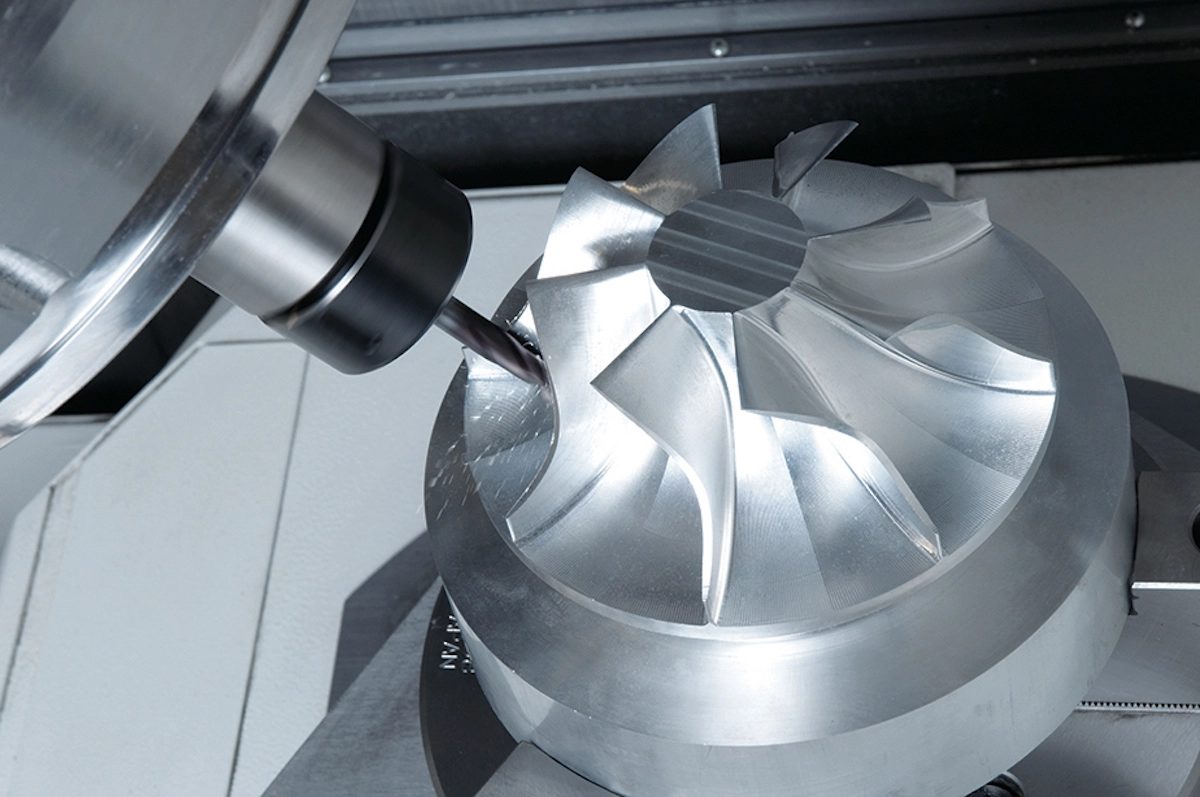
Injection molding
Injection molding is best suited for higher volume medical devices – laboratory equipment casings/housings, plastic surgical components, syringes, containers, test tubes, beakers. There are a broad range of materials available for injection molding including higher strength/durability plastics, higher flexibility including silicone plastics, sterilizable for dental and surgical tools and guides, and medical-grade for biomedical implants. Read more about injection molding →
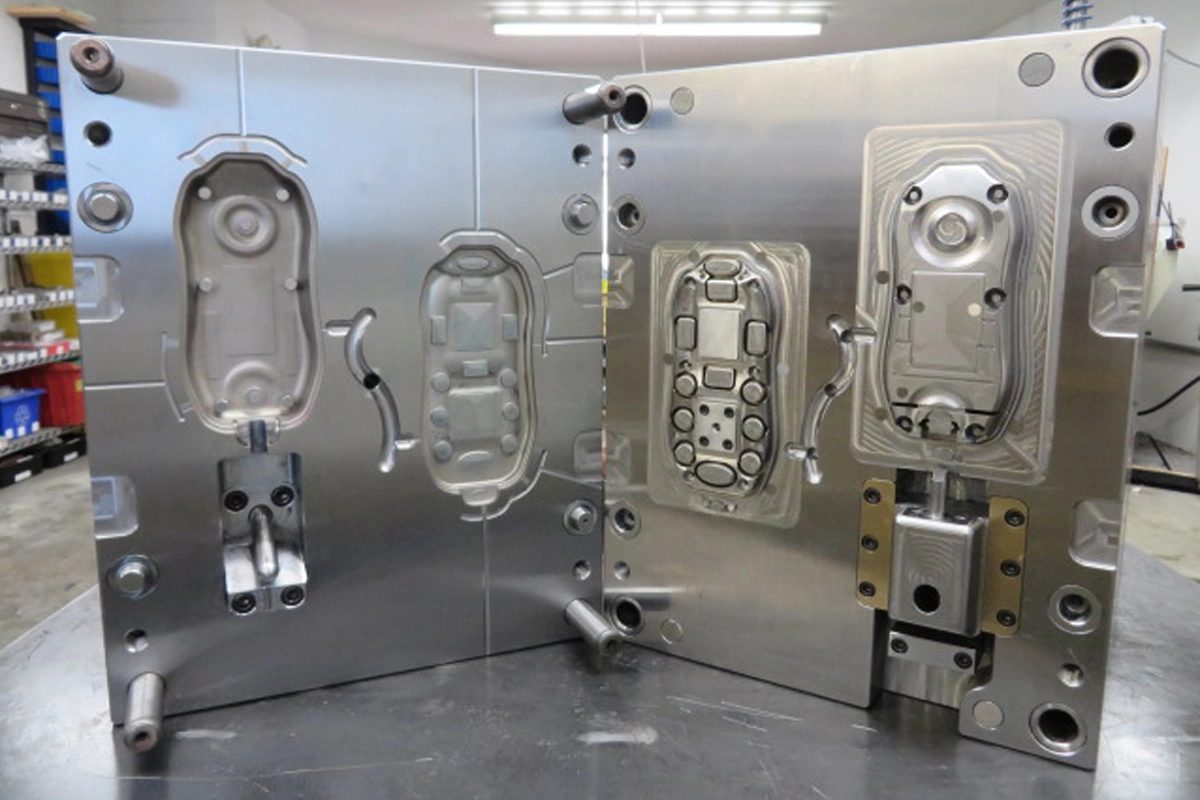
Fused Deposition Modeling (FDM)
Low cost solution for simple geometries. Consider for iterative, low-cost medical device prototyping or plastic medical devices where material strength is not a critical design attribute. Multiple plastic materials are available including materials compatible for biomedical implants and some are sterilizable for surgical devices. Read more about FDM →
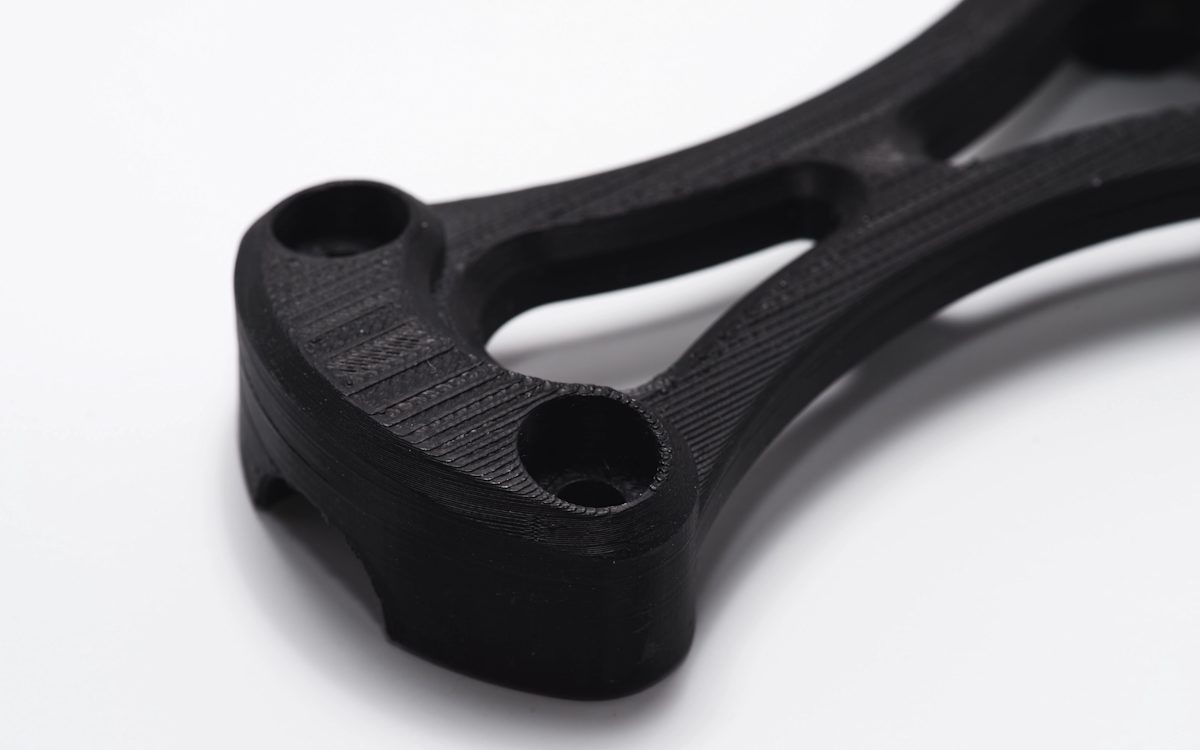
Stereolithography (SLA)
Best suited where high levels of detail and aesthetics are required. Parts have a smooth surface and can be painted. Applications for medical devices include lower cost prototypes, surgical and dental tools and guides, and some biomedical implants where high material strength is not required such as hearing aids. Read more about SLA →

Selective Laser Sintering (SLS)
Parts have good strength and a high level of accuracy. Consider for surgical and dental tools and guides with strength requirements similar to injection molded nylon. PA12 nylon is also sterilizable for biomedical implants. Read more about SLS →

Metal printing
Best for complex designs and where material strength is a critical design attribute. Metal printing has the most applications for medical devices of all additive manufacturing processes due to the ability to print complex geometrical shapes, higher material properties, and materials compatible with biomedical implants or sterilizable for surgical tools. Generally a higher cost option. Read more on metal 3D printing →
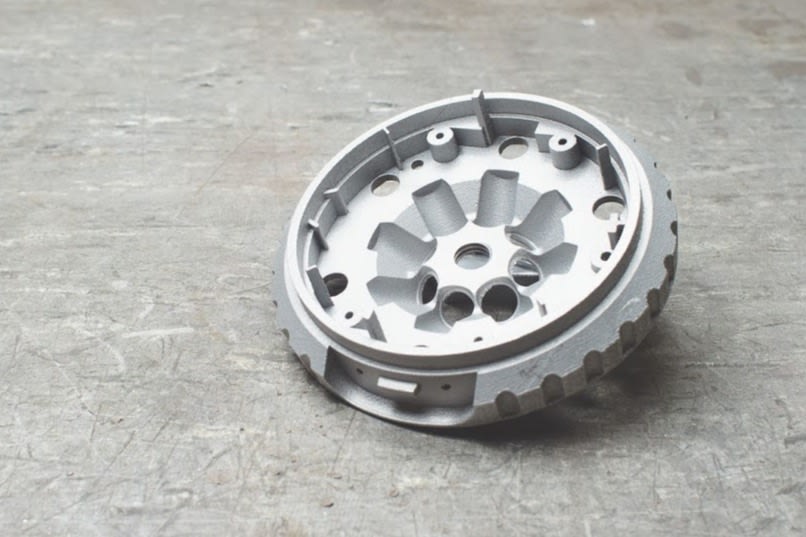
Applications for medical device manufacturing
There’s a wide range of applications for medical device manufacturing given the broad category of products classified as medical devices – from tongue depressors and latex gloves to x-ray machines and further to custom hearing aids and biomedical implanted devices such as heart valves. The field of medical device manufacturing is rapidly growing and the application of medical device manufacturing includes well-established products as well as cutting-edge technologies. Medical device manufacturing includes device prototyping for modeling and validation, complex geometry medical devices, modeling for simulation/training for medical professionals, and personnel protective equipment.

Common applications are:
The US Food and Drug Administration (FDA) requires premarket approval for medical devices, particularly for new or unproven products or where there is a significant risk to health and safety that requires clinical trials. Additive manufacturing through the use of rapid prototyping techniques can be an effective tool to quickly develop 3D parts, models, or assemblies for research and development and/or product testing for both the general medical manufacturing field and the biomedical engineering/medical research field.
Additive manufacturing has the benefit of producing highly customizable parts and complex 3D geometries – particularly suited to shape medical devices to the human body – without significantly increasing cost compared to traditional manufacturing processes. There is a wide range of possibilities available to manufacturers given the combination of 3D scanning, CAD design, and various additive manufacturing processes and materials. Examples of custom/complex geometry medical devices include:
- Custom prosthetics
- Custom surgical guides
- Biomedical implants (orthopedic, spinal, dental, organ)
- Innovative surgical instruments
Both CNC machining and additive manufacturing is well suited for low volume or custom production without the increased cost associated with traditional manufacturing processes. The same manufacturing processes used for prototyping/marketing, prosthetics, biomedical implants, and surgical instruments can also be applied to produce custom, low-cost, and anatomically realistic simulation and training models for medical professionals.
The recent events of the novel coronavirus pandemic have resulted in unprecedented demand for personal protective equipment (PPE) for medical professionals. Additive manufacturing has provided a low-cost alternative decrease production time and meet the emerging demands for PPE such as face masks and face shields, while injection molding has helped to scale production.
Best practices for designing and manufacturing medical devices
Following best practices for all types of manufactured products is always an important part of the manufacturing process and even more so for medical devices which are directly related to the health and safety of patients. As such, the regulations for medical devices are typically more stringent than for general manufacturing. In addition, best practices generally improve a company’s performance by increasing quality and decreasing waste, rework, and accidents. The following examples are best practices for manufacturing medical devices.
→ Know and understand the applicable regulatory standards and guidelines
Research the US Food and Drug Administration (FDA) regulations to avoid violating applicable laws and unnecessary redesign or rework. The FDA regulations are detailed in Title 21 US Code of Federal Regulations (CFR) Part 800 and more information is available on the FDA website.If manufacturing outside the US or shipping to another country be aware of the laws in that jurisdiction as well.
→ Consider design controls for product development
Design controls are criteria required to be met before moving to the next design phase and final approval of a design. They’re critical for medical device manufacturing because of the multi-step process required for certification and the ensure that the medical device design is on-track to meet the stringent manufacturing regulations applicable to medical devices. Criteria should be developed – which are typically specific to the product – and may include internal/customer requirements and applicable statutory regulations. Design reviews can be used to evaluate the design against the design control criteria based on the design maturity – design team members and other stakeholders are typically involved in design reviews and this is a great opportunity to gather feedback from all team members. Design controls are an effective way to track major design milestones and ensure the design meets the applicable requirements throughout the design process.
→ Consider Electronic medical device reporting (eMDR)
The US Food and Drug Administration (FDA) requires incidents involving a medical device including certain malfunctions and incidents that resulted in serious injury or death to be reported. An eMDR process can be used to automate and streamline the reporting process and allows for efficient and effective tracking to identify trends and implement effective corrective actions. Implementing an eMDR process results in standardized reports and can be used to ensure regulatory compliance for FDA reporting regulations.
→ Follow quality system practices
Consider what processes are necessary for your operation from design to delivery, particularly processes required by applicable medical device regulations such as Quality System guidelines, labeling, and reporting. Make sure the processes are written down for all employees.
Include inspection processes before a product is ready for shipping and the process for correcting any deficiencies (including reporting processes to learn from deficiencies and identify and correct trends). Make sure to include inspecting parts/materials from other suppliers and inspecting final products before shipping. If a robust Quality System does not exist, the best place to start is to develop checklists and flowcharts that outline your process from design to delivery.
→ Follow rigorous change management procedures
Change management procedures are important during the design phase but also throughout the life of a product to account for changes based on customer demands or corrective actions to the design or manufacturing process. Consider using a standardized procedure that tracks change requests, stakeholder approval or requests, and implementation of approved change requests. It may also be helpful to include potential impacts to other products or processes as part of your standard change management process to ensure consistency and improve quality across your company.
Regulations for manufacturing medical devices
In the United States, the US Food and Drug Administration (FDA) regulates medical device manufacturing and distribution. The FDA regulates medical devices based on three categories – Class I, Class II, and Class III – with Class I devices considered lower risk and Class III devices considered the highest risk. The FDA regulations are detailed in Title 21 US Code of Federal Regulations (CFR) Part 800. There are eight main areas covered by the FDA regulations:
- Registration
- Medical Device Listing
- Premarket Notification
- Premarket Approval
- Investigational Device Exemption
- Quality System Regulation
- Labeling
- Medical Device Reporting
All manufacturers and initial distributors of medical devices in the US must register with the FDA. Registration information must be verified annually and fees apply for initial registration.
All devices produced by a manufacturer must be listed with the FDA.
Most medical devices require prenotification to the FDA and an FDA acceptance letter before being commercially distributed. Some devices categoried by the FDA as Class I (lower risk) or Class II (medium risk) may be exempt from the premarket notification requirements; more information is available on the FDA website.
Medical devices categorized by the FDA as Class III (higher risk) require premarket approval and supporting documentation such as clinical trial data. If a Class I (lower risk) or Class II (medium risk) requires premarket notification then premarket approval is also required. Premarket approval is required before starting any marketing activities for these medical devices.
Outside of the United States, the European Commission have their regulations for medical devices which can be found here.
Present day medical device manufacturing and potential future trends
The medical device manufacturing industry is a rapidly developing field not just because of advances being made in manufacturing processes but also because of continuous development in the medical field, specifically biomedical engineering. Recent developments using additive manufacturing for medical devices have included synthetic blood vessels, orthopedic implants, organs, and even pharmaceutical medication. The possibilities seem only limited by the imagination of engineers and medical professionals. Image: The Delta-TT Cup, a 3D printed titanium implant with a lattice structure that accelerates patient rehabilitation and bone growth.

Looking to source custom parts for a medical device?
Receive instant quote