Polyethylene and polypropylene are two of the most widely produced plastics. Because of their similarities, choosing between them may be a challenge. These tips will prepare you to select the best option for your project.
What is polyethylene?
Polyethylene (PE) is a thermoplastic polymer made from the polymerization of ethylene. PE is the most commonly used plastic in the world, and as such is found in products like plastic bags, bottles, piping, and consumer goods. It is available in several forms, the most common of which are high-density polyethylene (HDPE) and low-density polyethylene (LDPE).
Here are a few of the characteristics of PE:
-
High impact strength. PE, especially HDPE, offers superior impact resistance, making it an excellent choice for applications such as heavy-duty containers, piping, and construction materials.
-
Flexibility and elasticity. LDPE is extremely flexible, making it ideal for applications like plastic films, plastic bags, and flexible tubing.
-
Chemical resistance. PE offers strong resistance to chemicals, especially in HDPE form. This makes it suitable for containers, pipes, and packaging that come into contact with chemicals and fuels.
-
Water resistance. PE is waterproof and does not absorb moisture, which makes it perfect for applications like water tanks, pipelines, and outdoor products like tarps and covers.
-
Easy processing. PE is easy to process using various manufacturing techniques like molding. This helps reduce costs and makes PE widely accessible.
-
Electrical insulation.PE is an excellent electrical insulator, making a great choice for cable coatings, wire insulations, and other electrical components.
What is polypropylene (PP)?
Polypropylene (PP) is a thermoplastic made from the polymerization of propylene monomers. It is widely used due to its toughness, flexibility, chemical resistance, and wear resistance. PP is often used in packaging, textiles, automotive parts, reusable containers, and more. Let’s take a closer look at its beneficial properties.
-
High chemical resistance. Like PE, PP is highly resistant to chemicals such as acids, bases, and organic solvents.
-
Heat resistance. With a high melting point (130–171 °C), PP can withstand higher temperatures, making it suitable for applications like hot-fill packaging and automotive components.
-
Toughness and durability. Despite being lightweight, PP has good toughness and impact resistance, making it suitable for products that require durability, such as plastic furniture and packaging materials.
-
Flexibility and elasticity. PP has moderate flexibility and offers good fatigue resistance, meaning it can bend without breaking. This property is crucial for items like plastic hinges, caps, and reusable containers.
-
Moisture and water resistance. PP is hydrophobic and highly resistant to water absorption, making it suitable for pipes or other parts or components used in moist or damp environments.
-
Cost-effective. Though slightly more expensive than polyethylene, PP is still an affordable and widely available material, making it cost-effective for manufacturers.
What are key similarities between PP and PE?
PP and PE exhibit some similar characteristics, but the align in the following ways.
-
Lightweight. Both PP and PE are lightweight, making them cost-effective for transport and easy to work with in manufacturing.
-
Recyclability. Both materials are recyclable, although PE is recycled more frequently due to its widespread use in packaging (such as plastic bottles and bags).
-
Non-toxic and safe. Both PP and PE are considered food-safe materials, making them commonly used in food packaging, kitchen utensils, and medical supplies.
What are the key differences between PP and PE?
Now let’s put PP and PE side by side, so we can accurately compare how the two materials differ.
-
Chemical structure. PP has a more complex structure, which provides more rigidity compared to PE.
-
Density and weight. PP is slightly denser than polyethylene, but also more lightweight.
-
Melting point. PP has a higher melting point (around 130–171°C) compared to PE (85–130°C). This makes PP better suited for high-heat applications.
-
Flexibility and strength. PE (especially LDPE) is more flexible, while PP is stiffer and more durable under mechanical stress.
-
Chemical resistance. Both materials offer good chemical resistance, but PP has better resistance to organic solvents, degreasing agents, and electrolytic attacks.
-
Transparency. PE tends to be more transparent, especially in its LDPE, while PP is often opaque.
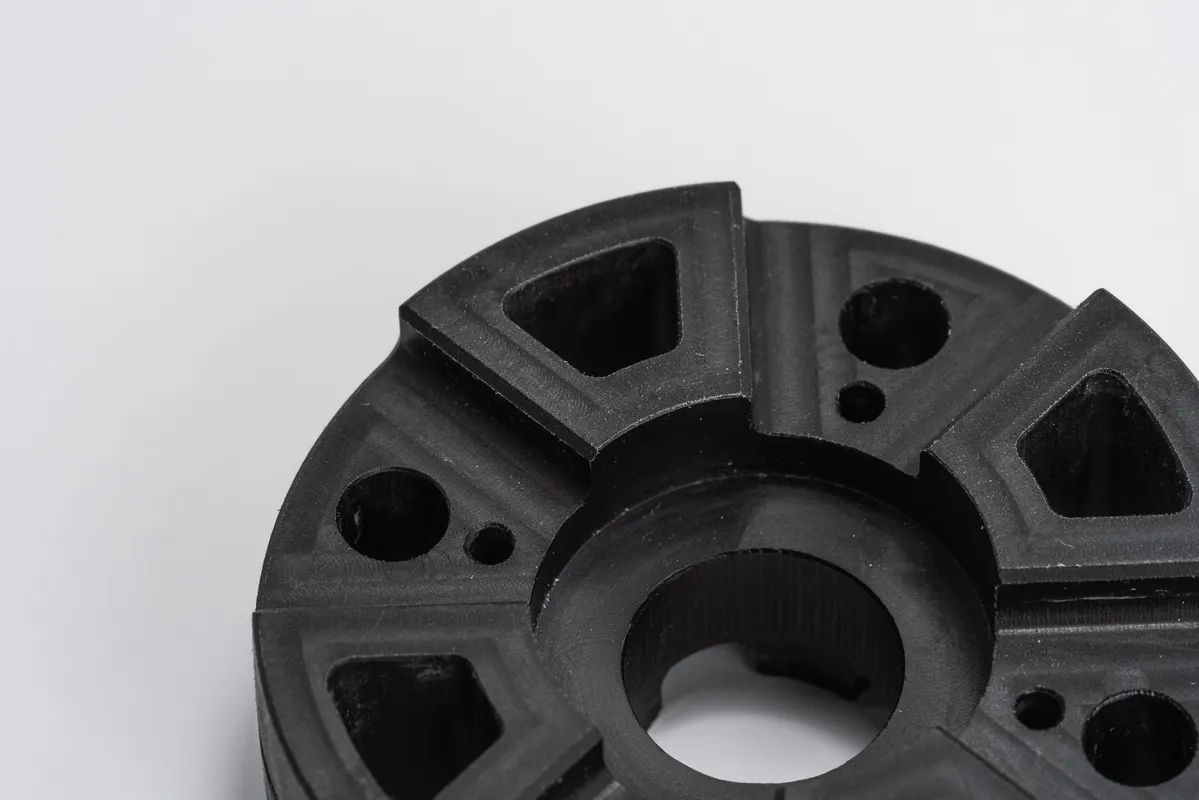
The cost of polypropylene vs. polyethylene
Generally, PE is more cost efficient than PP. This cost difference is due to variations in production methods, availability, and application requirements. PE is produced in larger quantities, making it less expensive overall.
Manufacturing methods for polyethylene vs. polypropylene
You can use many of the same manufacturing methods with PE and PP, although each material may be better suited to different ones. Here, we’ll examine three of our most popular methods of manufacturing to see how each material performs.
Injection molding with PE and PP
-
Polyethylene (PE). PE, especially HDPE, is well-suited for injection molding, and is often used to create flexible and moisture-resistant parts like bottles and packaging. However, challenges include warping, particularly with LDPE, and difficulties in achieving complex geometries due to its decreased flexibility compared to PP.
-
Polypropylene (PP). PP is highly suitable for injection molding due to excellent flow, a high melting point, and quick solidification. Its toughness makes it ideal for durable parts like automotive components and containers. However, shrinkage during cooling and mold wear are common challenges here.
3D printing with PE and PP
-
Polyethylene (PE). PE, particularly HDPE, can be 3D printed, but poses challenges like poor interlayer adhesion and warping. While it produces strong, lightweight parts, achieving high-quality prints requires precise temperature control and is less common than PP.
-
Polypropylene (PP). PP can be 3D printed using FDM, offering toughness and impact resistance that make it suitable for durable, flexible parts. However, it tends to warp due to low adhesion, requiring specialized printers or heated beds.
CNC machining with PE and PP
-
Polyethylene (PE). PE, especially HDPE, is easier to machine and is widely used in high-wear applications. Like PP, it requires careful temperature management to avoid melting and burr formation, but it offers excellent toughness and impact resistance.
-
Polypropylene (PP). PP can be CNC machined to provide toughness and durability for flexible parts like fittings. However, its softness can lead to deformation or chatter during cutting, requiring precise tool setup and cooling.
Industrial applications for polyethylene and polypropylene
Customers commonly use these materials to manufacture the following types of products.
Industrial applications of polyethylene
-
Packaging. Widely used in plastic films, bags, and containers for flexibility.
-
Piping. HDPE is often used in gas and water pipes for its strength and corrosion resistance.
-
Consumer goods. Found in toys, household items, and plastic bottles due to its versatility.
Industrial applications of polypropylene
-
Automotive. Used in bumpers, dashboards, and interior components for durability.
-
Textiles. Common in rugs, ropes, and reusable bags due to its strength.
-
Medical. PP is used to create syringes, medical vials, and food containers due to its safety.
Produce custom PE or PP parts
Order custom parts using PE or PP. Just upload a CAD file to receive instant pricing and lead times. To get your project started, you can also read more about choosing the right materials for your application and our guide to plastics.
Frequently asked questions
What are the main differences between PE and PP?
PE is more flexible and chemical-resistant, while PP is tougher and more heat-resistant.
Which is better for high-temperature applications?
PP is better for high-temperature applications due to its higher melting point.
Which material is more chemically resistant?
PE offers better chemical resistance, especially against acids and bases.
Which is easier to 3D print, PE or PP?
PP is easier to 3D print, though both pose challenges like warping.
Which is more suitable for outdoor use?
PE is more suitable for outdoor use due to better UV and weather resistance.
Is PP or PE better for food packaging?
Both are food-safe, but PE is more commonly used in flexible packaging.
Which has better impact resistance?
PP generally has better impact resistance than PE, especially at room temperature.
Which material is more cost-effective?
PE is typically more cost-effective, especially in large-scale applications.
Can both PE and PP be used in injection molding?
Yes, both PE and PP are widely used in injection molding for various applications.