Industries are switching from metal to plastic components because of weight reduction, performance attributes, cost savings, various resistances to corrosion and other types of wear and the fast production times attributed to them. The process able to deliver these benefits for plastic part production is injection molding.
The source of over 40% of all plastic parts globally and a $300B market as of mid-2022, injection molding is the manufacturing process of forming components in molds. In recent years, it's gained more traction in the medical industry especially due to the increasing demand for biodegradable materials that are more environmentally friendly and its ability to achieve high-quality, cost-effective parts.
The versatility of injection molding allows you to produce high volumes of parts at a lower piece-part price and at greater speeds compared to other processes like CNC machining and 3D printing. There are over 25,000 engineered materials compatible with injection molding that you can select from, and you can also scale your products into the thousands or even millions.
You should consider injection molding for projects:
-
That require large annual volume productions;
-
That involve complex designs and shapes (so long as the design takes into account IM design constraints like undercuts and part thickness);
-
Need part consolidation or metal-to-plastic conversion;
-
Where surface finish is a major factor;
-
Involve materials that would be too expensive with other manufacturing processes;
-
Involve expensive materials that pose budgetary concerns if machined;
-
Or in case the design is likely to stay the same or only change in smaller increments over several years (and production runs).
Let's dive into the common applications of injection molding and the key benefits of this higher-volume manufacturing process.
Ready to start injection molding parts?
Explore our injection molding services Request an injection molding quote
What kinds of parts can you make with injection molding?
Injection molding is common across a variety of industries. You’re likely to find injection-molded plastic parts in construction, food and beverage and consumer goods, among many other industries.
The most common applications found on the Protolabs Network platform are:
-
Aerospace
-
Automotive
-
Electronics
-
Medical
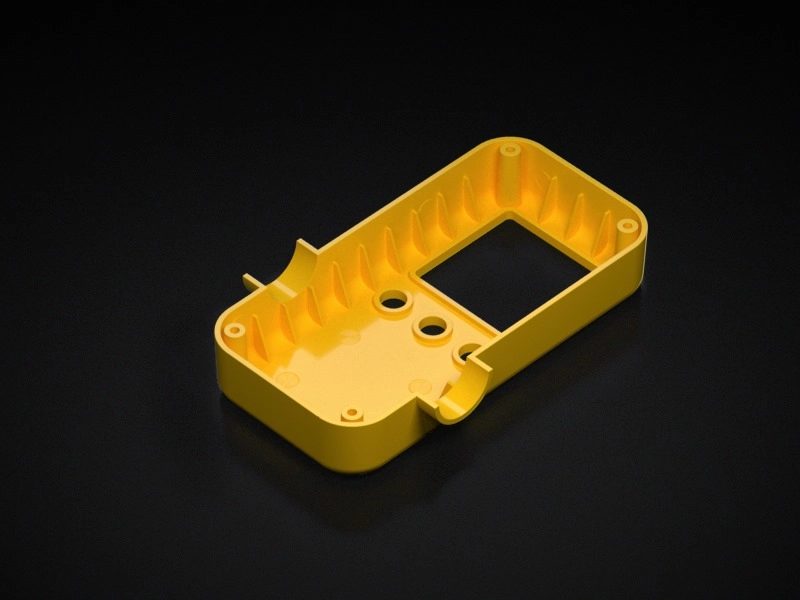
Injection molding aerospace parts
Aerospace components need to meet specific standards. They need to be lightweight, durable and able to withstand extreme temperature changes.
The most common injection molded parts for aerospace include:
-
Bezels
-
Chassis components
-
Enclosures
-
Housings
-
Panels
Injection molding automotive parts
Over the years, transportation technologies have become more advanced. On average, a car contains 30,000 parts internally and externally, from the engine block to tiny sensors that alert drivers to safety or maintenance issues. Almost every plastic component in the interior of your car is injected molded, as well as exterior parts like bumpers.
Other standard components that are injection molded for cars include:
-
Housings
-
Cupholders (and other storage compartments)
-
Dashboard components
The three most common injection materials used in the automotive industry include:
-
Polypropylene (PP) for non-critical parts
-
PVC for weather resistance
-
ABS for high-impact strength
Injection molding consumer electronics parts
Injected molded housings help protect the electronic components we all use today. Corrosion-resistant plastic enclosures protect metal components from harsh environments and temperature changes.
Other electronic components made from injection molding include:
-
Assemblies
-
Battery enclosures
-
Conduits
-
Components for laptops and desktop computers
-
Cases and enclosures for circuit boards
-
Electrical switches
Due to their excellent impact resistance and good electrical insulation, ABS and polystyrene (PS) are preferred for electronics.
Injection molding medical technology parts
Designing and manufacturing medical products and technologies comes with strict national and international guidelines to adhere to strict policies and prevent risks to patients. In the US, for instance, manufacturers producing medical components must use resins that carry an FDA seal of approval and ISO certification.
At Protolabs Network, we manufacture plastic enclosures for different medical instruments, transparent parts, and components for MRI machines.
Protolabs Network provides a variety of sterilizable and biocompatible materials for injection molded medical components. Medical grade silicone is the most popular; however, it is a thermoset, so special machinery and process control are required, which increases the cost.
Applications with less strict requirements can use materials like ABS, polypropylene (PP), and Polyethylene (PE).
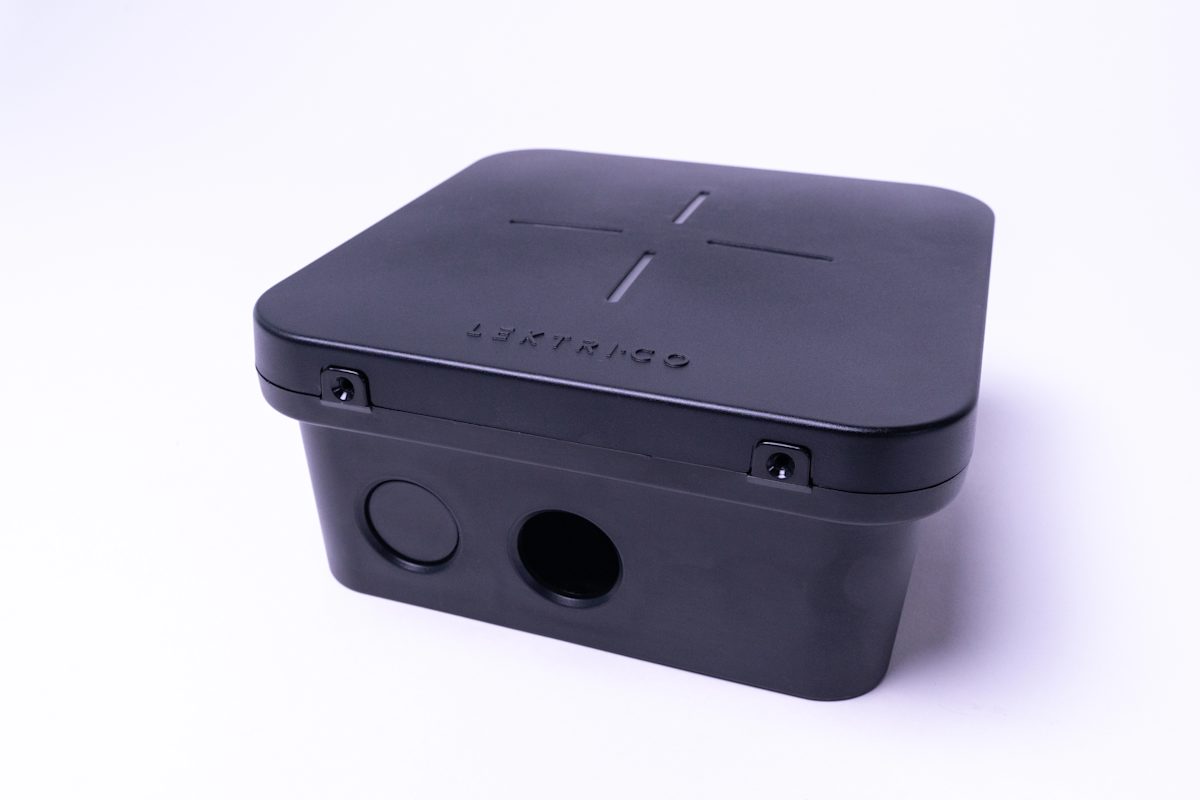
What are the benefits of injection molding?
Injection molding is overall more reliable and efficient than other manufacturing methods if you’re hoping to produce a lot of the same part. It can produce a wide variety of different geometries and part sizes.
Other benefits of injection molding include:
-
High-volume, cost-efficient, and fast production of plastics
-
Cost savings
-
Enhanced strength and durability
-
Tight tolerances and outstanding repeatability
-
Material flexibility
-
Excellent visual appearance
How does injection molding make a lot of parts quickly and cost-efficiently?
Injection molding is cost-competitive for manufacturing high volumes of identical plastic parts. Once the mold is created, and the machine is set up, parts can be produced quickly at low costs.
The recommended minimum production volume for injection molding is 500 units. At this point, economies of scale start to kick in, and the relatively high initial costs of tooling have a less prominent effect on the unit price.
Protolabs Network can make around 100,000 parts from ABS using just one mold at an average price of $0.68, though this varies based on the size of the part.
The typical injection molding cycle lasts around 15 to 60 seconds, depending on the part's size and the mold's complexity. In comparison, CNC machining and 3D printing might require minutes to hours to produce the same geometry.
With injection molding, you get your parts to market faster and gain a competitive advantage with the ability to produce multiple objects simultaneously that are identical to one another within an hour.
How does injection molding reduce costs?
Injection molding provides several cost benefits over other types of manufacturing processes. Today, the injection molding process is automated by machines and robots operated by a single technician, and this helps reduce labor costs and reworks caused by defects or human error.
Focusing on DFM (design for manufacturability) also provides cost benefits by decreasing the number of issues with moldability. DFM creates a collaborative process between OEMs, engineering teams, and customers that reduces the number of tool changes, machine downtime, and other production delays.
There is very little waste associated with injection molding because the amount of material needed to fill the mold is determined during the design process. Any waste created or scraps of material left over can be recycled and reused for other projects.
Are injection molded parts strong and durable?
The strength of injection molded parts comes from their one-layer design and continuous form. Over the years, the demand for strength and durability has increased, and today's lightweight thermoplastics are just as strong as some metal parts available.
You want to determine your part's strength at the beginning of the design process because it will help balance other design considerations and confirm what materials to use.
How does injection molding achieve tight tolerances and great repeatability?
Injection molding is highly repeatable. Of course, some wear occurs to the mold over time, but a typical pilot-run aluminum mold lasts an average of 5,000 to 20,000 cycles before needing to be replaced. Full-scale production molds from tool steel last around 100,000+ cycles.
Injection molding typically produces parts with tolerances of ± 0.500 mm (0.020"). Tighter tolerances down to ± 0.125 mm (0.005") are also feasible in certain circumstances. This level of accuracy is enough for most applications and comparable to CNC machining and 3D printing.
What materials can you use for injection molding?
Over 25,000 engineered materials are compatible with injection molding, including thermoplastics, silicones, thermosets, and resins. This means there is a wide range of materials with diverse physical properties that you can select from and design your part. The possibilities are endless.
Parts produced with injection molding have excellent physical properties that can be tailored with additives, like glass fibers, or by mixing different pallets, like PC/ABS blends, to achieve a desired level of strength.
You want to ensure that you select the right materials for your design. Keep in mind the part's impact and tensile strengths, heat deflection, water absorption, and flexural modulus of elasticity.
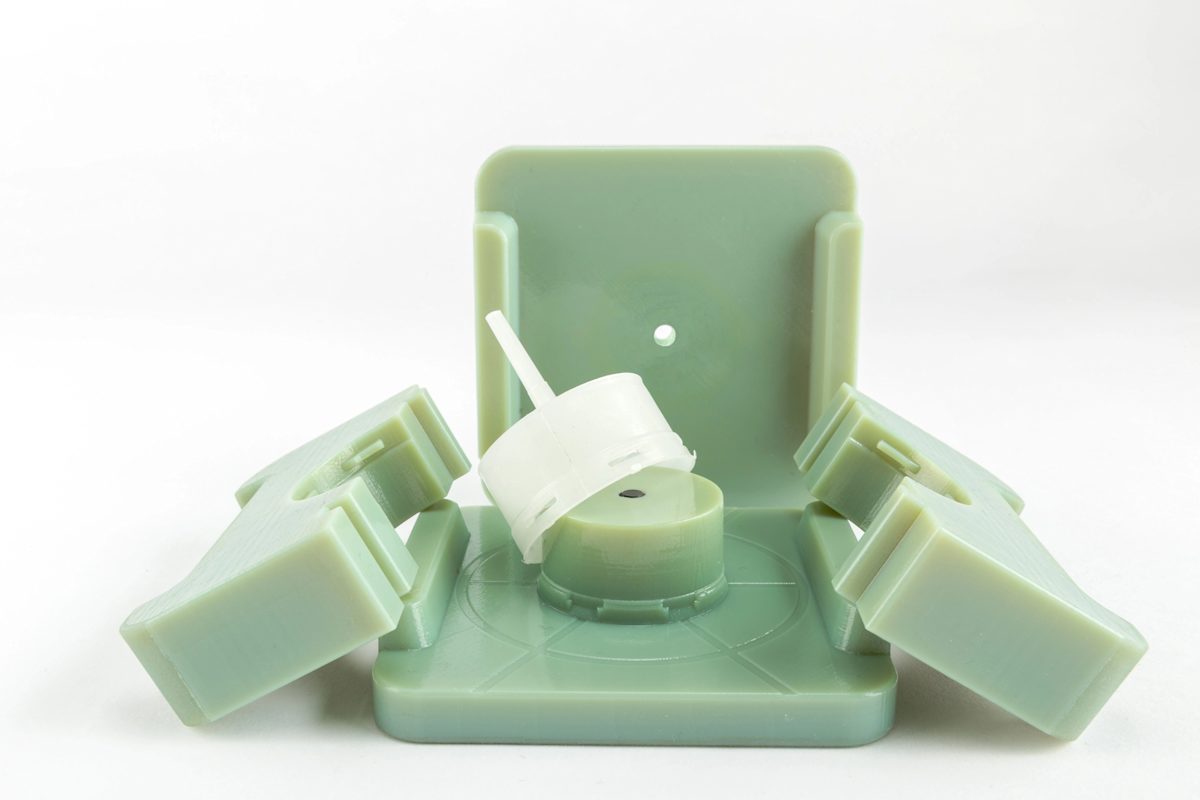
What's the cosmetic quality of injection molded parts?
Injection molding produces products that need little to no extra finishing. Most molded parts have a smooth finish, but you can design a product with matte finishes and unique textures and engravings.
Molded parts can be polished to a high degree that creates a mirror-like finish, and they can also be bead-blasted to develop more of a textured-type finish. Review the SPI standards that dictate the level of finishing that can be achieved for injection molded components.
Full disclosure - what are the drawbacks of injection molding?
While injection molding provides several advantages over other manufacturing processes, there are some drawbacks.
First, the main economic restriction is the high initial costs for tooling. Design engineers have to create a custom mold for each geometry, making the initial investment costs pretty expensive. To design and manufacture the mold costs between $5,000 and $100,000. For this reason, injection molding is economically viable for productions larger than 500 units.
Once the mold is created, any design changes can get costly, and modifications require a new mold to be created from scratch. This adds to lead times and overall costs.
Finally, the typical turnaround for injection molding is between six and ten weeks – four to six weeks to manufacture the mold and two to four weeks for production and shipping. Design changes add to the turnaround time. Here at Protolabs Network, it takes a maximum of 40 days to make the mold and for the client to get samples.
How do you compare injection molding and 3D printing?
Injection molding and 3D printing often get compared to one another; however, you should view them as complementary and not competing. 3D printing can help shorten pre-production iteration cycles of injection molding and allow for better testing, manufacturing and overall outcomes.
Curious about injenction molding parts with Hubs?
Explore our injection molding services Request an injection molding quote