Sheet metal fabrication involves bending or cutting flat pieces of sheet metal to form parts that are durable, long-lasting, and well-suited to industrial applications. However, because sheet metal is flat in principle, you will need to approach your part’s design differently than you might for other forms of manufacturing. Additionally, sheet metal fabrication can have relatively high labor costs. With this in mind, you’ll also need to take steps to streamline the overall manufacturing process in an effort to minimize costs. In this article, we’ll give you a few of our top tips for reducing costs on sheet metal parts. They encompass design, manufacturing, and post-processing, so you can be sure you are taking the most efficient approach possible to producing sheet metal parts. What factors affect the cost of sheet metal fabrication?
Before we dive into our tips for cost reduction, let’s take a general look at a few aspects of sheet metal fabrication that can raise costs. Then, in the sections following, we’ll touch on specific actions can take to reduce them.
-
Materials. The type and grade of sheet metal you use will affect the cost of your parts. Steel, for instance, is usually much more expensive than aluminum or carbon steel.
-
Sheet metal thickness. Thicker sheets usually require more material, and thus more processing time – if it is even feasible – which results in higher costs.
-
Design complexity. Typically, the more complex your design, the higher the cost. Be sure to consider the bend radius and using specialized sheet metal design software (more on both of these below)
-
Production volume. Perhaps obviously, economies of scale apply to sheet metal fabrication. Larger production runs often result in lower per-unit costs.
-
Post-processing. Painting, powder coating, plating, or anodizing your sheet metal parts can make them cost more.
Tips for reducing costs on sheet metal parts
Now it’s time to get into how you can save money (and time) when designing and manufacturing sheet metal parts. Below, we’ve curated nine cost-effective tips you can use when designing for and manufacturing with sheet metal fabrication service.
Use the right software
Design software that has specific tools for sheet metal parts – such as an “unfolding” view shows a 3D model of a sheet metal part will unfold into a flat pattern. It can also help you with bend calculations – which are the base for a good sheet metal design – and further understand the limits of the technology, so you can take steps to create a part that is both effective and cost-efficient.
Choose the right material for the job
We touched on materials in the previous section, but it is one of the primary factors that drive up the cost of sheet metal parts. Here, you’ll need to think about the part you are trying to make. A prototype, for instance, doesn’t always need to be created with an expensive material, especially if you are only attempting to validate a design.
Additionally, try to choose materials that are common or easily sourced. While expensive, stainless steel is often used in sheet metal fabrication, which means your manufacturer should have no problem finding it. The same goes for aluminum or regular steel.
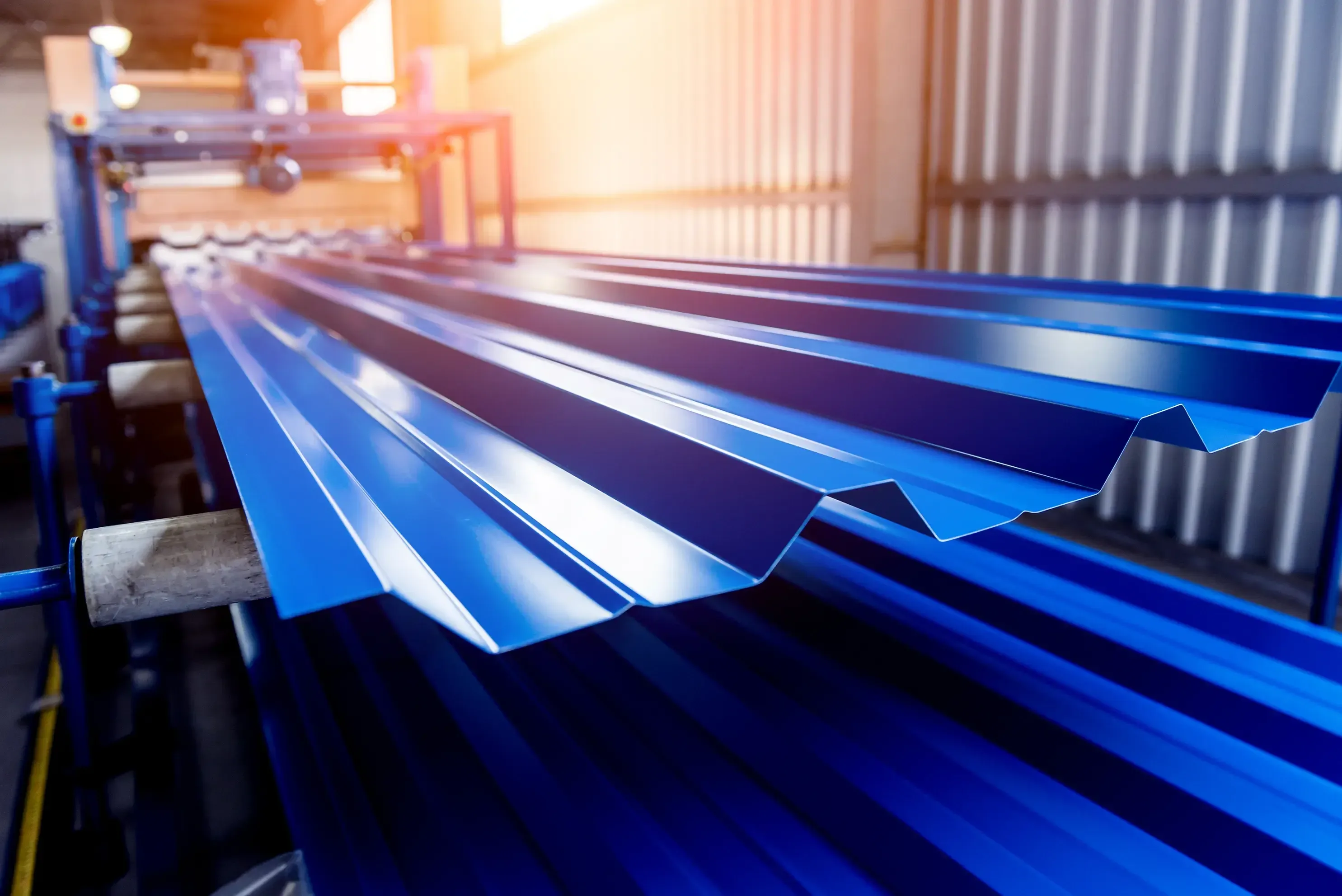
Avoid tight tolerances
When possible, avoiding tight tolerances in sheet metal fabrication significantly reduces costs. Tighter tolerance usually means slower production, which in turn results in increased labor hours due to the need for increased precision and other related adjustments.
Additionally, parts with tighter tolerances often lead to increased waste, as parts with minor errors or discrepancies often need to be scrapped or reworked. Increased waste means your material costs will also increase.
Avoid unnecessary features
Try to design your parts with designing with fewer intricate geometries, complex contours, or sharp corners. Doing so reduces the need for specialized tooling and machining processes, which can reduce both labor and material costs.
Combine parts
The more cuts in your sheet metal parts, the more expensive they will be. When designing your part, make every effort to combine parts, especially if they are made from the same material and won’t result in a more complicated assembly.
Consolidate cutouts
The same goes for cutouts: the more you have, the more expensive your part will be. Instead of making many small cutouts, in your part – for example, in a vented section – consider designing it with a single cutout, such as a single, long rectangle.
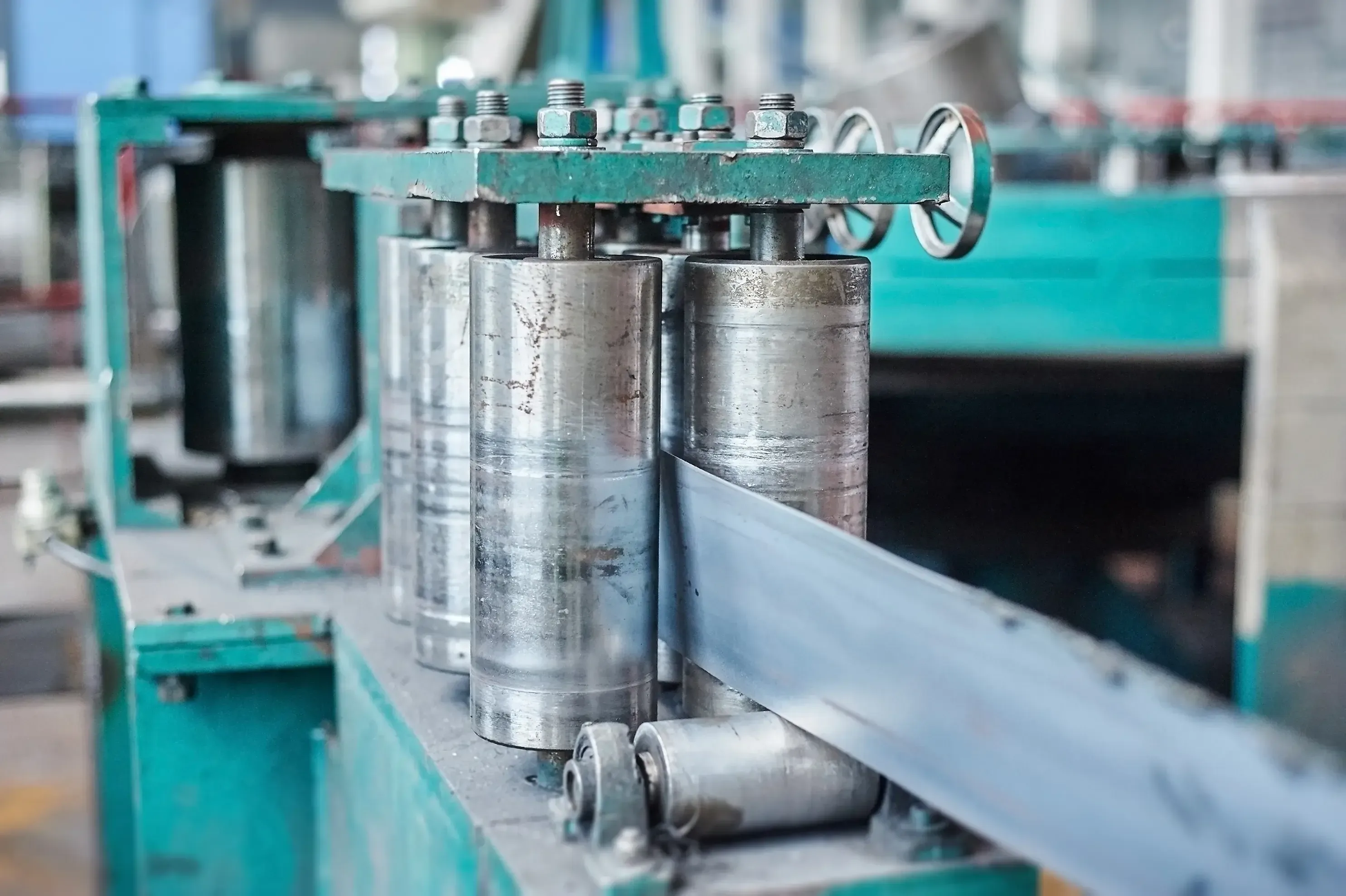
Try to avoid welding
When welding, pre-plated sheet metal releases zinc oxide, which is toxic. If your parts need to be welded, you must use uncoated cold rolled steel, then apply an anti-corrosion coating afterward.
Unsurprisingly, this is an expensive endeavor. It also increases lead times. If you absolutely must join sheets, look at alternative methods of doing so, such as riveting.
Use consistent bend orientation
As long as they are on the same plane, orienting bends in the same direction reduces setup time for any bending equipment your manufacturer will need to use. It also means your manufacturer won’t have to reorient your part each time they make a bend. This leads to faster and more cost-efficient production
Use an appropriate bend radius
A sheet’s bend radius is the distance from the center of the bend to the outer surface of the metal. For the most efficient production, you should ensure that your part’s bend radii are between 0.030 in. (0.762mm) and the thickness of the material that is being bent.
Standardize feature sizes
When possible, strive for standardized feature sizes in your parts. This includes punch form features like bridge lances, embossments, and ribs, as well as thread, hole, and corner sizes. This will limit retooling, minimize setup times, and result in more cost-efficient production.
Order sheet metal parts
Start production on custom sheet metal parts by uploading a CAD file to our Quote Builder. You can instantly compare lead times that suit your project’s schedule.
To sharpen up your sheet metal expertise, read more about the basics of sheet metal fabrication and types of sheet metal fabrication.
Frequently asked questions
What techniques can minimize material waste during sheet metal fabrication?
Techniques such as nesting optimization, standardizing dimensions, and DFM help minimize material waste – and as such reduce costs.
How does standardizing sheet metal dimensions help to reduce costs?
It allows you to purchase materials in bulk, reduce setup time, and simplify fabrication processes.
Which alloys are cost-effective for sheet metal parts?
Aluminum and galvanized steel are cost-effective alloys for sheet metal parts. They also offer good strength-to-weight ratios and corrosion resistance.
How do automated cutting techniques help reduce costs?
Automated cutting techniques tend to increase precision, which leads to fewer errors, reduce material waste, and minimize labor costs.