Introduction
Industrial machinery serves as the backbone of various industries, supporting operational efficiency, productivity, and quality control. To do so, however, such machines must be reliable, efficient, and durable – all of which starts with assembling them from high-quality parts.
Creating these parts requires a deep understanding of the materials and processes used to manufacture them, best practices for their design, methods for reducing cost and lead time, and more.

What is industrial machinery?
Industrial machinery refers to a broad category of equipment and devices used in various industries for manufacturing, processing, and production. It encompasses a wide range of machines designed to perform specific tasks and operations, including the following.
-
Manufacturing equipment. Machines used in production processes, such as CNC machines, lathes, milling machines, presses, and industrial robots.
-
Material handling equipment. Machines used to move, store, and transport materials within a facility, such as conveyors, lift tables, and forklifts.
-
Packaging machinery. Machines used to package products efficiently, including filling machines, labeling machines, sealing machines, and wrapping machines.
Types of parts commonly manufactured for industrial machinery
The specific parts you will need to manufacture will of course vary depending on the type of machinery and its intended application. Our customers, however, often use Protolabs Network to create the following for use in industrial machinery.
-
Moving parts. Components designed to facilitate motion within machinery, such as shafts and bearings, enabling efficient power transmission and mechanical functionality.
-
Casings. Protective enclosures or housings that shield machinery components from external factors, providing structural integrity, safety, and often incorporating access points for maintenance.
-
Conveyor belts. Continuous loop systems used for transporting materials or products within industrial settings, facilitating efficient movement, sorting, and processing along production lines.
-
Industrial jigs and fixtures. Custom tools used to hold, support, or guide workpieces during manufacturing processes, ensuring accurate and repeatable positioning for precise assembly or machining operations.
-
Automation parts. Components used in automated systems, including actuators, controllers, and robotics, enabling increased efficiency, productivity, and accuracy in industrial processes.
-
Replacement parts. Components specifically manufactured to replace worn-out or damaged parts in existing machinery, extending the lifespan and maintaining optimal performance of industrial equipment.

What materials are used to manufacture parts for industrial machinery?
Metals, plastics, and composites are all used in the manufacture of industrial machinery. Exact material selection will depend on factors such as load-bearing capacity, thermal properties, chemical compatibility, electrical conductivity, and other application requirements. Manufacturers often use a combination of materials to optimize performance and performance.
What metals are used to create parts for industrial machinery?
Metals are used in industrial machinery for their strength, durability, and excellent mechanical properties. Commonly used metals include:
-
Steel. For parts that require high strength, toughness, and corrosion resistance, such as shafts, axles, and structural frames.
-
Aluminum and alloys. For parts that require a balance between strength and lightweight properties, such as machine casings and components for conveyor systems.
What plastics and polymers are used to manufacture parts for industrial machinery?
Plastics and polymers are lightweight, electrically insulated, and allow for increased design flexibility. Here are a few plastics that are commonly used to manufacture parts for industrial machinery.
-
Polyethylene (PE) and Polypropylene (PP). For components requiring chemical resistance and good strength, such as conveyor belts, rollers, housings, and casings.
-
Polycarbonate (PC) and acrylic (PMMA). For components or parts that require transparency, such as windows, protective covers, and displays in machinery.
-
Nylon (Polyamide). Because it is known for its high tensile strength and wear resistance, Nylon is often used for the creation of gears, bushings, bearings, and other applications requiring low friction coefficients.
-
Elastomers. Such as rubber and silicone are used in machinery for sealing, damping, and vibration isolation applications due to their flexibility, resilience, and sealing properties.
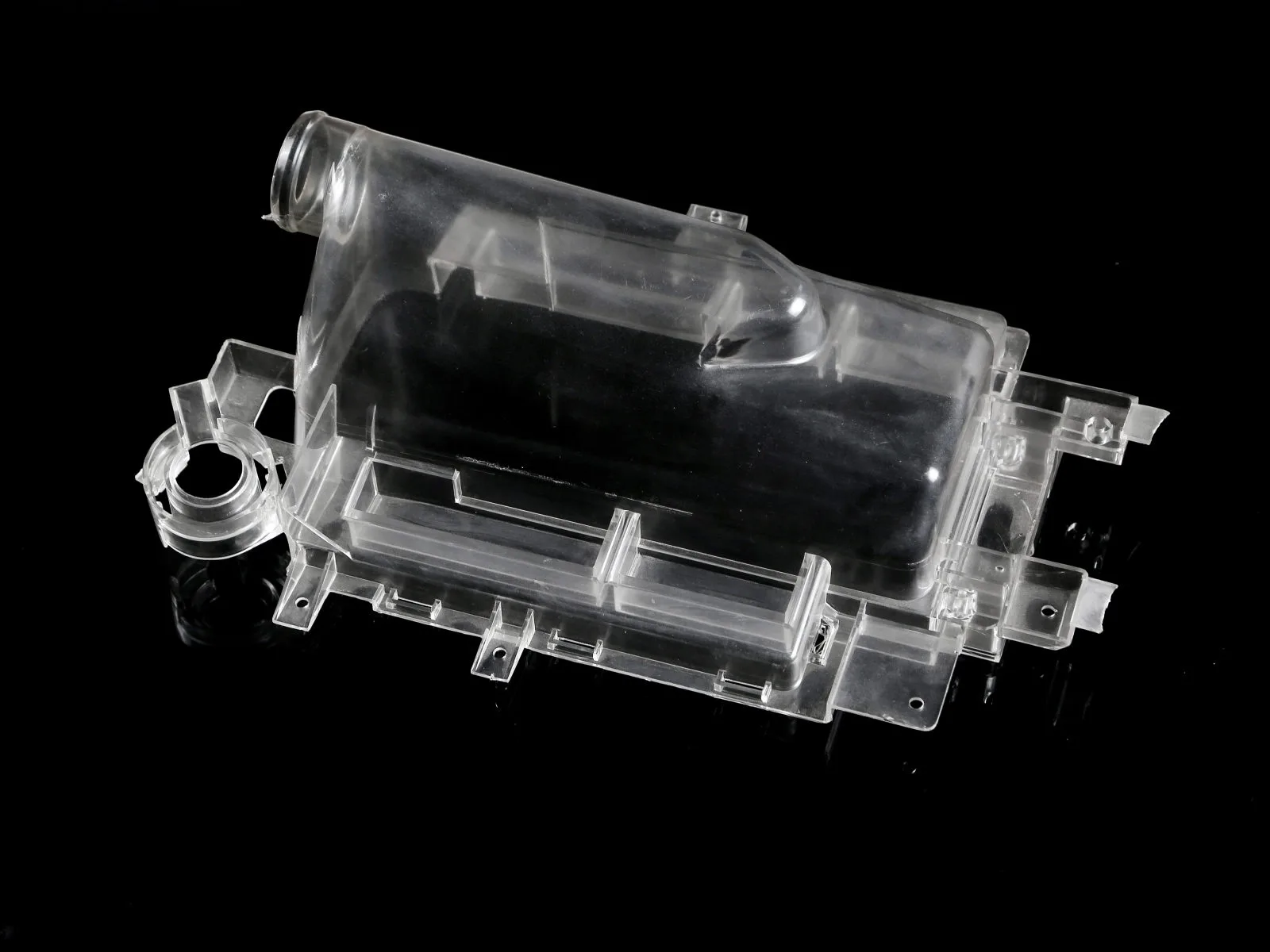
What composites are used to manufacture parts for industrial machinery?
Composite materials combine different materials to achieve specific properties. Here are a few composites used to manufacture parts for industrial machinery.
-
Fiberglass. Offering high strength-to-weight ratio, corrosion resistance, and electrical insulation properties, fiberglass is suitable for equipment enclosures and structural components.
-
Carbon fiber. With exceptional strength, stiffness, and lightweight properties, carbon fiber is often used in high-performance machinery parts.
What manufacturing methods are used to create parts for industrial machinery?
Several manufacturing methods are used to create parts for industrial machinery. The selection of a specific method depends on factors such as the type of part, material properties, desired precision, production volume, and cost considerations. Here are some common manufacturing methods for creating parts in industrial machinery.
-
Machining. Involves the use of tools and machines to remove material from a workpiece and shape it into the desired form. Techniques such as turning, milling, drilling, and grinding are used to create precise parts with tight tolerances. Computer Numerical Control (CNC) machining, meanwhile, is commonly employed for automated and high-precision machining.
-
Casting. A process in which molten metal is poured into a mold, then cooled to solidify. Casting methods, such as die casting, are suitable for creating complex parts, particularly those with intricate shapes or internal cavities.
-
Sheet metal fabrication. Used to form and shape thin metal sheets into various parts. Processes such as cutting, bending, and welding are used to create components like panels, brackets, and enclosures. Laser cutting is another common method sheet metal fabrication methods.
-
Additive manufacturing. Also known as 3D printing, additive manufacturing builds parts layer by layer using various materials, such as plastics or metals. It offers flexibility in design and can create complex geometries, prototypes, and low-volume production parts.
-
Injection molding. A process in which molten plastic is injected into a mold cavity and cooled to solidify into the desired shape. Injection molding is suitable for high-volume production of parts with consistent dimensions and complex designs.
What are design considerations for manufacturing parts for industrial machinery?
With the following design considerations, engineers can develop parts that are not only functional and reliable but also optimized for efficient and cost-effective manufacturing in industrial machinery. Collaboration with manufacturing experts and feedback from the production team can further enhance the design process and improve overall manufacturing efficiency.
-
Functionality. The part should fulfill its intended function within the machinery. The design should consider factors such as load-bearing capacity, alignment, proper fit with other components, and compatibility with the overall system requirements.
-
Material selection. Choosing the appropriate material is crucial to meet the mechanical, thermal, and chemical requirements of the part. Consider factors such as strength, durability, corrosion resistance, and temperature resistance when selecting materials.
-
Tolerances and fits. Clearly define tolerances for critical dimensions to ensure proper fit and assembly. Balancing the need for precision with the capabilities of the manufacturing process is essential to avoid overly tight tolerances that may be costly or impractical to achieve.
-
Safety. Consider safety aspects in the design to prevent hazards and ensure operator and user safety. This may include features like guards, ergonomic considerations, and proper labeling or instructions.
-
Sustainability. By designing parts with emphasis on environmental sustainability, you can achieve cost savings and meet regulatory requirements while producing greener. To do so, consider recyclability, energy efficiency, and the use of environmentally friendly materials or manufacturing processes.
-
Serviceability and maintenance. Design parts with serviceability in mind. To do so, consider access for maintenance, ease of replacement, and the availability of spare parts to minimize downtime and facilitate repair.
By focusing on cost reduction and lead time optimization, engineers can manufacture parts for industrial machinery more efficiently.
-
Strive for standardization. Whenever possible, utilize standardized components. This promotes interchangeability, simplifies sourcing, and allows for easier maintenance and repair.
-
Design for manufacturability (DFM). You should design parts for ease of manufacturing, considering the capabilities and limitations of the manufacturing processes that will be used. Additionally, strive to design parts with simplified geometries, avoiding complex features or difficult-to-machine shapes, which can increase production time and costs.
-
Find the right supplier. Establish strong relationships with reliable suppliers, which offer favorable terms for materials, tooling, and other services. You can also work together to streamline the supply chain, reducing lead times and ensuring timely delivery of components.
Find out more about how engineers use Protolabs Network to produce industrial-grade machinery parts. You can also upload a CAD file to receive instant pricing and DFM analysis.
Our knowledge base is filled with practical information about custom part manufacturing, including guides to producing end-use parts.
Frequently asked questions
What materials are commonly used for manufacturing industrial machinery parts?
Materials that are commonly used to create parts for industrial machinery include steel, aluminum, plastics, and composites.
How can I ensure the dimensional accuracy of machined parts?
Although CNC machining is a precise production method, our quality control procedures known as the Protolabs Network Standard ensures that your finished part is up to spec and adheres to the specified tolerances.
What factors should I consider when selecting a supplier for manufacturing parts?
You should consider factors such as reliability, quality, cost, lead time, and the supplier's track record.
Is it possible to reduce manufacturing costs without compromising quality?
Yes, by optimizing designs, streamlining processes, and improving efficiency.
Can additive manufacturing (3D printing) be used for industrial machinery parts?
Yes, additive manufacturing is commonly used for prototyping, low-volume production, and complex geometries.
How can I ensure the longevity and durability of machinery parts?
Choose materials with high strength and durability, apply appropriate surface treatments, and perform regular maintenance.
What is the typical lead time for manufacturing industrial machinery parts?
Lead time varies based on part complexity, quantity, and supplier capabilities, typically ranging from weeks to months.