What is TIG welding?
TIG welding, or Gas Tungsten Arc Welding (GTAW), uses a tungsten electrode that will not melt during the process. The heat from the electrode fuses the metal while a shielding gas, usually argon, keeps contaminants out of the weld.
What sets TIG apart is the manual control—it’s up to the welder to add filler material when needed. This hands-on approach delivers unmatched precision, making it the go-to process for delicate, detail-driven projects.
TIG welding vs. other welding methods
There are a few different processes that can work for sheet metal assemblies. Welding is one of the most widely used techniques for joining metals, and there are several ways to do it depending on the material and the job.
-
Stick welding uses an electrode coated in flux, which melts to form a protective gas. This method is perfect for outdoor and rough conditions where precision isn’t the top priority.
-
MIG welding is relatively quick and easy, feeding a wire electrode into the joint. The wire melts and acts as both the heat source and filler, while a shielding gas keeps the weld clean. It’s fast, efficient, and great for big jobs with thicker materials.
-
TIG welding takes a different approach, using a tungsten electrode that doesn’t melt. The welder adds filler material manually, if needed, while a shielding gas like argon protects the weld from impurities.
If MIG is the speedy multitasker and Stick is the rugged all-rounder, TIG is the perfectionist—built for detail, beauty, and strength.
Comparing the top 5 welding processes
Welding process | Ease of use | Speed (deposition rate) | Typical tolerances | Common applications | Suitable materials | MIG welding | Easy | Fast (up to 8 kg/hr) | Moderate (±0.8 mm) | Automotive, general fabrication | Carbon steel, stainless steel, aluminum |
---|---|---|---|---|---|
TIG welding | Challenging | Slow (1–3 kg/hr) | High (±0.25 mm) | Aerospace, medical devices, art installations | Stainless steel, aluminum, titanium |
Stick welding | Moderate | Moderate (up to 5 kg/hr) | Low (±1.5 mm) | Construction, pipeline work, maintenance and repair | Carbon steel, cast iron |
Flux-cored welding | Moderate | Fast (up to 10 kg/hr) | Moderate (±1.0 mm) | Shipbuilding, heavy equipment | Thick sections of steel |
Spot Welding | Easy | Very Fast (seconds per weld) | Low (±2.0 mm) | Automotive body panels, metal furniture | Thin sheet metals like steel and aluminum |
How does TIG welding work?
TIG welding is a delicate dance between heat, precision, and control. Here's the step-by-step process:
-
Ignition of the arc: The tungsten electrode generates an electric arc that heats the metal to a molten state.
-
Shielding gas: Argon or helium flows around the weld area, preventing oxygen and nitrogen from contaminating the molten metal.
-
Filler material: If needed, a filler rod can be manually added to the molten pool, allowing precise control over the weld’s composition and strength.
-
Cooling: The weld solidifies as it cools, forming a joint that is strong and visually clean
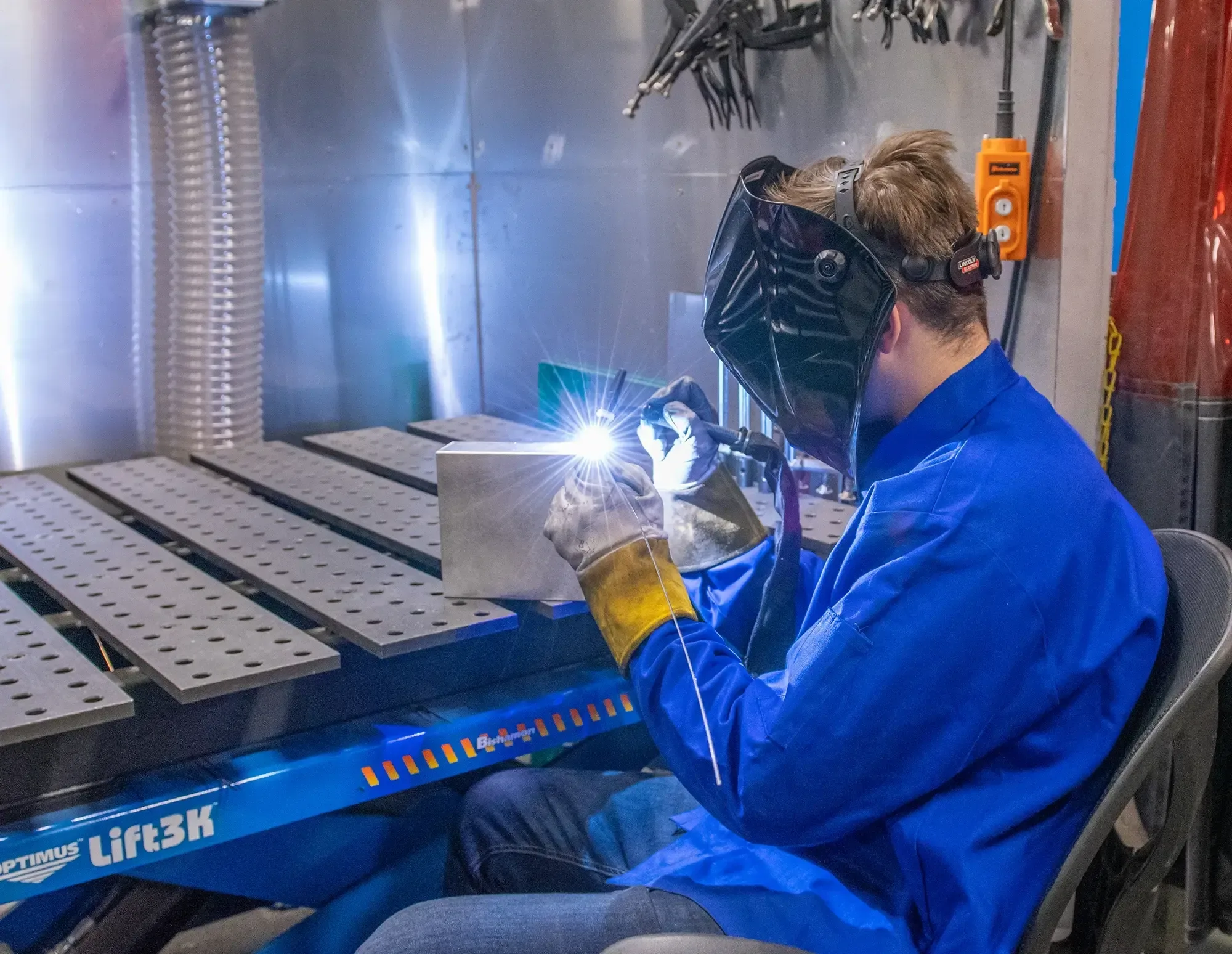
TIG welding by service
TIG welding plays a key role in manufacturing by bringing precision, strength, and clean finishes to the table. Here’s how it fits into different processes:
-
Sheet metal fabrication: Perfect for thin materials, TIG welding ensures minimal warping and clean joints. Sheet metal fabrication is often used to create intricately detailed parts, like these Christmas tree ornaments by Goodwin PLC, or for parts that undergo high wear-and-tear like these industrial exoskeletons made by Skelex.
-
CNC machining: When machined parts need assembly or repair, TIG welding provides the precision needed to keep parts up to spec.
-
Injection molding: While not part of the molding process itself, TIG welding is often used for repairing and maintaining molds, which keeps production running smoothly.
-
Metal 3D printing: TIG welding is sometimes used as a post-process for metal 3D printed parts, fixing imperfections or for joining parts with a seamless finish.
For custom manufacturing requests, including TIG welding, contact networksales@protolabs.com.
How TIG welding is used manufacturing
TIG welding is used in manufacturing when precision and quality are the priority. If you ride a performance bicycle or cook with high-end pots and pans, you’ve likely experienced the exceptional finish of a TIG weld. It is a particularly popular process for the following industries.
-
Aerospace: Fabricating lightweight, high-strength aluminum and titanium components.
-
Automotive: Crafting custom exhausts, chassis, and roll cages.
-
Medical: Joining stainless steel for surgical instruments and devices.
-
Art and design: Producing sleek, clean welds for sculptures, installations or home decorations.
Materials to use with TIG welding
TIG welding works with a wide range of metals so it can be leveraged for different industries and applications.
-
Aluminum: Perfect for lightweight designs, though its high thermal conductivity means you have to be careful with heat management.
-
Stainless steel: Combines strength and corrosion resistance, making it ideal for durable, high-performance parts.
-
Titanium: A top choice for aerospace and medical applications, thanks to its strength-to-weight ratio.
-
Copper and copper alloys: Often used in electrical components due to its conductivity.
Each material brings its own challenges and advantages, but TIG welding incorporates a manual element that allows the welder to adjust factors like heat, filler material, and technique in real time to suit the specific properties of each material. This adaptability is one of the reasons TIG welding is used for such a broad variety of metals. Keep in mind that although it’s possible to weld different metals together, such as steel to aluminum, this is not typically advised as it can significantly impact the functionality of parts.
TIG welding and strength
TIG welding results in incredibly strong joints, especially for thin materials. The process reduces the risk of defects such as porosity and cracking, so you get high durability even under stress. Industries that require parts with structural integrity—like aerospace and medical manufacturing—use TIG welding for its reliability. You can source custom TIG-welded parts through our off-platform services.
Pros and cons of TIG welding
TIG welding delivers exceptional accuracy but comes with its own set of challenges
Pros
-
Precision: Ideal for detailed work and thin materials.
-
Quality: Produces aesthetically superior welds with minimal cleanup.
-
Versatility: Works with a wide range of materials.
Cons
-
Slower process: TIG welding is more time-consuming compared to methods like MIG welding.
-
Skill-dependent: Requires a high level of expertise for the best results.
-
Cost: Precision comes at a price, including time, equipment, and money—you may end up paying nearly double what you would for MIG welding.
TIG welding tips and tricks
If your parts are heading to TIG welding, a little planning in the design stage can make a big difference. Here’s how to set yourself up for success:
-
Keep weld areas clean and accessible: Design smooth, easy-to-reach surfaces where welds will go. This helps keep contaminants out of the way and ensures a solid bond.
-
Match material thicknesses: Avoid pairing thick and thin materials at the weld joint—it makes it harder to control heat and can lead to distortion.
-
Plan your joint design: Features like beveled edges or chamfers make it easier to get a strong, deep weld, especially on thicker materials.
-
Keep welds away from potential stress concentrations, and other fragile areas. This is because welds are almost always weaker than the surrounding material, and therefore the area most likely to break under strain.
-
Think about heat control: Leave enough spacing and use materials like stainless steel or titanium that can handle the heat without warping, especially if you’re working with thin sheets.
-
Make it easy to weld: Design parts so welders can comfortably access the joints. For example, avoid angles tighter than 30 degrees or overlapping plates that leave less than five centimeters of clearance for a welding torch. Joints tucked into narrow cavities or hard-to-reach corners can slow the process and lead to inconsistent weld quality.
Get a quote for TIG welding
For TIG welding and other custom manufacturing requests,contact our sales team. Protolabs Network provides off-platform TIG welding services tailored to your project’s specifications. Let us help bring your designs to life with precision and strength.
Frequently asked questions
Why is TIG welding slower than other welding methods?
TIG welding prioritizes precision and quality, requiring more control and technique compared to faster methods like MIG welding.
What is the maximum thickness for TIG welding?
TIG welding is best suited for thin to medium-thickness materials, typically up to 5-6 mm, though thicker materials can be welded with proper preparation.
Can TIG welding be used for repairs?
Yes! TIG welding is ideal for repairing cracks and joining intricate parts.
What is TIG welding used for?
TIG welding is commonly used in industries requiring high-quality welds, such as aerospace, automotive, medical device manufacturing, and even artistic metalwork.
What does TIG stand for?
TIG stands for Tungsten Inert Gas, referring to the tungsten electrode used in the process and the inert gas (usually argon) that protects the weld area.
Can you TIG weld without gas?
No, shielding gas is essential to TIG welding for protecting the weld area from contamination.