SuperNode's journey began in 2018 with renewable energy pioneer Eddie O’Connor at the helm. Now, with the backing of the Norwegian Green Investment group Aker Horizons, they're driven by a goal to provide everyone with affordable, secure, and green energy using innovative superconductivity methods.
The grid's challenge: Decarbonisation and capacity limits
We're witnessing a global embrace of wind and solar energy, and countries are setting ambitious green energy and net zero goals. However, contemporary grids lack the power capacity to accommodate the additional inflow from renewables. With a maximum capacity of 1 GW, conventional cables not only experience electrical losses but also need extensive infrastructure, space, and materials, making the power transfer process expensive.
To transition smoothly and timely into a greener future, Bloomberg projects a minimum investment of $21.4 trillion by 2050. However, relying solely on conventional grid technologies isn't going to cut it. This is where SuperNode’s pioneering power transmission approach promises to bridge the gap.
SuperNode's solution: Superconducting cables
Superconductors, when cooled to extremely low temperatures, can transmit power with zero electrical losses. Historically, superconducting cable applications have been limited to lower distribution levels in space-constrained urban settings, such as the AmpaCity project in Essen, Germany and the Shingal Project in Seoul, South Korea.
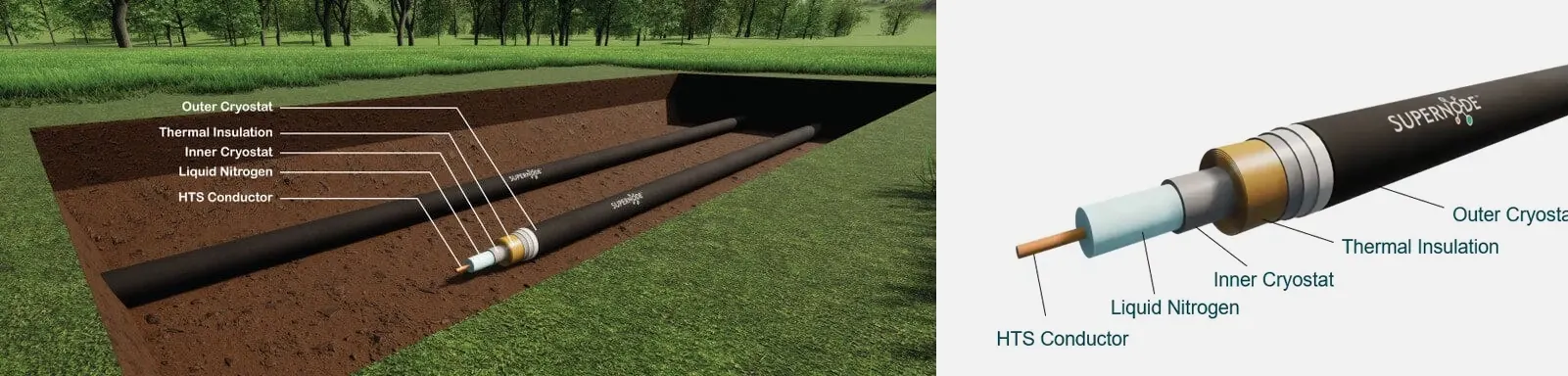
While the cooling process demands the cables be submerged in cryogenic fluids, these cables have very high power transmission capacity compared to the conventional ones. SuperNode's innovation is centered on creating even more efficient cable systems, ideal for higher-level, bulk power transfers. Their findings indicate that when you operate at 2GW or higher, the cooling expenses are less than what you would lose with a traditional 2GW cable. What's more, the energy needed to cool a 2GW, 6GW, or 10GW superconducting cable remains the same, making it more efficient to transfer greater power amounts.
Besides its onshore application, this technology holds a promise for offshore renewable platforms. A superconducting cable system in a collector station can lead to savings in space, materials, and finances. The following image does a great job of putting things in perspective:
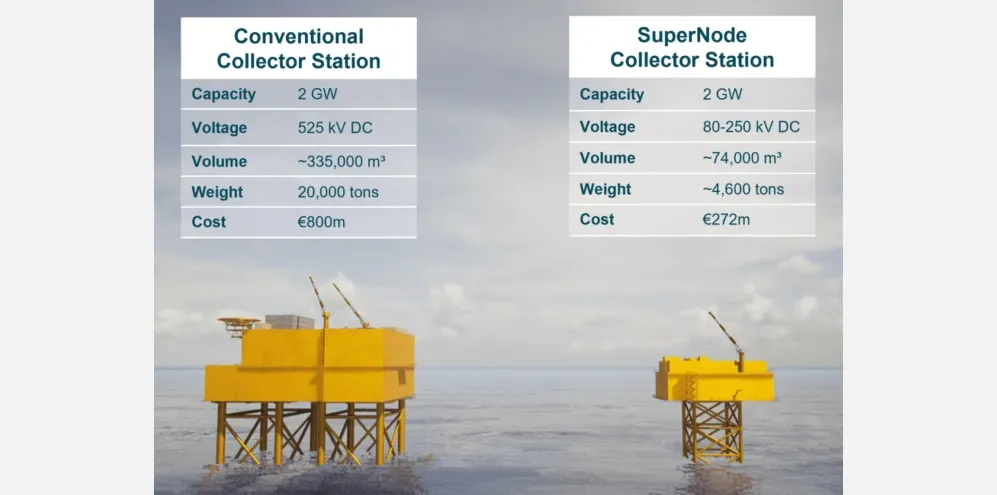
Accelerating development through on-demand manufacturing
As SuperNode shifted from research to prototype creation, they leaned on our services for our manufacturing expertise. Our versatile platform and wide material options allowed SuperNode to swiftly evaluate concepts and streamline the decision-making process. For a start-up like SuperNode, the rapid feedback and the ability to understand the design's financial implications proved invaluable. SuperNode could secure new components rapidly, mitigating risks and sticking to timelines. "Working with our account manager has enabled us to acquire new components rapidly to minimize the risk of delays to our testing timelines," notes Stephen Doyle, Senior Mechanical Engineer at SuperNode.
With our support, SuperNode has manufactured:
-
Vacuum Saddles: Aluminium saddles for pumping down the pipe-in-pipe vacuum annulus.
-
PEEK Sleeves: Serving as a dielectric barrier within their end cap and joints sub-systems.
-
Copper Testing Jigs: Used to verify the system's resistivity properties and mounting methods.
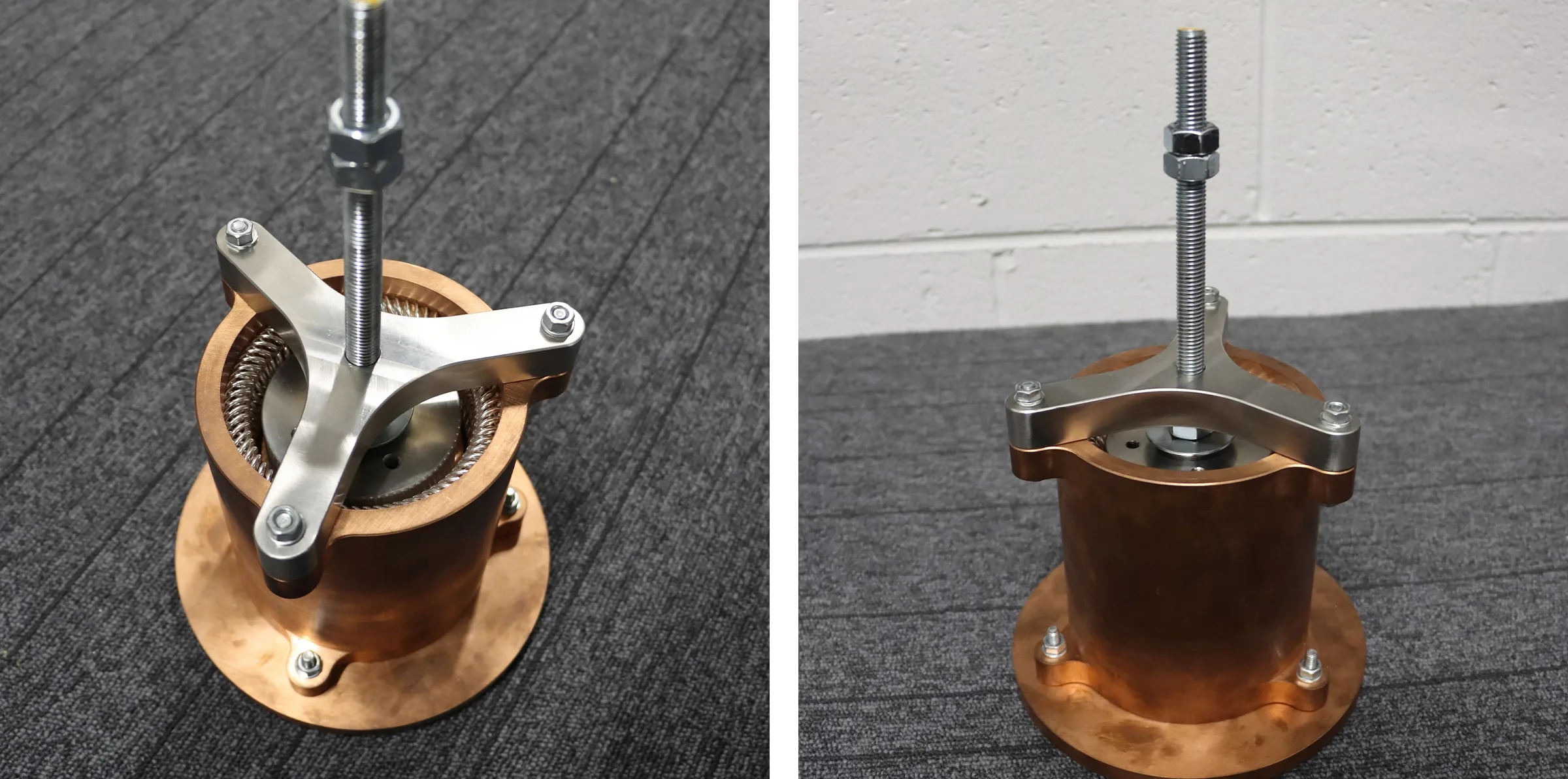
Refining design through collaboration
Collaboration with our manufacturing engineers allowed SuperNode to identify crucial design elements and areas where they could be more flexible. This has resulted in cost and lead time reductions for some components. “Their engineers have been keen to understand the purpose of different components and design features, which has enabled them to make suggestions about alternative materials or features to help us achieve better outcomes for our orders,” Doyle adds.
Custom components tailored for a sustainable future
SuperNode mentions that while many manufacturers excel in specific materials or processes, zeroing in on the right one for your design can be a challenge. The company navigates this by relying on our extensive partner network that streamlines this process by connecting with the most suitable manufacturer.
SuperNode's insulation advancements have already eclipsed NASA's record for soft vacuum insulation (1Pa – 10Pa). Their focus now is on further diminishing heat leakage into the inner cryostat, which will prolong the intervals between re-cooling. To achieve this, they're partnering with global leaders including CERN, the European Laboratory for Particle Physics.
With an eye on the future, SuperNode is setting ambitious goals. Their plan includes the establishment of a cutting-edge alpha facility by 2026 and the rollout of an efficient beta facility by 2030 to meet the expanding market demands.