Skelex is an innovative Dutch startup at the forefront of their field. They build mechanical passive exoskeletons that will not give you ‘superhuman’ strength but will make lifting industrial tools over and over again much easier.
Their passive exoskeleton makes your arms feel weightless using dynamic balancing. The springs in the back of the frame transfers the weight in your arms to to your hips and gives you the necessary amount of support while working in difficult postures, like overhead. This is proven to help industrial workers feel 80% less fatigue, increase their arm strength by 40% and experience fewer neck and shoulder injuries.
They also managed to solve the biggest challenge many hardware startups face with the help of our platform: manufacturing-on-demand when a new opportunity arises.
THE BREAKDOWN | |
---|---|
Organization | Skelex |
Location | Rotterdam, NL |
Product | Industrial Passive Exoskeleton |
Industry | Automotive, aerospace, shipbuilding |
Why us? | On-demand manufacturing |
The Result | Flexibility to start production whenever necessary |
Technology | CNC machining, 3D printing, Vacuum Casting, Sheet Metal |
Materials | Aluminum 6061, PLA, Silicone |
The Team
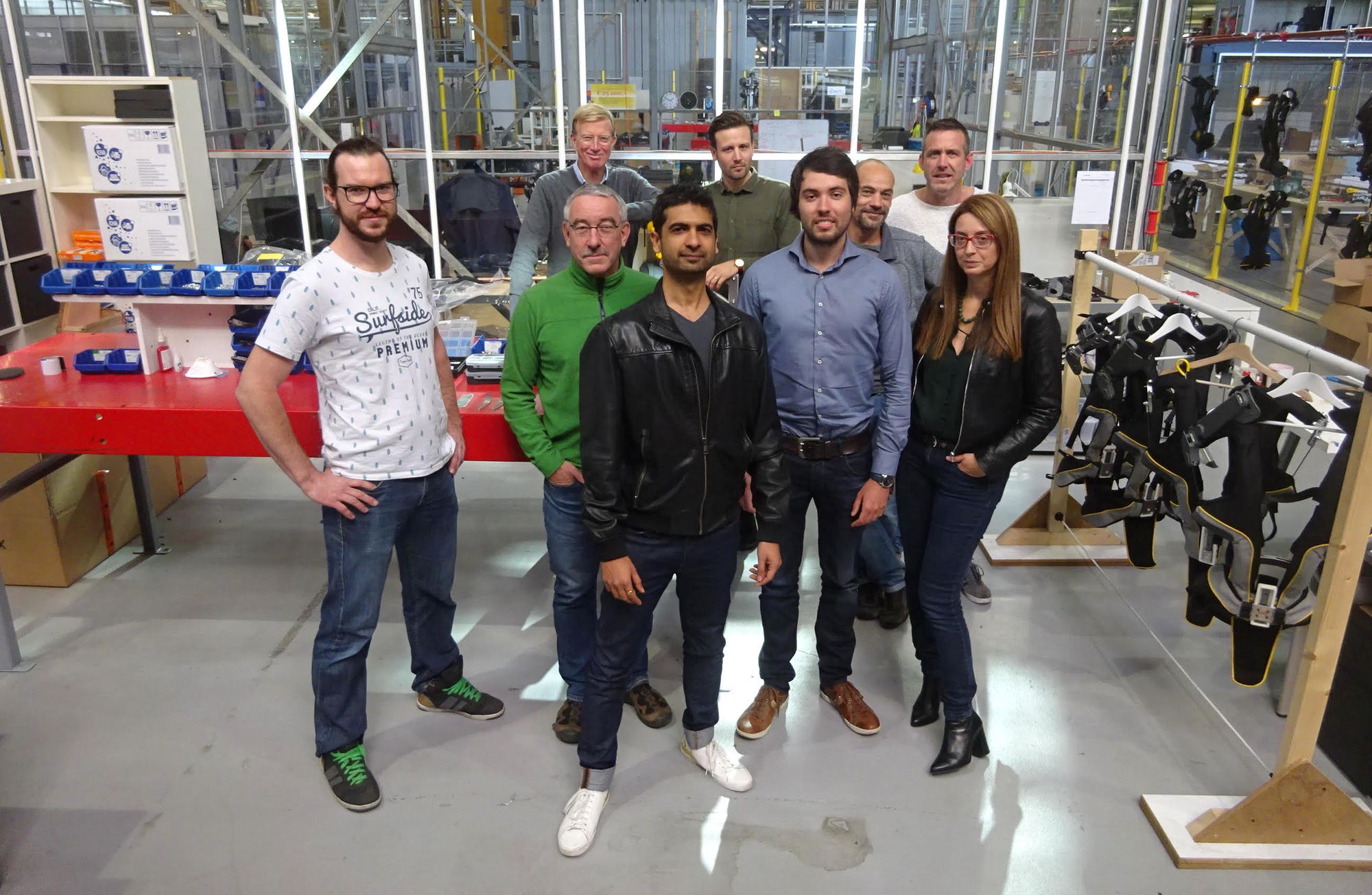
The idea behind Skelex was born through… music. Gaurav Genani, the founder of Skelex, felt fatigue after playing the electric guitar for a long period of time. After studying engineering at Delft University, he realized that this is a big issue that many industrial workers face. Gaurav explains:
“Millions of workers around the world have to operate in difficult postures and make repetitive movements over and over again. This is a very tiring job and these guys are working for decades. Eventually, the bodies deform and they get injured. So, our device is like a bicycle for the arms, making this heavy work lighter.”
Skelex was founded in 2013 and the first Skelex suit was ready in 2015. Today, Skelex has grown to a company of 10 employees with a small R&D and engineering team. They work with manufacturing organizations in the automotive, aerospace and shipbuilding sectors, such as Airbus and the vehicle maintenance unit of the Dutch Army.
Their exoskeleton is currently on version 1.4, weighs 4.2 kg and costs a few thousand dollars USD. The team has big aspirations and is already working on their next-gen exoskeleton that will be 50% lighter and 10 times cheaper.
The biggest challenge
The Skelex design team believes that an industrial passive exoskeleton needs to be simple, light, compact and feel like an extension of your body. This is to ensure that the suit doesn’t get in the way and that people will actually use it and integrate it into their daily routine.
Since passive exoskeletons don’t have any electronic motors or sensors, they are in reality simple mechanical systems that work in close collaboration with the human body. It is the human body where the design process begins for Skelex. Through extensive and hands-on ergonomic testing Michael Kuiken, the human kinetic engineer of the team, passes the design requirements to Ivo de Looij, the mechanical engineer, who then creates the CAD designs and ensures that they are manufacturable.
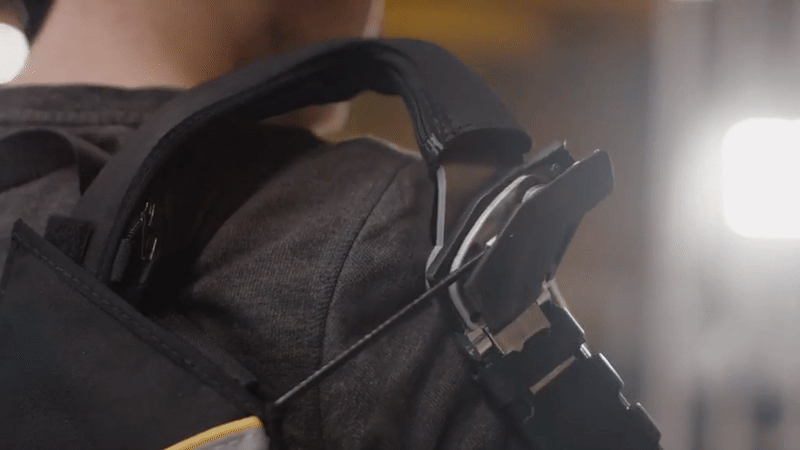
But the ergonomics and mechanical design are not the biggest challenges for Skelex. Gaurav explains:
“It is not a technological challenge, far from it. This is a user challenge, a societal challenge. We need to convince people that this technology is helpful and to accept it. It took years for other health and safety equipment, such as the hard hat, to be adopted.”
In practice, this means that it is uncertain when the next order will come as it takes time to make such societal changes. It is not financially viable for a small company, like Skelex, to lock their capital in stock that they might not sell soon. So, they had to find a different solution...
On-demand manufacturing
Instead of keeping stock, the Skelex team decided to manufacture their suits on-demand whenever a new opportunity arose.
This also gave them a key advantage over their competition: flexibility. If a customer had a specific need, they could re-engineer and re-manufacture an exoskeleton specifically tailored for that client. Gaurav mentions:
“In the early stages of a company, flexibility is important because you don’t know when an order will come. The flexibility we give to our customer is one of the main reasons we are still doing business. If there is an opportunity we go for it.”
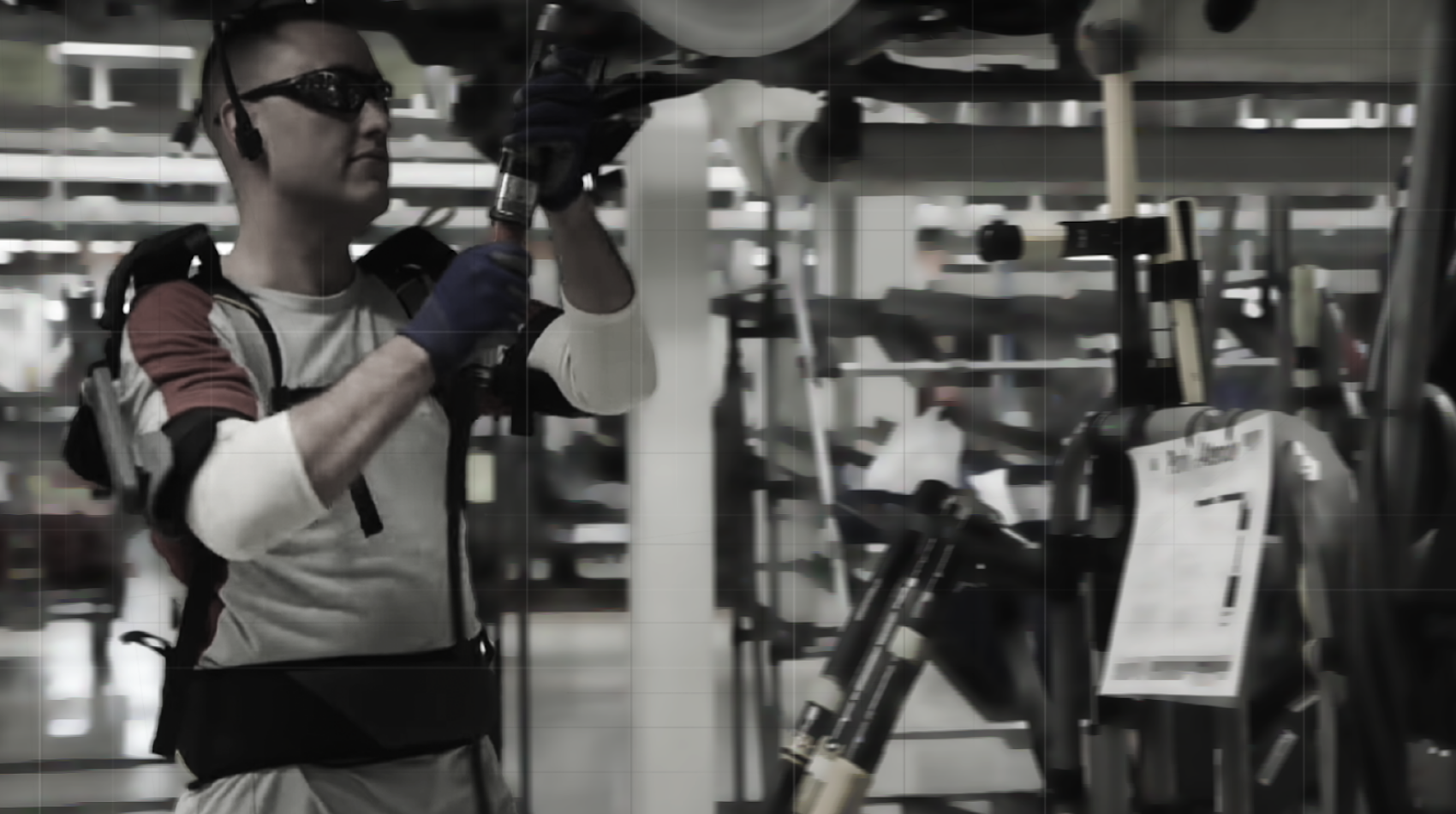
The “all-in-one” manufacturing solution
Skelex found the hard way about the inefficiencies of “traditional” outsourcing and on-demand manufacturing, especially when it comes to metal parts. Most CNC suppliers they contacted were either very expensive for smaller orders, took a long time to provide a quote, or were not capable to manufacture all the components of the exoskeleton.
This is until they found our network. Gaurav goes onto explain their experience:
“We started with low-cost 3D printing; we then found out that the platform also has CNC services; it was easy to get information and quotes and we got our sample parts quickly; we didn't have time to waste asking different suppliers what can they do, what is their price etc. Using the network was fast, convenient, smooth, and profitable.”
Another reason they decided to use our services for their on-demand manufacturing needs, was the great customer experience. With the support of our team, any issues that may be created during manufacturing would be quickly resolved, ensuring they could deliver their products on time to their clients.
📍 Download our free engineering guide to CNC machining here
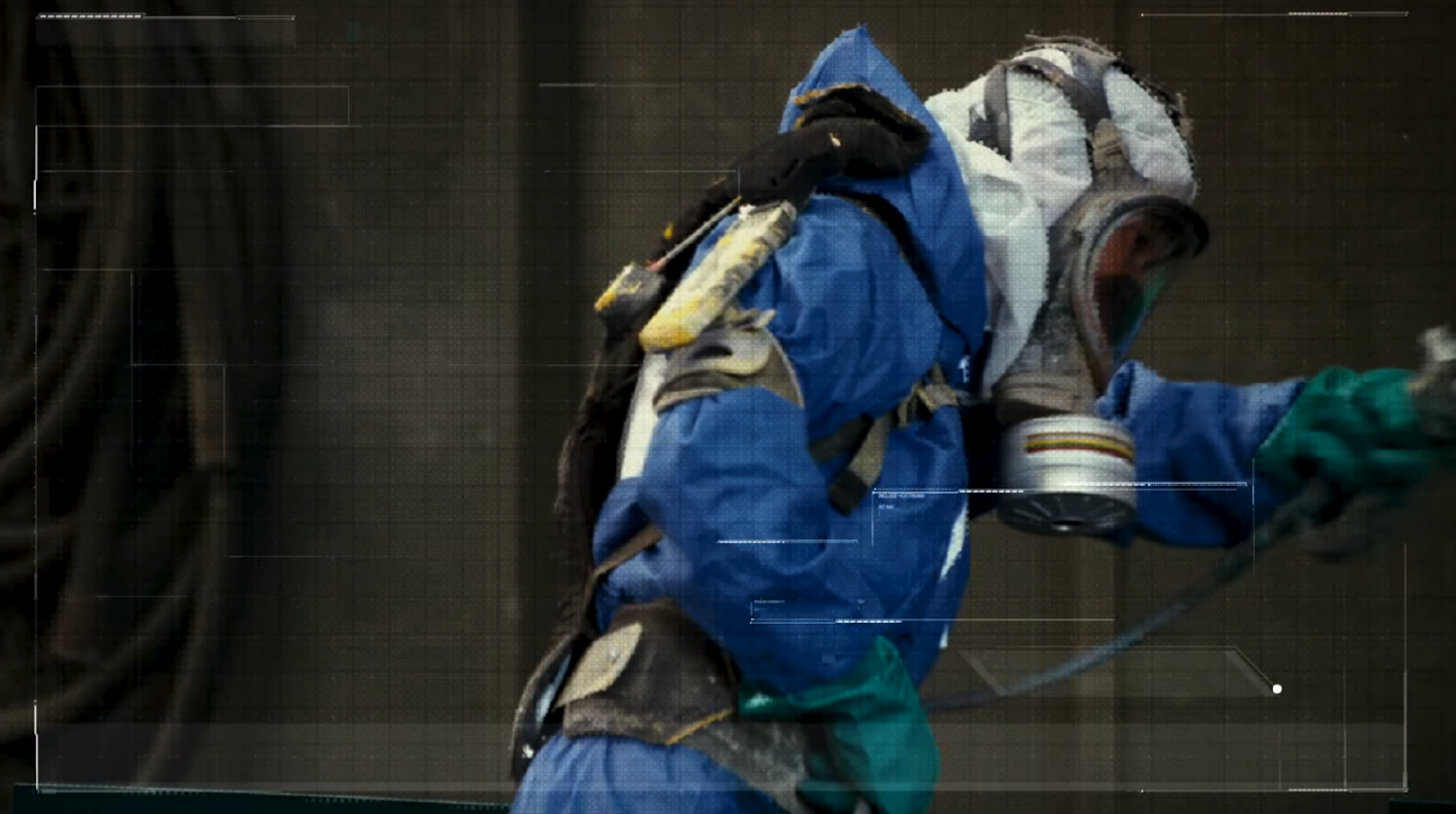
Ramping up production
Currently, Skelex is preparing to ramp up production from 10s to 100s (and soon to 1000s). Technologies that are very cost-competitive at lower volumes, such as CNC machining services and 3D printing, cannot keep up at higher production run.
For this reason, they are now redesigning their exoskeleton to be manufacturable with other technologies, like vacuum casting or injection molding for the plastic components, and sheet metal fabrication for the metal parts.
Ivo de Looij, the mechanical engineer of the team, goes to explain how we can help them scale up their production:
“We've recently learned that the network also offers Vacuum casting and Sheet Metal. We can now source more than 95% of our plastic & metal parts through the technologies we offer.”
Lifting the future
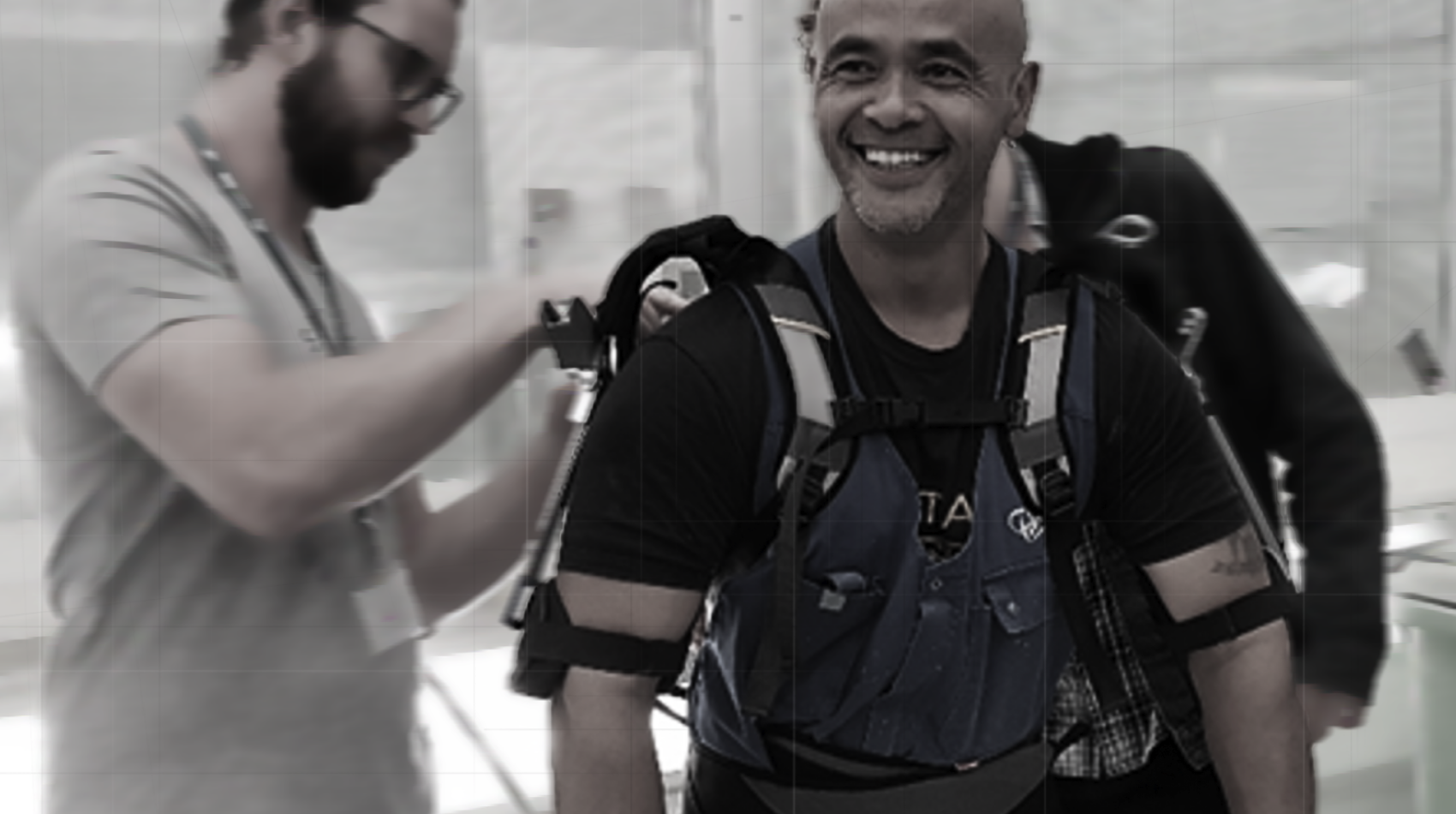
The Skelex team has done exceptionally well at designing an industrial passive exoskeleton that can improve the quality of life for millions of workers globally. Their efforts also played an important role in raising awareness of the issues to the decision makers who look after the well-being of their workforce.
The Skelex suit shall continue getting smaller and more comfortable to use. By taking advantage of the economies-of-scale, it will also become more affordable. This will speed up the mass adoption of the technology.
Protolabs Network will continue supporting their efforts, by making sure they have easy access to a large network of Manufacturing Services that offer multiple technologies including (and not limited to) 3D printing, CNC machining, Injection Molding, Sheet Metal, and Vacuum Casting.
Learn more about the Protolabs Network platform here.
⚡Or start uploading your parts today to get an instant quote.