Inventas worked with their client to design, test and manufacture a cutting-edge bicycle trailer. The biggest challenge? The short and hectic Nordic summer was rapidly approaching. Missing the deadline would mean a one year delay for the entire project. To tackle this Herculean task, the engineers of Inventas turned to Protolabs Network to move to full-scale production of 95,000 parts with injection molding in an extremely tight timespan.
When it comes to sustainable transportation, nothing compares to a bicycle. It is much faster than walking and is an environmentally friendly way of doing your daily commute. Plus, with some additional hardware, riders can carry their heavy shopping bags, bring their kids to school or transport heavy objects that don’t fit in a backpack.
The client of Inventas focuses on helping people live sustainable lifestyles. Their most recent project is to design a bicycle trailer that is user-friendly and suitable for an urban lifestyle. In October 2017, the company set out to bring a new bike trailer design to the market.
Their main technical requirement? It must collapse sideways with as few levers as possible. According to their CEO, there are several options on the market, but these are either too wide to store or are difficult to disassemble.
“Our bike trailer collapses sideways. This is different than all other trailers on the market that use a fixed frame. Traditional trailers collapse so they are flatter. But they are still just as wide and cumbersome to store.”
The Breakdown | |
---|---|
Organization | Inventas |
Location | Norway |
Product | Bicycle trailers |
Industry | Urban Transportation |
Why Protolabs Network? | One-stop solution for manufacturing |
Technology | injection molding |
Materials | Glass-filled Nylon, POM. |
An Innovative Design
After looking at some of the previous patents and available technology, the design team decided to build an entirely new bike trailer. “People have been trying to do [this type of design] before, but no one has really created a mechanism that is convenient as well as practical.”
To properly engineer this new trailer design, the company partnered with Inventas. The engineering firm offers comprehensive product design services. Inventas’ team worked with their client to draft, simulate and test the new geometry and bring it to production over the course of just three months.
“We needed to focus on technical parameters like weight and strength ratio, as well as what materials we wanted to use to make an environmentally friendly bike trailer,” says Andre Ingolfsen, project manager and industrial designer at Inventas.
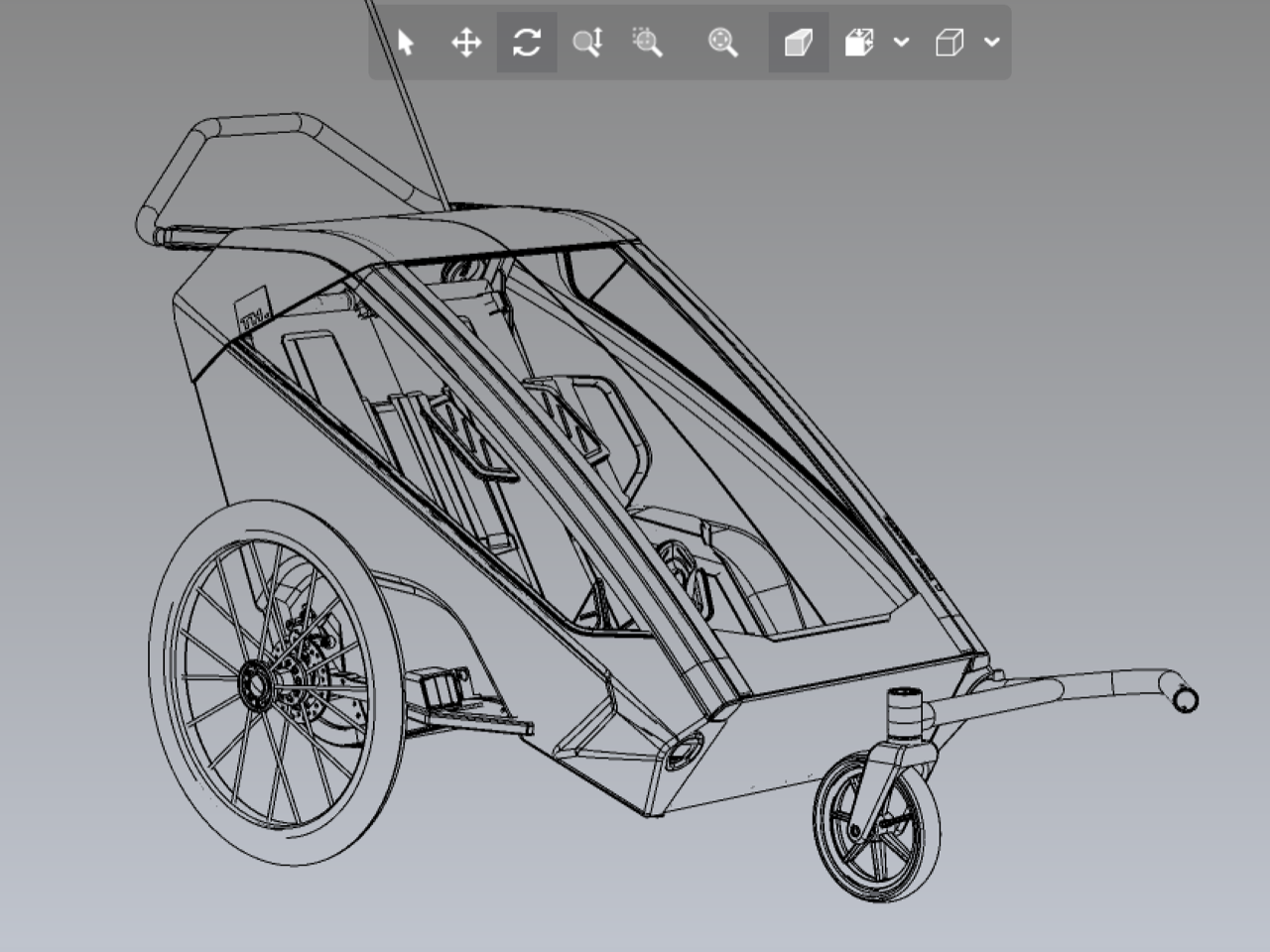
Manufacturing Challenges
After finalizing the design from over a year of work, Inventas faced another big challenge: a tight production deadline. “Our client wanted to launch the product in 17 weeks, and we struggled to find suppliers and partners that could deliver within such a short time frame,” said Ingolfsen.
Ingolfsen explained that Inventas does not do any manufacturing in-house, so they needed to work with a service provider that could help them while they were simultaneously finalizing the trailer design. “We have some small scale 3D printers for internal use on projects; otherwise we use partners externally for prototyping and production,” Ingolfsen says.
To meet all technical and usability requirements, the bike trailer is made of an aluminum frame and plastic connecting parts. The aluminum parts help keep the trailer light during transport and storage, but also have the necessary stiffness and strength.
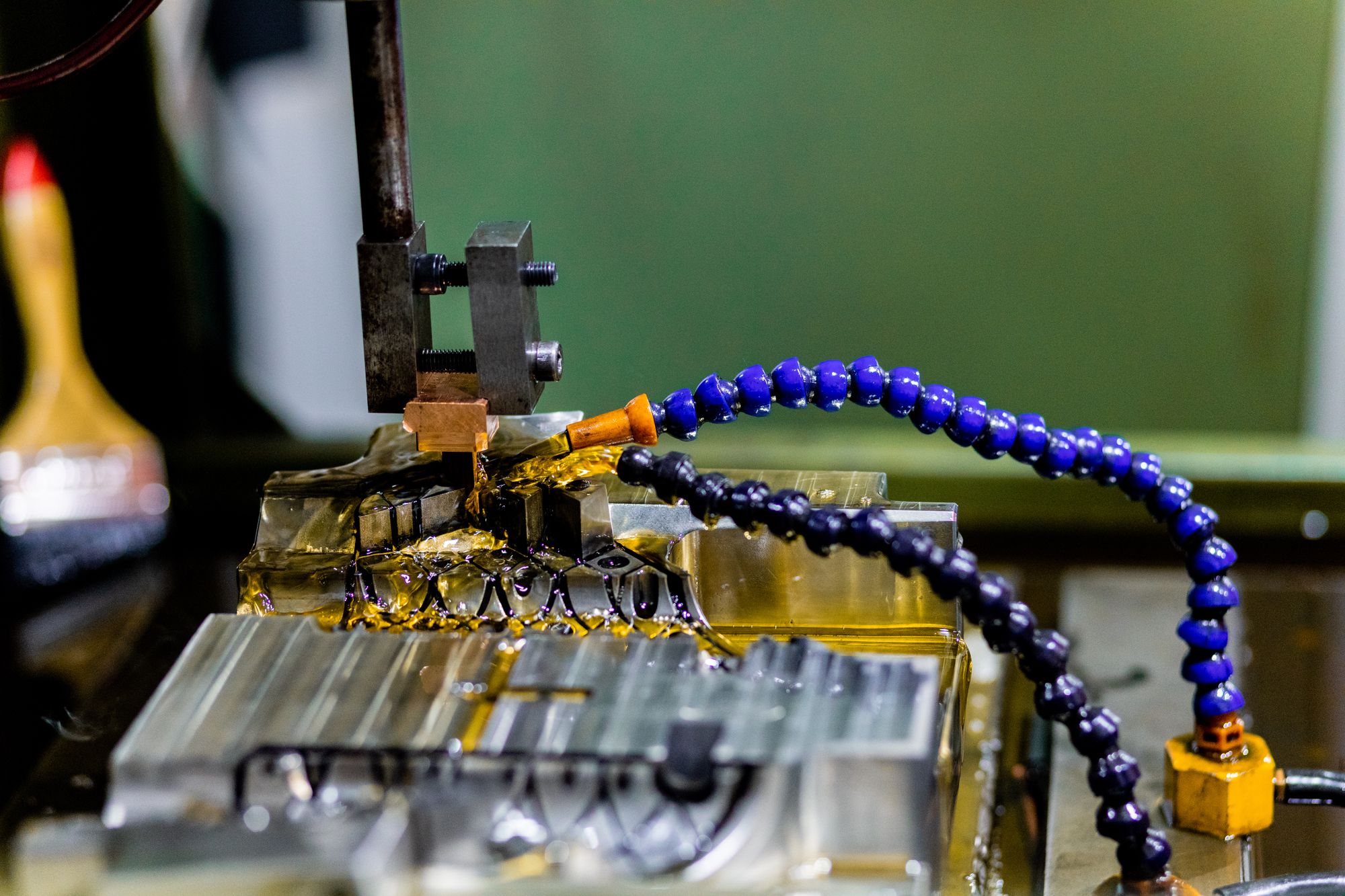
The biggest challenge for this project was designing all plastic components that allow the trailer to fold sideways. The trailer has approximately 30 different components to enable users to manipulate the frame for usage or storage easily.
Due to the number of parts in the bike trailer, Inventas needed a manufacturing partner that could produce everything in such a short time frame. This proved to be tricky, especially since they also needed a supplier that would support their full-scale production requirements.
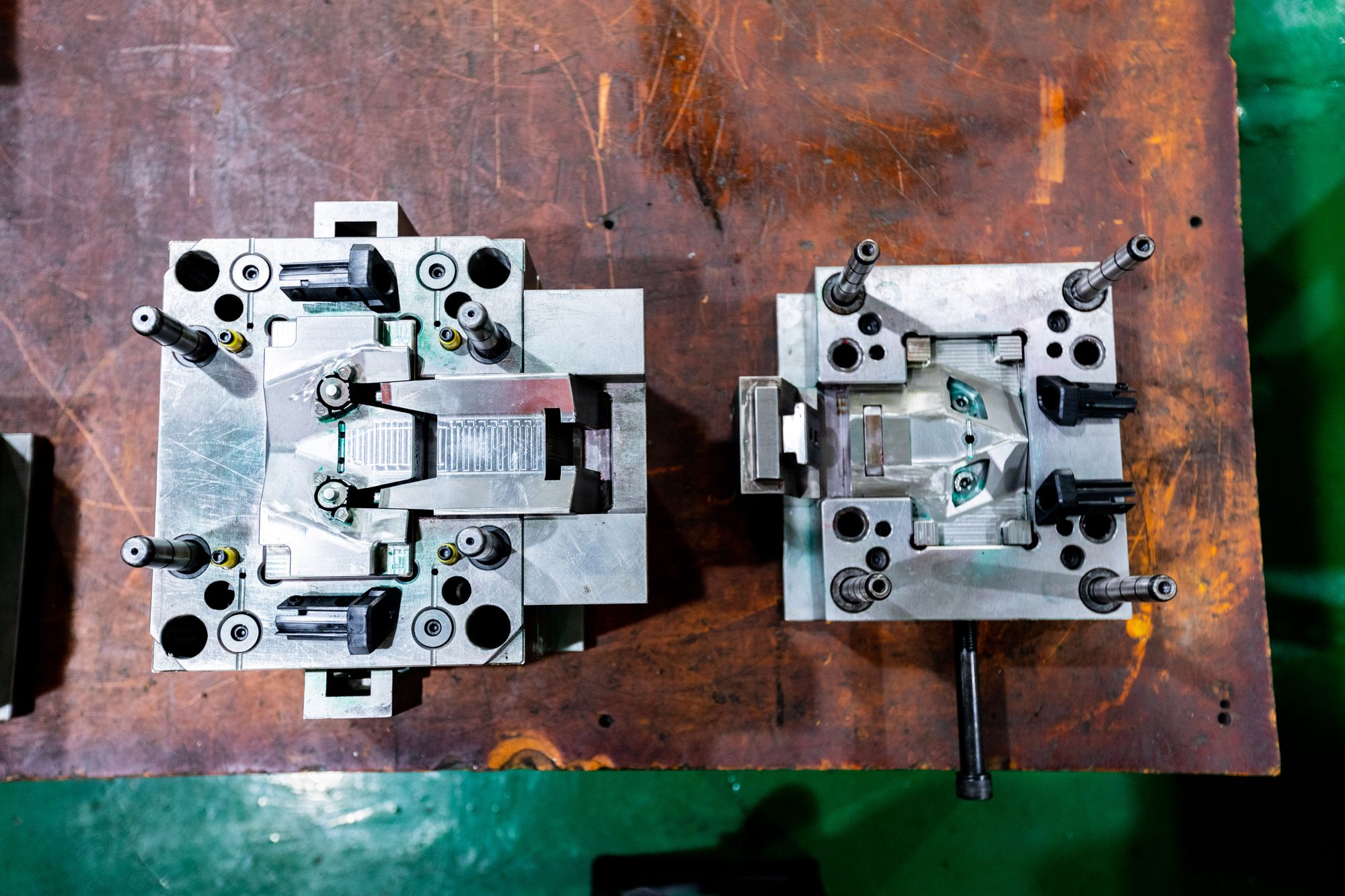
The Need for Speed
Even with such a tight deadline, Protolabs Network was able to keep Inventas on schedule and made it easy to start manufacturing once engineers reached the final design. Throughout the entire process, Protolabs Network helped provide instant quotes and manufacturability feedback, so Inventas didn’t need to wait for production costs or spend extra time finding a supplier.
To produce all the plastic parts, Inventas selected glass-filled nylon (PA6-GF30) and POM for their high stiffness and strength-to-weight ratio. Engineers decided to use injection molding as the primary manufacturing method, which supports detailed geometry, multiple types of plastic and quick turnaround for their production volume; Inventas needed to manufacture a total of 95,000 parts made out of 29 different molds.
To get all of the parts they needed, Inventas used multiple Protolabs Network Manufacturing Partners and split their order into three large batches. By doing this, the firm was able to machine an order while finalizing the next group of parts, reducing any potential delays.
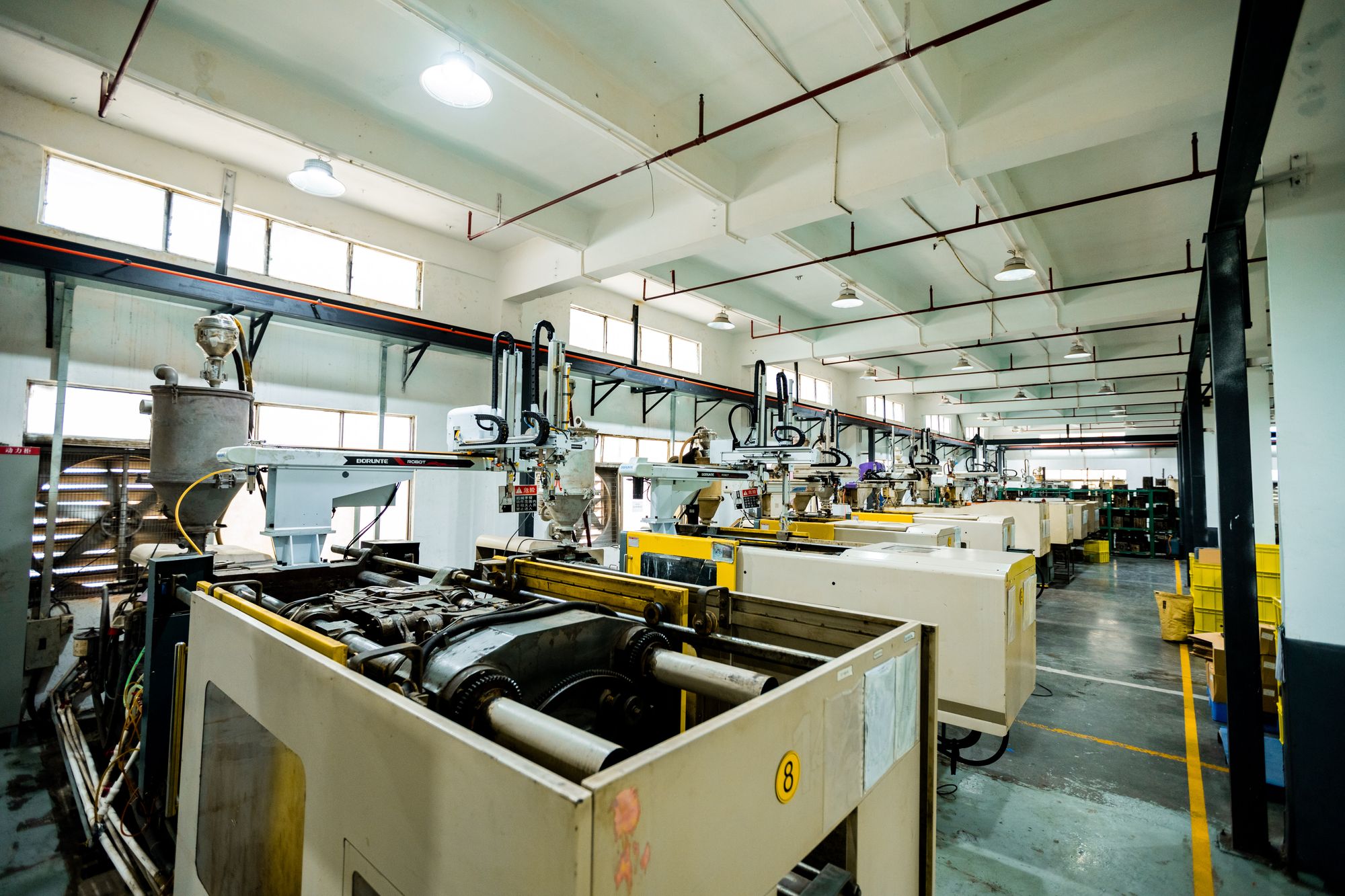
📍 Download our free engineering guide for Injection Molding here
In the meantime, Protolabs Network helped coordinate production and provided one main point of contact for Inventas. This gave Ingolfsen’s team the time to focus on perfecting the bike trailer design, instead of having to deal with multiple service providers and figure out how to manufacture all of the trailer parts.
By simplifying the choices that Ingolfsen and his client had to make to get the trailer parts, Protolabs Network helped Inventas not only meet production deadlines but bring a product from a drawing to reality.
“The Protolabs Network team took immediate action to find a solution to our manufacturing problem, and did so in a very structured and clear manner, allowing for both the project team and our customer to make rapid decisions,” Ingolfsen says.
Riding Ahead
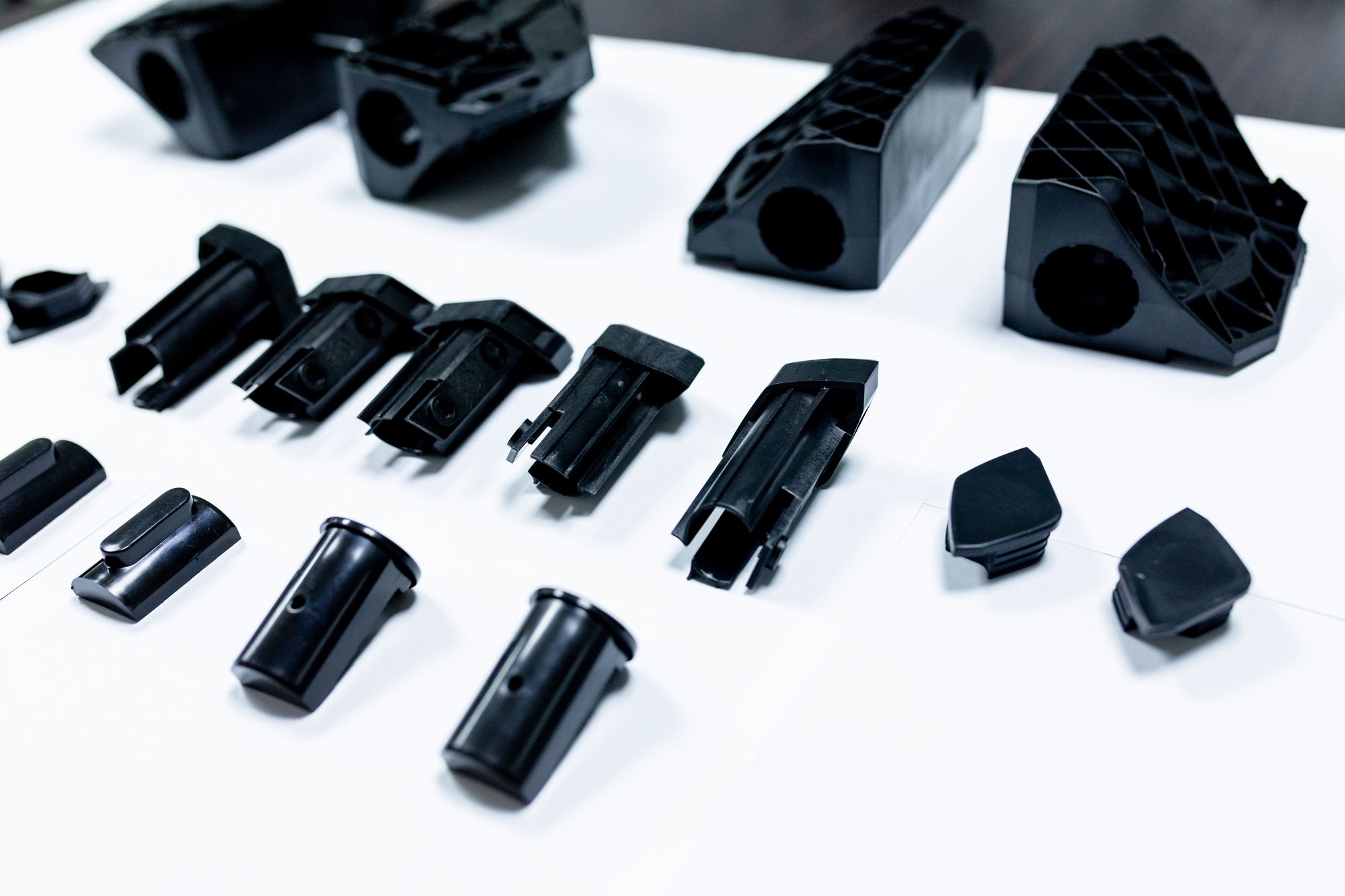
The result from the partnership between Inventas and their client was truly remarkable. They achieved to bring to life a project in record time. Their easy-to-use and urban-friendly bike trailer can make more and more families across the globe leave their car behind and embrace this alternative means of transportation, supporting a greener future.
For Protolabs Network, this was a unique project that proved the power of our distributed manufacturing network. By providing a single point of contact, our team helped Inventas access global manufacturing capacity while allocating all their full attention to what matters the most: finalizing their designs and bring an innovative product to the market.
Learn more about the Protolabs Network platform here.
⚡Or start uploading your parts today to get an instant quote.