The challenge
Otect is a boutique hardware startup that creates pristine, high-quality lens caps for Leica cameras. One of the in-house brands of Engineering Lab, a hardware design agency in The Netherlands, Otect has strict functional and cosmetic requirements for its products. The lens caps have to match Leica’s quality standards and attach exactly, so every piece has to adhere to high tolerancing requirements and have perfect surface finishing.
How we helped
Otect used our quote builder to get instant pricing on designs, which accelerated the iteration process within the startup’s budget. The company also benefitted from the platform’s onboard DFM analysis, as well as guidance from an in-house injection molding specialist. We helped Otect produce a premium, perfectly fitting lens cap, while amping up the speed and cost-efficiency without compromising on the elevated quality requirements.
How on-demand manufacturing accelerated product development
Founded in 2020, Otect is a hardware startup that makes specialty lens caps for Leica products. Otect is one of the in-house brands of Engineering Lab, a design agency that helps entrepreneurs and startups develop proofs of concept and prototypes. Helming both is engineer and product designer Michael Jones.
Having worked with companies to advance their hardware since 2015, Jones knows a thing or two about how tricky it can be to source high-quality parts. Product development is an intensely iterative process, and any roadblocks, such as being unable to get parts on a budget and within a given timeframe, can swiftly delay or even derail that process.
This being the case, Jones has strategically outsourced part sourcing with on-demand manufacturing whenever in-house production wasn’t feasible. He’s collaborated with us to deliver clients’ proofs of concepts and prototypes for most of his career, having worked with the platform since the 3DHubs days.
Initially, the main benefit of working with our network was to source 3D-printed parts locally within a day or so. This was easier than purchasing several 3D printers and learning how to get the most out of them, and it freed up time to work on product design in parallel. Having a dedicated, on-demand partner also cut costs significantly.
“I was able to iterate on the design and get real-time cost updates,” said Jones. “I managed to reduce the cost of parts for my clients.” They evolved from a 3D printing company to a comprehensive manufacturing service provider in 2021, which coincided with the birth of Engineering Lab, and Jones stuck with us to offer clients the speed and quality he’d leveraged, now in more manufacturing technologies.
Most significantly, Jones used our platform to grow his own entrepreneurial venture, Otect.

Sourcing custom parts to uphold a legacy of premium quality
Otect presented Jones with a niche manufacturing challenge. The product—called the Q-Cap after Leica’s Q line—needed to match Leica’s premium quality and aesthetics, from prototyping well into production. This meant the team needed to source high-quality components with excellent surface finishes and specific colors similar to the hue of a Leica camera.
“Every part needs to be high quality, from the aluminum stock and the machine settings to the bead blasting and anodizing,” said Jones. “It’s taken a lot of work to get the Leica standard.”
As Michael had already worked with us, he immediately started using the platform for 3D printing and CNC machining prototypes. At first, he sourced as-machined CNC parts and finished them in-house, but as demand grew, this approach wouldn’t be as viable.
The project quickly scaled from several hundred units to over 3,000 lens caps, requiring a shift from sole CNC production to a combination of CNC machining and injection molding. According to Jones, the ability to source parts using different technologies all from one platform was “game-changing.”
Our onboard design for manufacturability (DFM) analysis and advice from engineers also gave Jones and his team a boost.
“One of the barriers to injection molding is the mold cost,” said Jones. “It’s quite a big commitment, typically in the range of thousands of euros, so you want to make sure your designs are as correct as possible and to limit any changes.
“Working with specialists to get the design correct the first time was really helpful, especially as all the changes were quite cost-effective. It was really helpful to have someone to spar with and test out new ideas on the platform, get a new price for them, and ultimately go into production.”
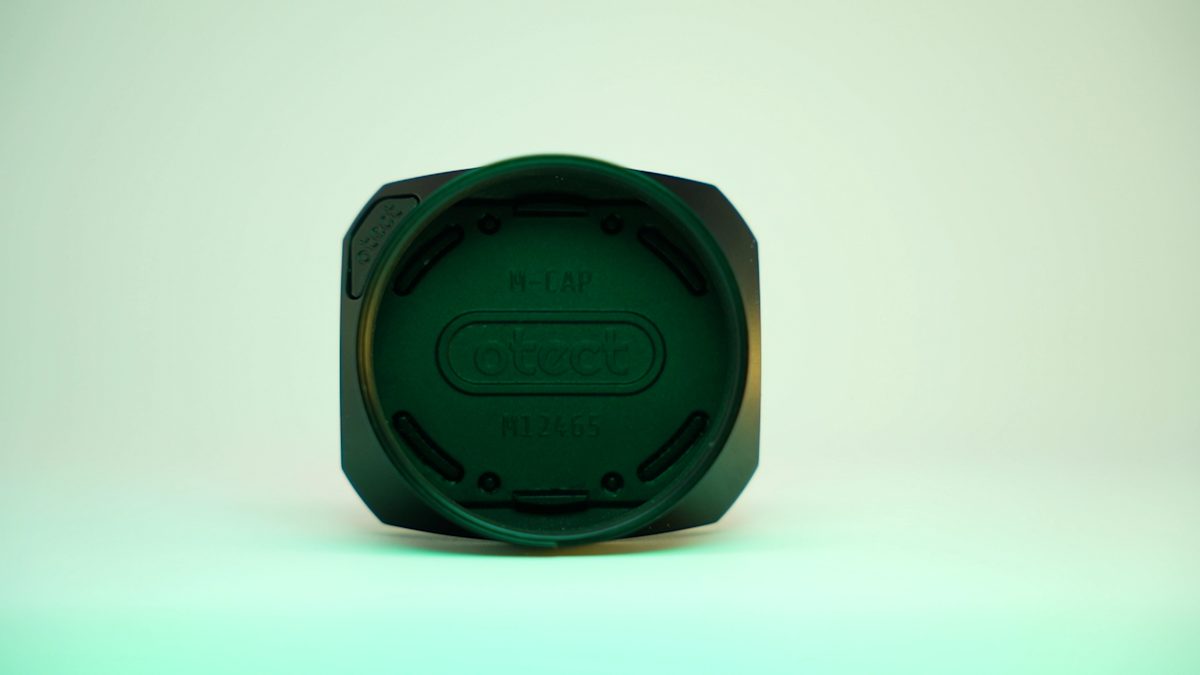
Scaling with a single, dedicated supplier
Aside from the added advantages of instant quoting and DFM advice, our network also provided Jones with the possibility of having one supplier for prototyping as well as production. The Otect product has no room for error, and it took quite a while to get the accuracy and surface finishing, among other properties, to the quality required.
The design itself comprises three distinct components, a plastic shield that covers the lens, a spring that attaches to the shield and a metal cap protecting the entire assembly. Sticking with us allowed Otect to iterate swiftly and move from prototyping to higher volumes of production without having to bring different manufacturers up to speed on all the strict production needs.
Having one supplier for all three components ensures that the parts, made via CNC machining and injection molding, snap together perfectly and fit the camera. Using several suppliers with their own quality standards could have made this less feasible, and assembly is crucial for Otect. Getting parts toleranced the same way and with the same surface finish quality affords Jones and his team a 30-second assembly time, which makes it easier to meet order quantities in the thousands.
As of late 2022, Otect is shipping over three thousand lens caps to clients, including Leica itself. The company is rapidly scaling in its production aspirations, and Jones is confident that he’ll continue to grow with us as the dedicated Otect supplier. According to Jones, “ we’ll be able to keep working with the network and producing parts moving forward.”
Did you know we offer local sourcing for CNC machining?