Introduction to laser cutting
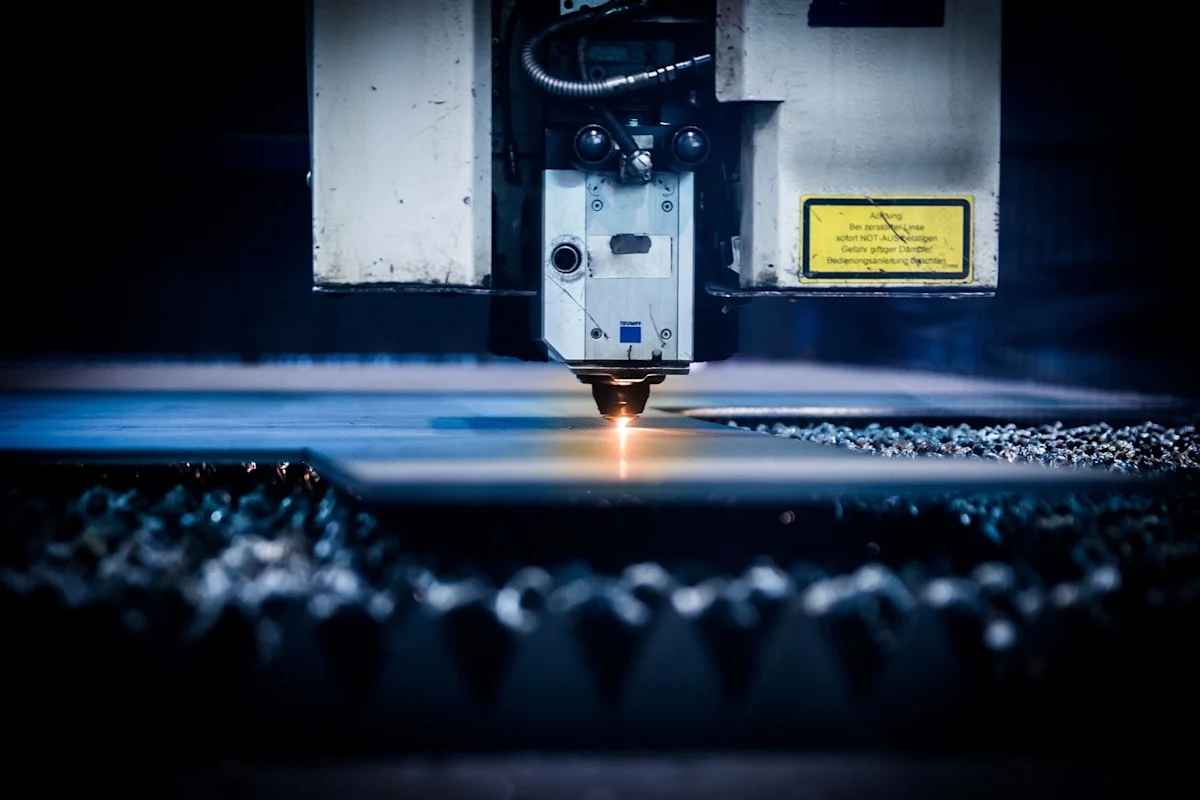
Key takeaways
- Laser cutting is excellent for both one-off jobs and low-to-medium volume production orders
- Use laser cutting to achieve precise, easy, and accurately reproducible parts
- Laser cutting is perfect for batches producing different parts form the same base material, with little to no change in setup
What is laser cutting?
Laser cutting is a high precision CNC thermal process that uses a high-power laser beam to cut, melt, or burn a material sheet. It uses a focussed beam of light to cut and etch sheet material to the design specification. Ideal for a variety of material types (including metals, wood and polymers), it is capable of producing complicated parts without using a custom-designed tool.
The process is suitable for both one-off jobs and low, medium volume production due to its high repeatability. Laser cutting is particularly useful for the fabrication of metals (steel, brass, aluminum, or nickel). It has become a firm favorite in the production of medical products owing to its high precision, reliability, and resultant smooth finishes.
In contrast to CNC machining, laser cutting works with sheet material, producing shapes and forms no more profound than 10mm (depending on the material type).
Learn about the different types of sheet metal fabrication →
In this article, the key differences between the main types of laser cutting are introduced, and the characteristics of the process are discussed. By the end, you will have an overview of the basic principles of the technology and how these relate to its key benefits and limitations.
Advantages & disadvantages of laser cutting
Advantages
Laser cutting offers near unparalleled flexibility when working with sheets of material. It can cut, engrave, or score a variety of different shapes from the same material thickness without changing setup - regardless of complexity or size.
Learn about Protolabs Network’s sheet metal fabrication capabilities here →
Laser cutting can give exact cuts and marks, suitable for anything from bottle openers to circuit boards. This is both faster and more efficient than manual fabrication methods.
Disadvantages
Working with material over 100mm thick can become difficult, depending on laser type.
High energy consumption can lead to relatively expensive running costs. Skip to the costs section of this article for more details.
Main types of laser cutters
In the fabrication of sheet metal parts, manufacturers make use of three basic types of laser cutters: CO2 gas, crystal, and fiber.
CO2 gas
Pumped using electric discharge, these cutters use a laser composed mainly of carbon dioxide, helium, and nitrogen. Emitted at a wavelength of 10.6mm, a CO2 laser can pierce materials thicker than fiber cutters with a similar power output of the same power. Efficient and low cost- these are widely used in manufacturing.
Crystal laser cutters
Beams generated from YVO, or YAG, crystal laser cutters are capable of cutting through stronger and thicker materials than CO2 cutters, due to their smaller wavelengths and higher intensity. The machine parts wear more quickly than gas cutters due to their higher concentration and are therefore more expensive to run.
Fiber laser cutters
Belonging to a family of solid-state lasers (a laser that uses a solid gain medium), these tools use fiberglass to amplify base seed lasers. These are up to 3 times more energy-efficient than gas-based cutters. Fiberglass cutters have no moving parts (like fans for gas circulation or mirrors in the light-generating source), resulting in a tool that is far easier to maintain. As opposed to carbon gas-based lasers, fiberglass alternatives can cut thin sheets faster while operating at the same power and are also able to cut reflective material materials without consequence.
Laser cutter comparison overview
CO2 laser | Crystal laser | Fiber Laser | |
---|---|---|---|
State | Gas based | Solid state | Solid state |
Material type | Wood, acrylic, glass, paper, textiles, plastics, foils and films, leather, stone | Metals, coated metals, plastics, ceramics | Metals, coated metals, plastics |
Pump source | Gas discharge | Lamp, diode laser | Diode laser |
Wavelength (µm) | 10.6 | 1.06 | 1.07 |
Efficiency (%) | 10 | 2 - lamp, 6 - diode | <30 |
Spot Diameter (mm) | 0.15 | 0.3 | 0.15 |
MW/cm2 power density | 84.9 | 8.5 | 113.2 |
How a laser cutter works
In laser cutting, a part is placed onto a bed, where material is then etched or cut from a sheet using a laser. Here is a simple overview of the laser cutting process:
- Power is adjusted based on the material being cut and the thickness of the sheet. A typical laser beam has a diameter of 0.1 - 0.3mm (power of 2-3kW.)
- A CAD drawing is converted into a series of commands that can be interpreted by the laser cutting machine. This is usually done by the machine operator based on its standard working procedure.
- A sheet of material is then cut to size, placed on the machine's bed workpiece is clamped onto the bench, making sure that the orientation is straight (not slanted).
- The material is now cut or scored by the laser. The light is emitted from a resonator; this is an airtight glass tube composed of two facing mirrors and filled with diode activated gases. It’s then emitted from the cutting head, where light from the resonator is focussed onto a curved lens, where it is focused into a single beam).
- Multiple parts can be cut from the same sheet and will run on the same program.
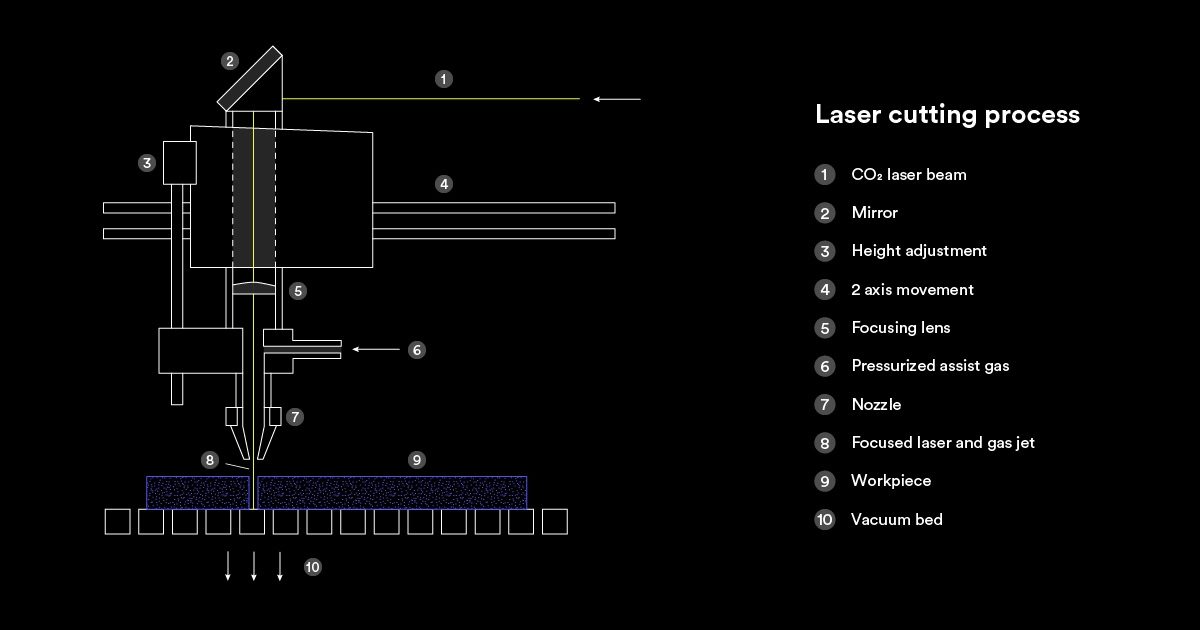
Metals used for laser cutting
Laser cutting is a versatile method of manufacture and can be used to cut a range of materials including metals, plastics, wood, paper and textiles. When it comes to metals, steel cuts better compared to aluminum and copper. This is because steel, unlike aluminum and copper, reflects light and thermal energy, which otherwise can lead to warping. Below you can find a summary of the most common metals used for laser cutting.
Materials | Characteristics |
---|---|
Aluminum 5052 | + Exceptional finishing qualities (easy to anodize) + Moderate to high strength - Low hardness |
Aluminum 5754 | + Higher-strength than 5052 + Corrosion-resistant + Good machinability |
Copper C110 | + Excellent thermal & electrical properties + High ductility - High thermal conductivity |
Stainless Steel 304 | + Excellent mechanical properties + Excellent corrosion & acid resistance - Relatively difficult to machine |
Stainless Steel 316L | + Excellent mechanical properties + Excellent corrosion & acid resistance - Relatively difficult to machine |
Mild Steel 1018 | + Semi-magnetic + Relatively easy to machine - Poor corrosion resistance |
Laser cutting costs
The cost of laser cutting can vary massively, depending on material thickness, material properties, and type of laser. As each part is so different, the easiest way to predict a price for a specific metal part would be to upload your CAD file to Protolabs Network for a free and instant quote.