What if you could fight climate change with a fleet of tree-planting drones? That’s what DroneSeed is striving towards. With custom-built drones for each project and tight turnaround times, the Seattle-based startup leverages rapid manufacturing technologies to stay nimble.
Organization | DroneSeed |
Location | Seattle, USA |
Industry | Aerospace, forestry |
Product | Drones as a service |
Technology | 3D printing (FDM, MJF) |
Materials | PLA, nylon, carbon fiber |
Why us? | The amount of parts DroneSeed wanted to produce went far beyond their in-house capacity |
Results | Hundreds of parts delivered fast at affordable prices |
Tackling wildfire reforestation
DroneSeed is disrupting the status quo. The team has developed an innovative route to reviving forests that have been ravaged by wildfires. 6 times faster than a human tree-planter, DroneSeed’s fleet of drones are retrofitted to drop seed vessels in scorched soil to develop and flourish.
And DroneSeed is constantly searching for new angles to improve efficiency. Grant Canary, CEO at DroneSeed adds, “The company’s biggest goal is to boost seed survival to maximize post-fire responses and get the greatest survival rate before invasive species come in.”
Designing tailormade drones
Part of promoting seed survival includes building custom-made drones. “There’s no one-size-fits-all when it comes to reforesting,” explains John Thomson, Senior Drone Systems Engineer at DroneSeed, “because the applications are so unique for each client, DroneSeed uses a mix of off-the-shelf and custom parts.”
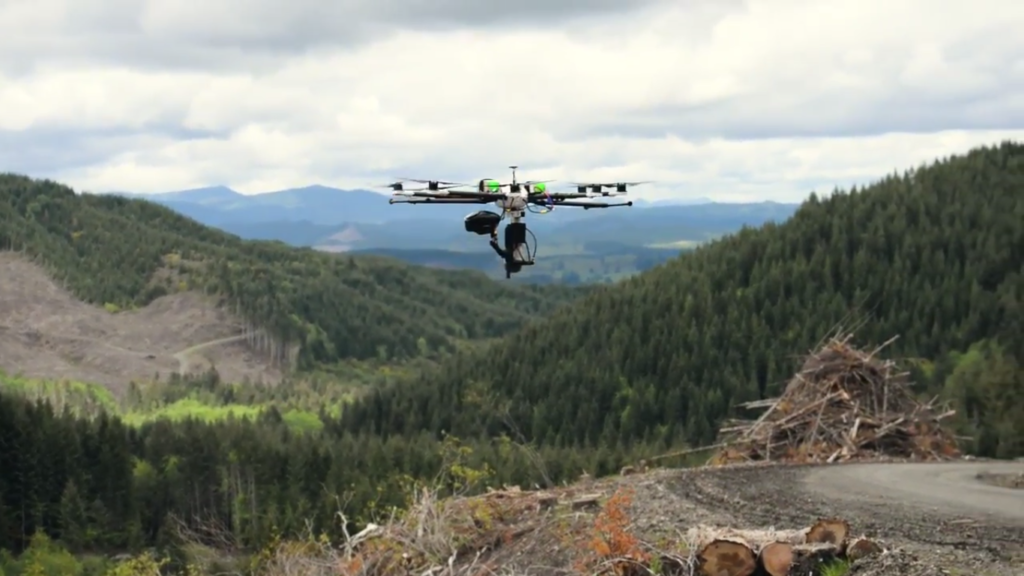
Off-the-shelf parts for DroneSeed are things like the composite fuselage - a part too complex for the service-focused business to manufacture themselves.
For each project there’s a tight turnaround. On average DroneSeed manages to ready a fully customized payload solution from initial order to completed design in 2 months.
PLA for flexibility, MJF for strength
DroneSeed opt for PLA for design validation and field testing. Operators handle drones with work gloves (instead of kid gloves) so the material needs to be able to accrue minimal damage. Oncee a design has been validated, the parts are manufactured in MJF to outfit the production fleet.
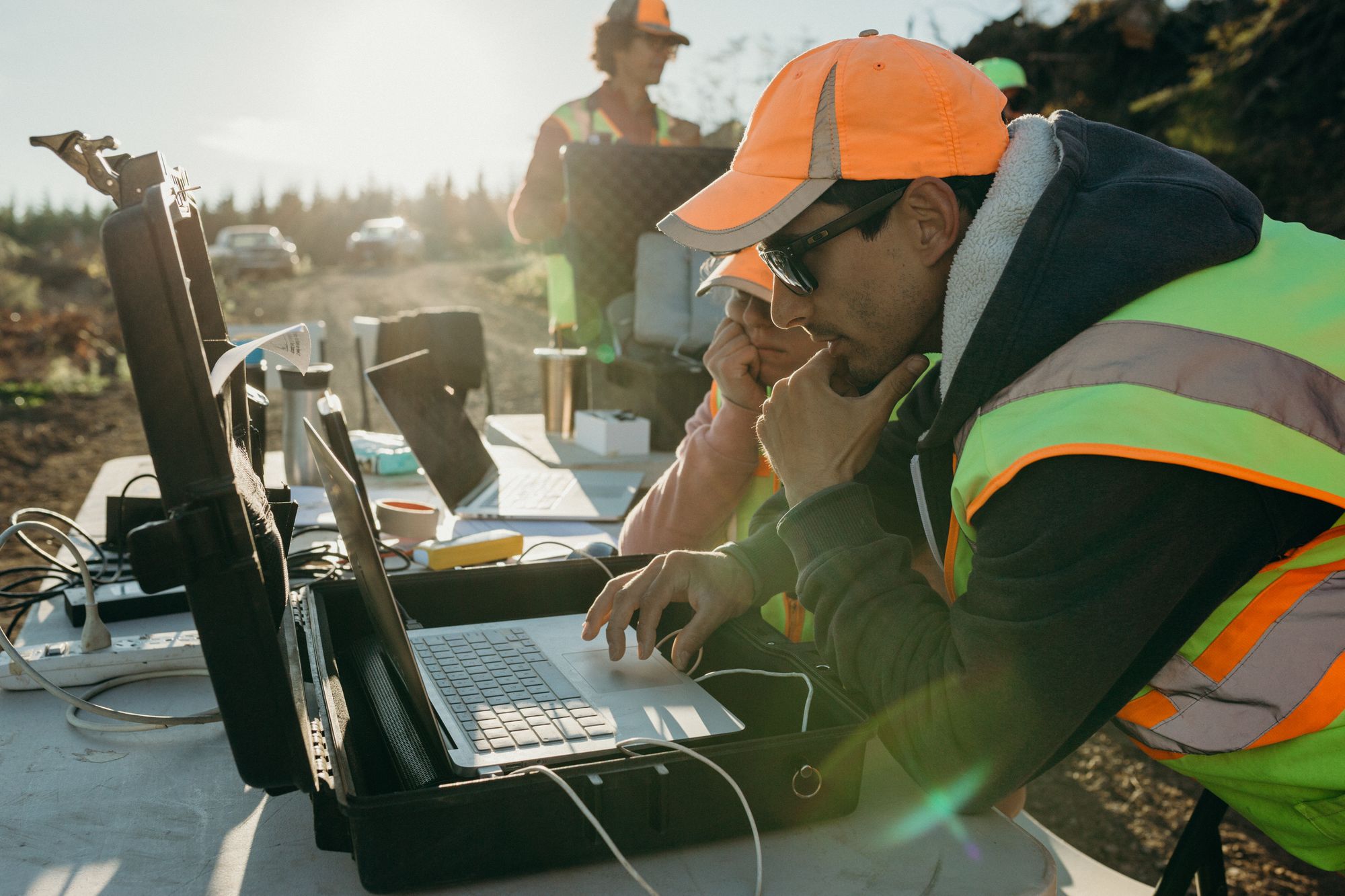
Generally, the first choice is PLA due to the low cost and flexibility it offers. Plus PLA has some acceptable mechanical properties. “We don’t usually have to worry about high temperatures,” shares John, “but we have had a couple of situations where our parts needed to deal with hot or high vibration environments.”
⚡️Download our our free engineering guide to 3D printing here
3D printing for speed
Because they make so many of their parts custom, DroneSeed uses Fused Deposition Modelling (FDM) to produce higher performance prototypes and the majority of finished parts.
For DroneSeed, FDM offers plenty of advantages such as:
- Lower costs
- Range of available materials
- Complex parts can be easily designed
- Faster production
If a higher performance material than PLA is needed, the team switches over to MJF.
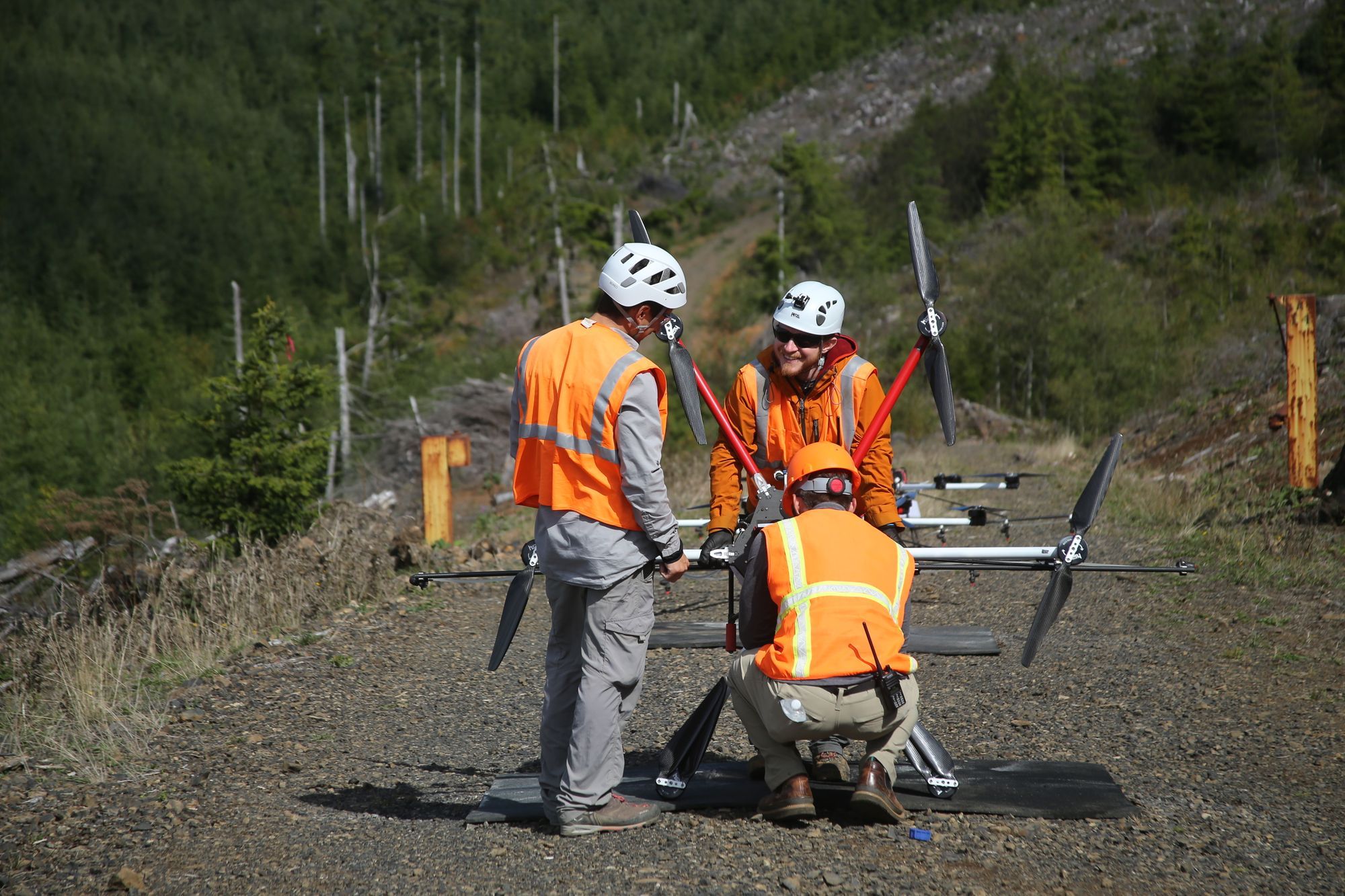
For the [3D printing](https://www.hubs.com/guides/3d-printing/) process, “We design our components so that everything has a specific wall thickness to get the balance between strength and weight,” describes John, “also when working with PLA, it’s important to stiffen the part by adding extra supports or struts while constantly optimizing for weight. That way, it’s ready to go once it’s off the print bed.”
To keep the drones robust, no additional finishing is needed. The basic finishes are smooth enough and mechanical strength trumps appearance.
Manufacturing for scale
DroneSeed uses a mix of in-house manufacturing tools as well as working with Protolabs Network to outfit its fleets.
“We have a handful of MakerBots and a laser cutter, but that’s only going to be able to cut it for limited, extremely tight turnaround prototyping,” says John, “with so many active fleets, the amount of required parts quickly multiplies beyond the in-house capacities.”
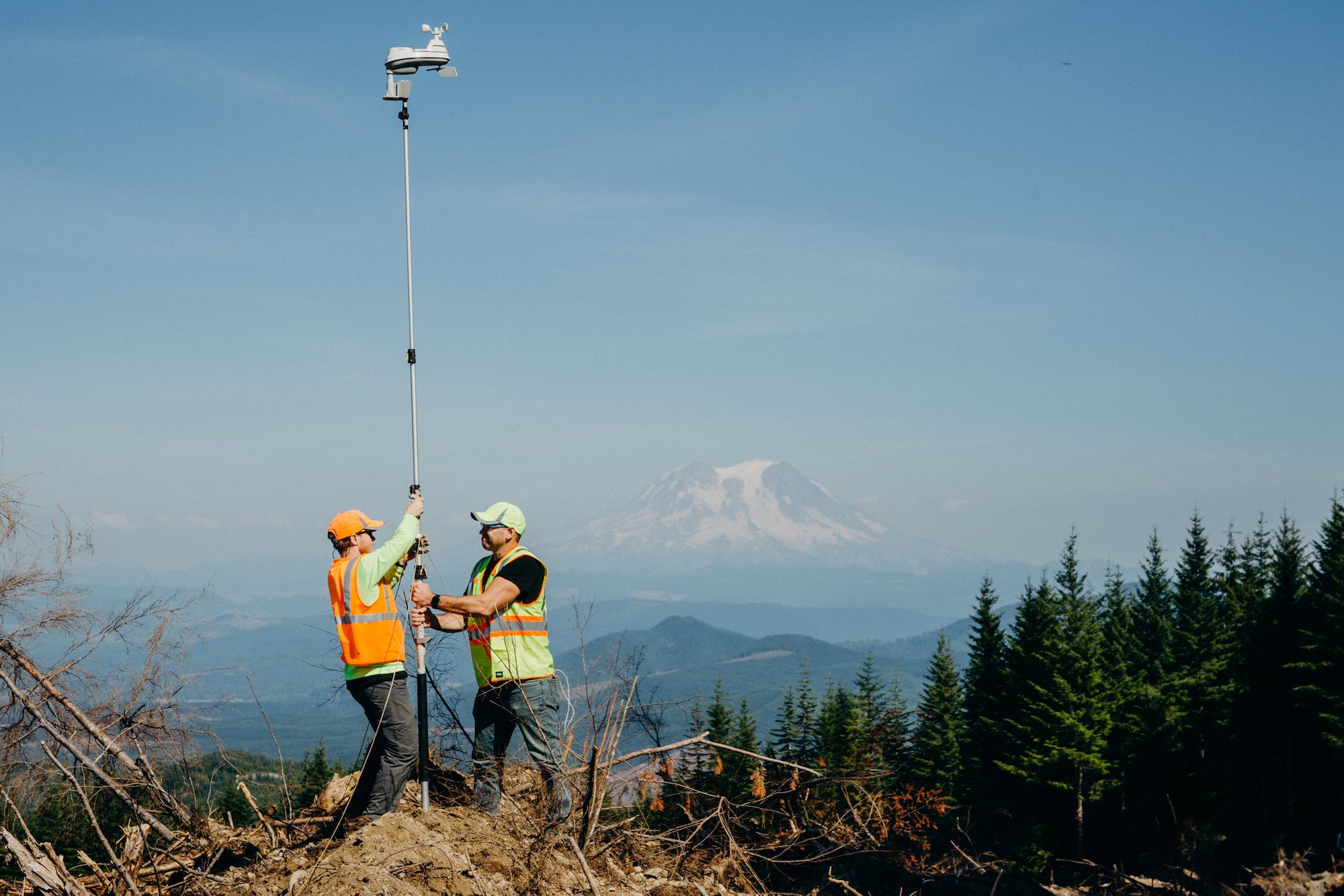
The average DroneSeed swarm has 5 drones. Each drone alone can have up to 70 individual 3D printed components, totalling to about 350 parts for a whole fleet. With that amount of parts, DroneSeed turns to us.
“As we verify our initial designs, the 3D printers are fine, but the moment we start going into outfitting a full fleet - forget it,” explains John.
“Being able to affordably leverage FDM processes on a tight schedule let us get out to the field with our tech in a way that probably wouldn't have been possible otherwise.”
- John Thomson, Senior Drone Systems Engineer at DroneSeed
Read more customer stories:
- Learn how Kepler launched a nanosatellite into space in 365 days
- Find out how Skelex manufactures industrial passive exoskeletons on-demand
- Building headphones that deliver the highest level of audio performance possible
⚡️Or upload a part to the Protolabs Network platform to get an instant quote