Formula SAE is an annual engineering student competition taking place all over the world. The race attracts teams from the world’s best technical Universities who have 9 months to design, manufacture, and compete with a small Formula-style race car.
When they had to manufacture parts with tighter tolerances than they ever needed before (as tight as ± 5 microns), the Southampton University Formula Student Team (SUFST, for short) turned to Online Manufacturing with Protolabs Network to source critical parts of their suspension system. This way they got access to advanced CNC machining capabilities that allowed them to drastically increase the reliability of their car and to achieve their best season yet.
THE BREAKDOWN | |
---|---|
Organization | SUFST |
Location | Southampton, UK |
Product | Formula Student Race Car |
Industry | Automotive |
Why Protolabs Network? | High precision CNC maching capabilities |
The Result | Best race season yet |
Technology | CNC machining |
Materials | Anodized Aluminum 6082 |
Watch Pau Miquel, SUFST’s Chief Designer, describing the function of the parts they manufactured and keep reading if you want to learn more detail about their journey.
The Team
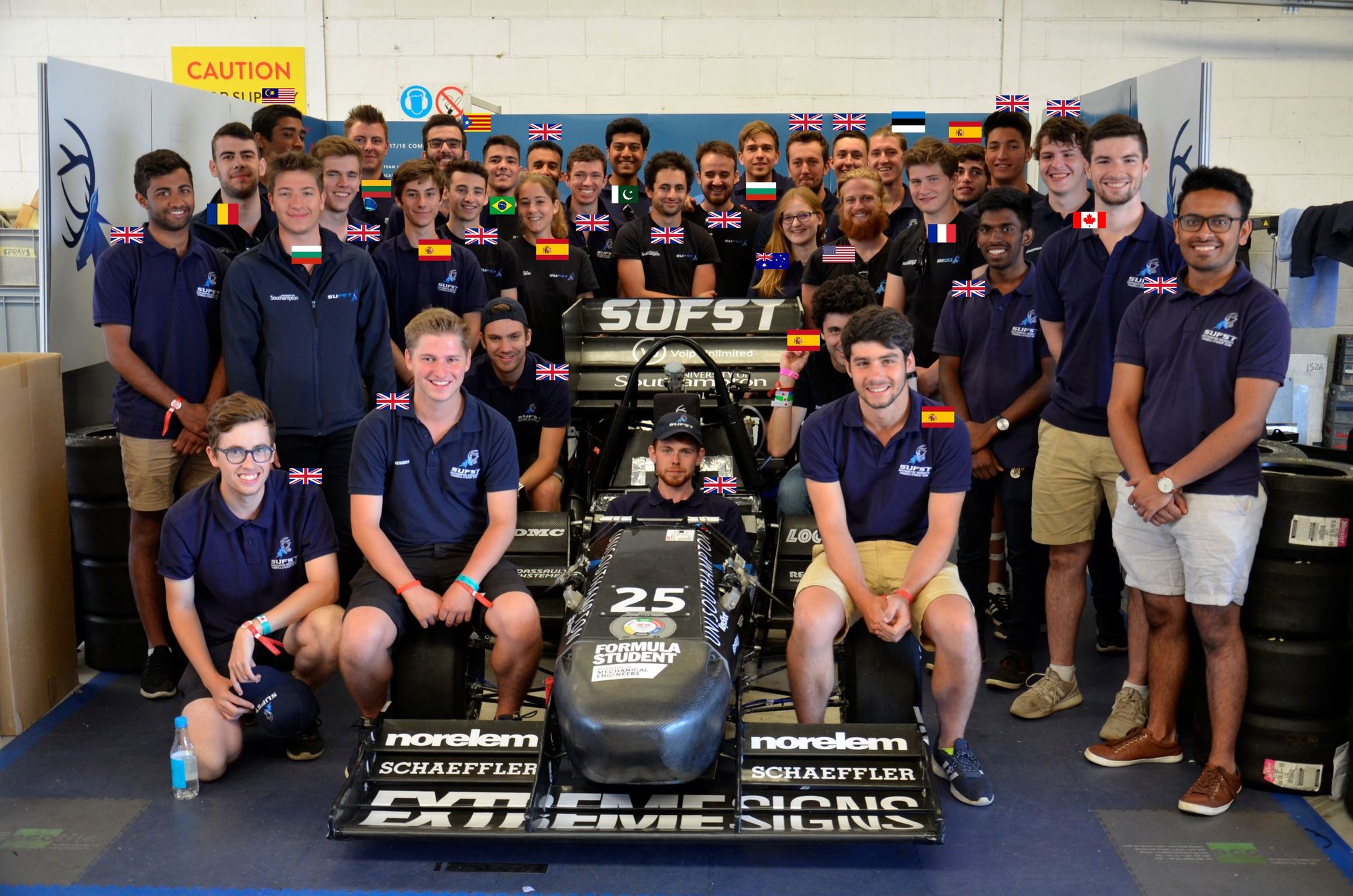
SUFST, founded in 2012, is a Formula Student team from Southampton, UK. Their first formula race car - the STAG O - was ready to compete in the Summer of 2013 and they have been racing every year since in national and international competitions.
Despite being young, the engineers of this team are highly ambitious and talented. Their senior members have years of Formula Student racing experience and a lot of hands-on knowledge gained by working for some of the biggest names in motorsport, like Red Bull Racing, McLaren and Force India.
Last year, the team managed to complete for the first time the Endurance Event of the Formula Student competition with their STAG V. The Endurance Event is a 22 km race that pushes the car to its limits and completing it is a huge achievement, as about 50% to 75% of all teams never make it.
The improved reliability of the suspension system, brought by the high-precision parts CNC machined by the manufacturing partners of our network, contributed greatly to this achievement. Let’s see how they did it.
The Design Brief
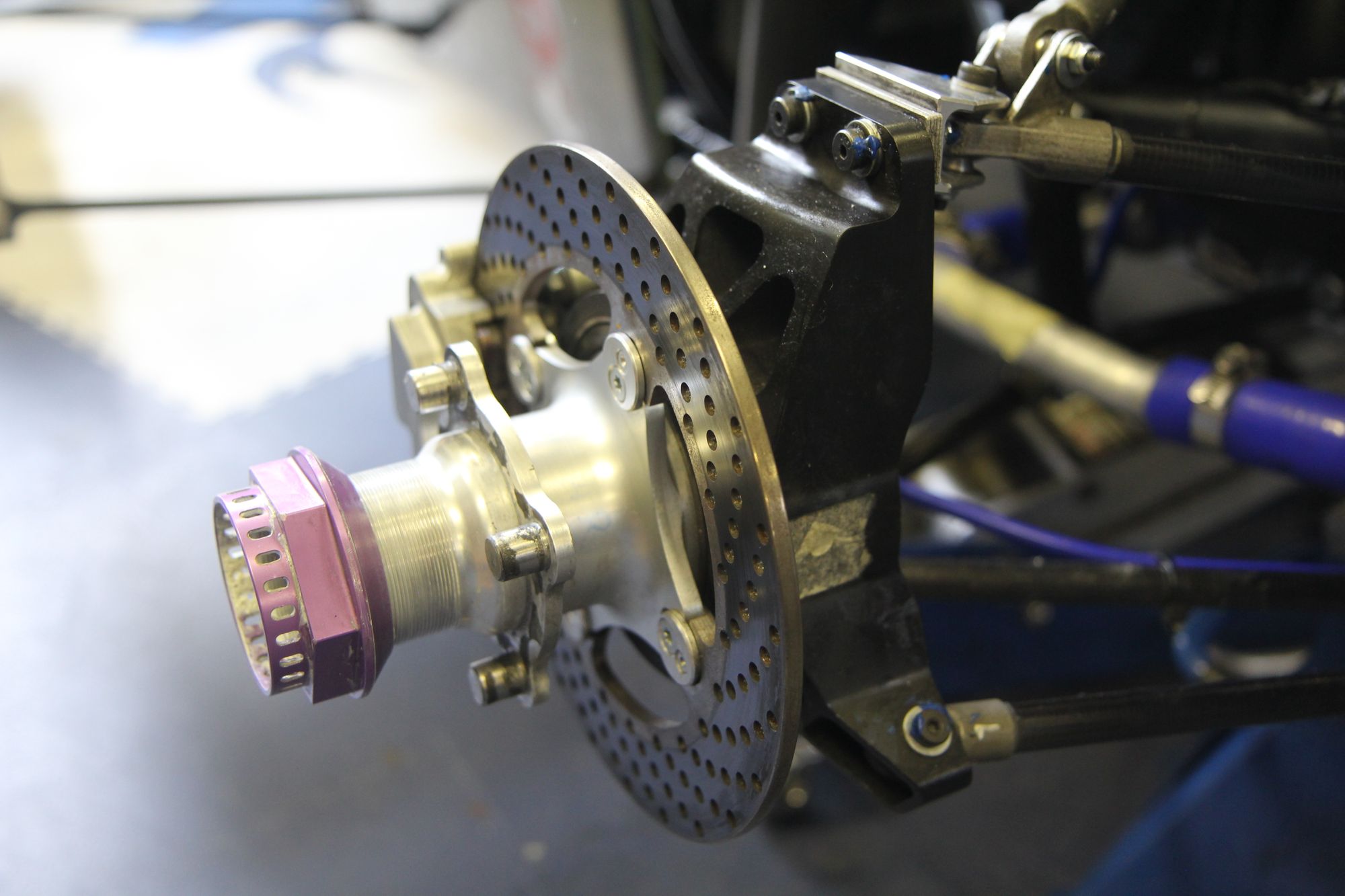
The Formula Student competition is a true engineering challenge! The young engineers have to solve real-life problems and optimize the performance and reliability of their car while making the necessary compromises. Here are some of their main design restrictions they have to take into account:
- Time: The teams have 9 months to design and build a race car from scratch and then compete during summer. This means that the teams have to work on a very tight timeframe.
- Safety: Before they are allowed to compete, all cars must pass a process called scrutineering where the judges examine every detail against a 130-page long rulebook to make sure the car is safe to drive.
- Manufacturing: The rules also state that most of the manufacturing work has to be done by the students. This is a huge project since the car assembly typically has 3000+ components.
Of course, some components have a complex geometry or technical requirements that surpass the skillset of the students, who are usually only allowed to use manual machines. For these parts, SUFST used to locally outsource the manufacturing before they decided to work with Protolabs Network.
The subsystem with the most challenging to machine components is the suspension system, which connects the wheels to the chassis of the car. The components that the SUFST team needed to outsource were the wheel hub, the upright and the wheel nut. We will examine each of them.
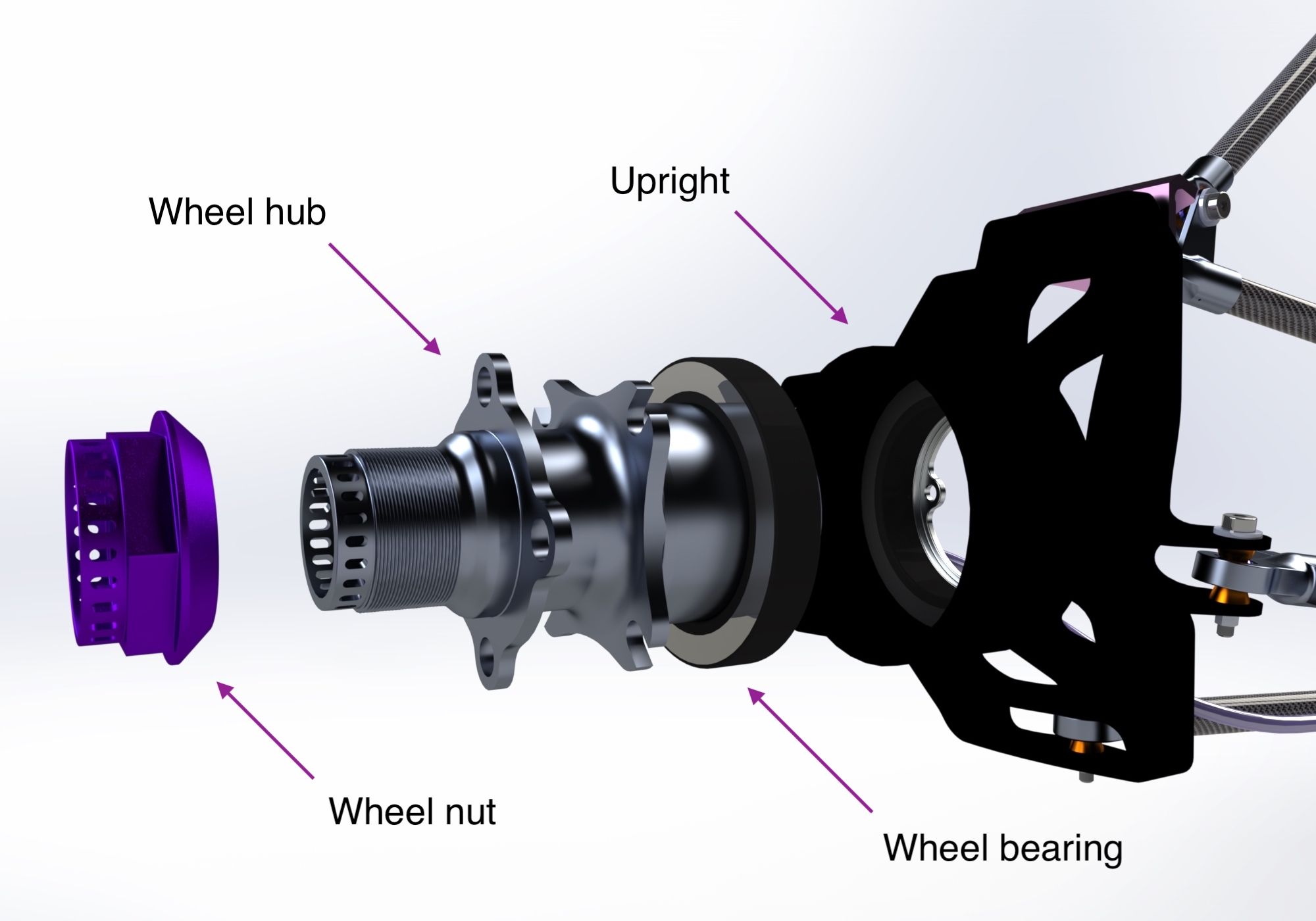
The “Tightly Toleranced” Wheel Hub & Upright
Pau Miquel, SUFST's Chief Designer, explains the function of these two key components:
The hub is the component that connects the wheel and the upright which is attached to the main body of the car. The hub rotates with the wheel, while the upright needs to stay stationary. To do this a bearing fits between the two. The fit of this bearing is crucial for performance and reliability.
The young engineers of SUFST learned the hard way that tight tolerancing is essential here. In the past, the fitting of the bearing caused many reliability issues during the race. The team traced these problems back to the loose tolerances and rough surface finish of their old hub and upright.
After consulting with the bearing manufacturer, they determined their technical requirements: a dimensional tolerance of ± 5 microns and a surface roughness of Ra 0.4 μm were needed. These very high precision requirements were beyond the capabilities of their local machine shop.
So, the team decided to take advantage of the Protolabs Network global network to fulfill their manufacturing needs. Using Online Manufacturing allowed them to get access to advanced high precision CNC machining quickly and easily.
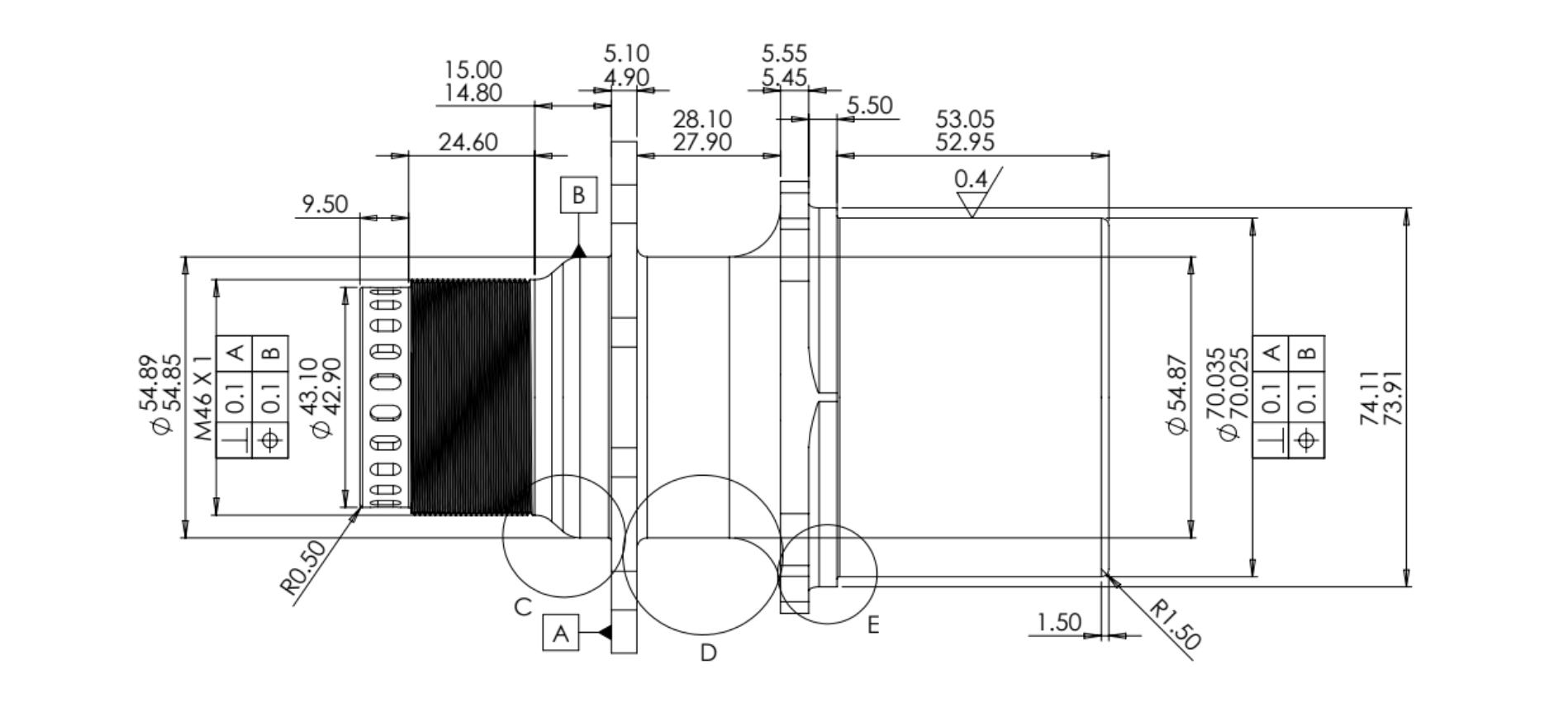
📍 Download our free engineering guide to CNC machining here
The “Pristine” Wheel Nut
The wheel nut is a humble component that serves a very important function in a formula race car. Pau Miquel explains:
The wheel nut keeps the wheel in place. For safety reasons, it has to meet very strict requirements. We decided to go for this custom single nut design because it allows us to change our tires quickly between events during the competition.
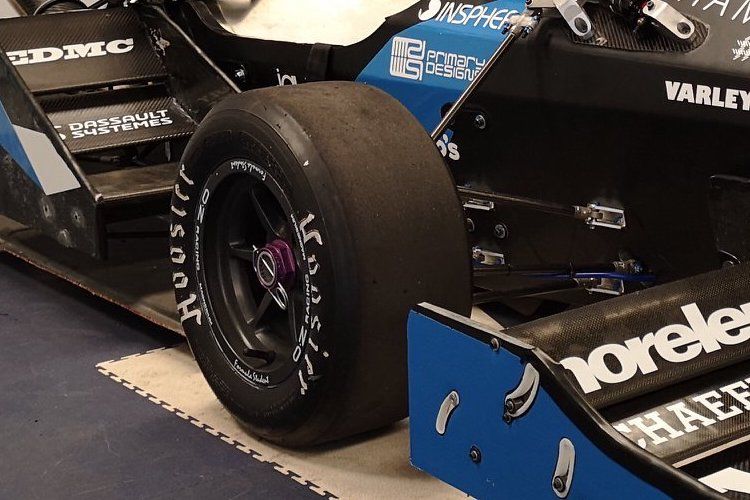
He then adds:
This came handy when we woke up and saw the track completely wet on the day of the competition. We were completely confident though that we could change from dry to wet tires very quickly and easily right before the race if that was necessary.
The rules state that the wheel nuts must be in pristine condition and Protolabs Network delivered: after machining the nut in a 5-axis CNC mill-turning system, the nuts were anodized purple to achieve an aesthetically pleasing and abrasion resistant finish.
The Protolabs Network Experience
Another reason the students enjoyed the Protolabs Network CNC machining services was the customer experience. Pau mentions:
One of the reasons we liked working with Protolabs Network was the Customer Service. This was something we have never experienced before. It was almost surprising and shocking - in the best way possible - when an issue during production was identified and resolved by the Protolabs Network team even before the parts arrived.
Preparing for the future
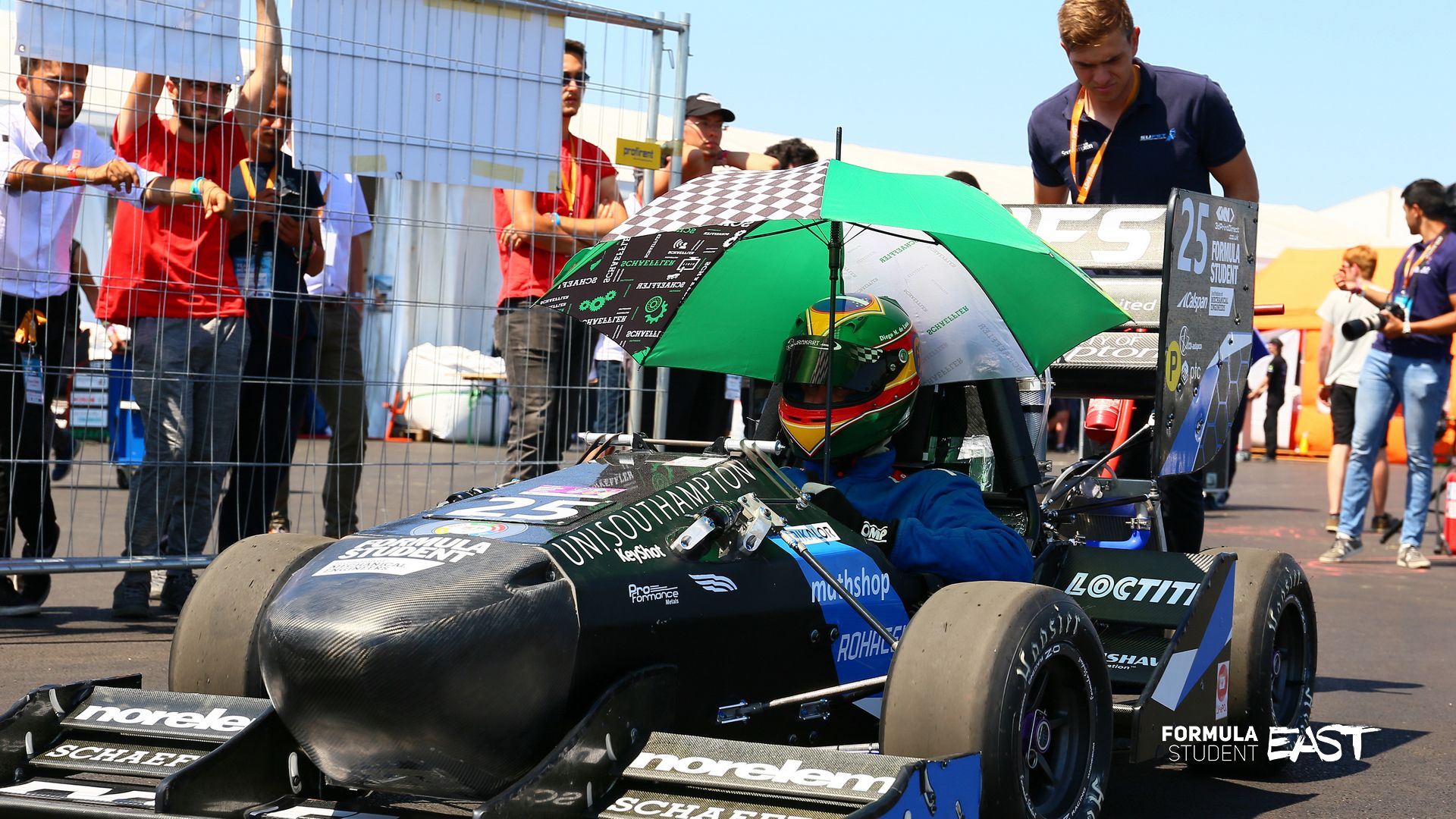
The engineers of SUFST are currently working on finalizing the design of their next year’s race car. Having solved their major reliability issues, the team now focuses on increasing the performance of their next car - the STAG VI - by reducing its weight. They are also performing a lot of testing on this year’s car to inform next year’s design.
Protolabs Network's role within this is to expedite the development process for these highly talented engineering students by giving them a platform where they can source without hassle the most challenging to manufacture components of their car. This way they can keep spending their time on what matters the most: honing their engineering skills by building the best formula race car possible.
Learn more about the Protolabs Network platform here.
Or start uploading your parts today to get an instant quote.