German Orbital Systems provides turnkey satellite solutions to its customers in the aerospace, telecommunications, and optical communication sectors. Their engineers work with clients to outline device functionalities, design the satellite -- or additional components -- and then work with service providers to manufacture the final product. Common applications include remote sensing, scientific communication, data collection, and communication.
“A lot of times, customers come up with the ideas and we discuss what’s possible,” says Connor Jonas, aerospace engineer at German Orbital Systems. The company’s projects include an ADS-B antenna, that can collect airplane data while the craft is in flight over water, as well as a unique sequencer unit to manage the launch of up to 40 satellites, which is a crucial component for large satellite clusters.
The Breakdown | |
---|---|
Organization | German Orbital Systems |
Location | Berlin, Germany |
Product | Nanosatellites |
Industry | Telecommunications |
Why Protolabs Network? | Quick on-time delivery of space-grade parts |
Technology | CNC machining |
Materials | AI 6061, PEEK, Teflon |
Design Tools
To ensure perfect products, German Orbital Systems (GOS) uses a variety of tools to design CubeSats, microsatellites and custom projects. All CAD work is completed with SolidWorks, and circuit boards are outlined with Altium.
To further verify the designs, engineers use Matlab and SolidWorks Simulation to test for warping, buckling, thermal analysis and communication capabilities. These digital tools let engineers easily run multiple scenarios in a virtual environment, improving design time.
On the hardware side, engineers prototype pretty consistently with an in-office Ultimaker. “We’ll use [the 3D printer] all the time for new mechanisms, structures -- we’ll print everything out to make sure everything fits and for manufacturability,” Jonas explains. Beyond new mechanisms, the company does a fair amount of circuit board assembly in house.
For CubeSats, the general design is fairly standardized and has defined form factors. This is good but can be limiting when customers want to do more with a design or a specific application requires more space than the form factor gives. For this reason, GOS offers microsatellite manufacturing services as well as CubeSats.
Working with the CubeSats speeds up the design process since engineers can rely on standardized structures and components, and can follow similar MIAT procedures for all our CubeSat orders.
On the other hand, microsatellites allow for more creativity, and are a more suitable choice for larger payloads and involved sensing applications. It’s also ideal for GOS clients that want to have more product customization.
According to Jonas, microsatellites often bring engineers more interesting applications but do require longer timelines to ensure all of the components work and properly fit. Though depending on the application, engineers can tweak the Attitude Orbit and Control System (AOCS) and Electric Power Supply (EPS).
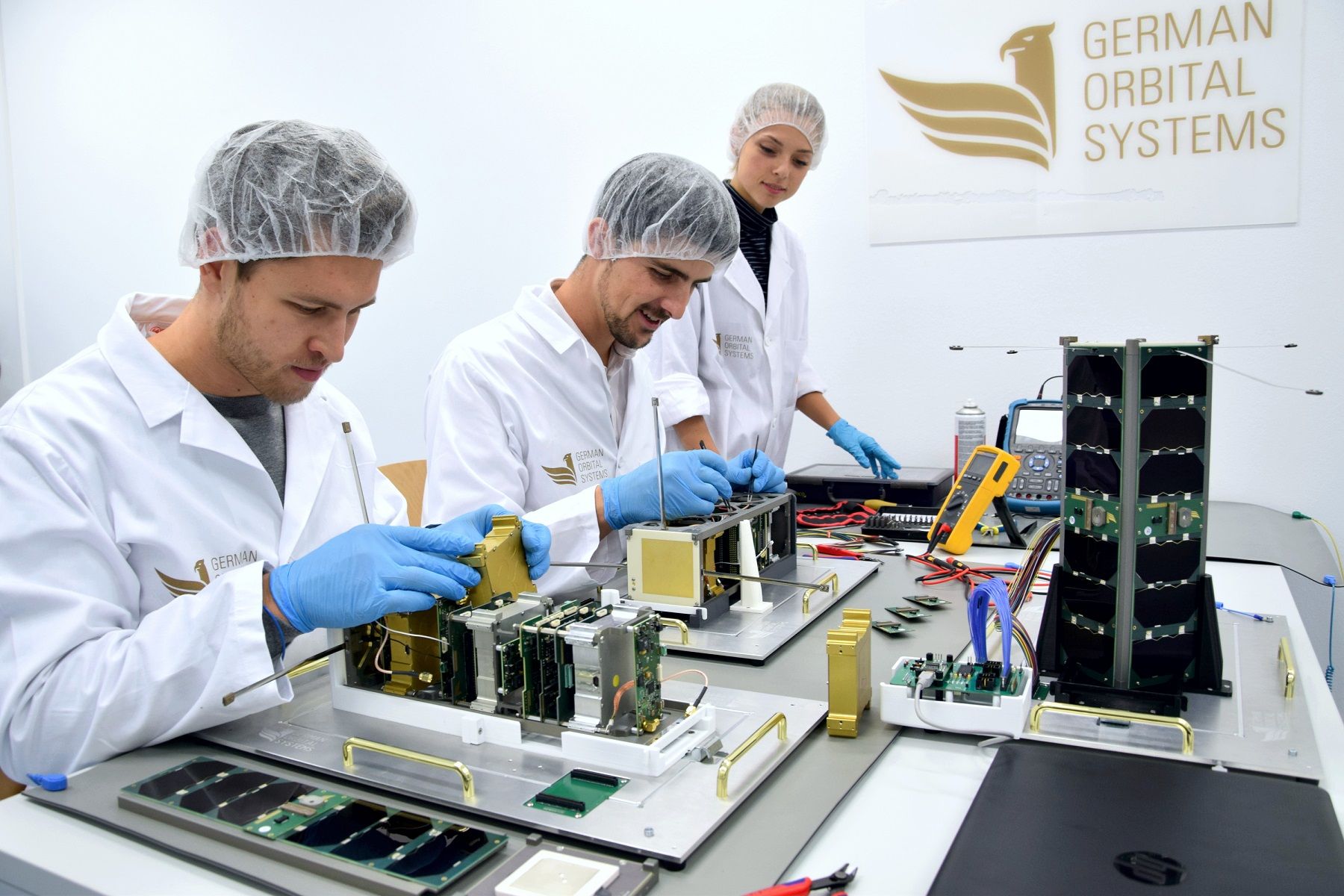
Outsourcing Manufacturing
GOS’ primary focus is on engineering design services, so the organization works with service providers to outsource all of their manufacturing needs.
Over the years, GOS has shifted to use Protolabs Network more frequently as a way to get more transparency with cost and ultimately reduce lead times. Being based in Berlin, GOS relied on local manufacturers and a multitude of providers, but sometimes found it difficult to accurately predict when products would arrive, which prolonged delivery to the client.
While working with more than one manufacturer, GOS would see lead times change from six weeks to eight weeks or be pushed out even further, which caused project bottlenecks.
“Protolabs Network is able to do [the manufacturing] in half the time, and that’s a huge advantage to us,” Jonas says.
Because GOS uses a small number of materials, this limits potential manufacturing methods. The organization uses CNC milling for satellite structures because they are cut from solid aluminum blocks. This technique provides repeatability, easier management through software-based workflows and reliable round-the-clock production.
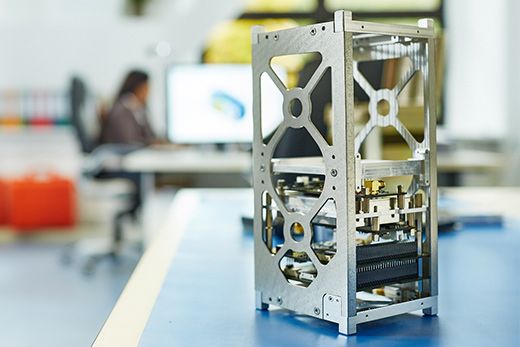
📍 Download our free engineering guide to CNC machining here
Materials
Material selection is an important part of German Orbital System’s design process -- not only for compliance but also product longevity. With satellites spending so long in space, materials need to have low mass, high strength, and low outgassing properties.
For both CubeSats and microsatellites, engineers want consistent material properties, minimal weight, and predictable costs. For the majority of designs, engineers rely on aerospace grade Aluminum 6061.
“Aluminum 6061 is chosen for its strength, its cost and its lightness. It also has low corrosion properties, which makes it common for aerospace applications,” says Jonas. Because of these factors, GOS uses aluminum alloys for the frames.
For non-metal secondary components, the major concern is outgassing. Certain materials shed gasses that might occlude optical instruments, reducing the solution’s effectiveness. To avoid large gas emissions, plastic components are made of PEEK or PTFE.
As available materials continue to evolve, Jonas says, there is the possibility of integrating carbon fiber into specialized designs. Carbon fiber is super lightweight, which is ideal for space technology but is currently very expensive to manufacture.
In Conclusion
As a comprehensive design firm, GOS strives to engineer the best possible products for its clients in the aerospace and telecommunication industries. By partnering with Protolabs Network, the company can bring their custom satellites to market (to space) faster than ever!
Learn more about the Protolabs Network platform here.
🚀Or start uploading your parts today to get an instant quote.