Goodall Design & Protolabs Network | |
---|---|
Organization | Goodall Design |
Location | Knokke, Belgium |
Industry | Boating |
Product | Sailboats |
Technology | CNC machining, 3D printing (in-house) |
Materials | Delrin, aluminum 6061-T6 |
Why us? | Wanted to receive parts faster |
Results | Higher quality control, more freedom to experiment with designs |
Goodall Design is one of the few brands that keep all their design work in-house. So far, this has proved successful for the company, whose boats have won major championships on almost every continent. This team of designers (and avid sailors) are constantly looking for improvements.
“Every time we go out sailing and we see something that could be improved, we immediately try out new parts and see if they make the boat better,” explains Laurent Verbeeck, CEO at Goodall Design, “It’s one thing for the boat to go fast in a straight line, it’s quite another if a boat allows for easy handling to give you that edge on the race course.”
3D printing and CNC for boat building
3D printing has accelerated the testing and learning process for Goodall Design. “For building boats, I don’t think the materials like carbon or epoxy are particularly new,” shares Laurent, “for us, the innovation that has greatly helped is 3D printing.”
The sailboat company has been leveraging 3D printing for around 3 years now to test out small parts. Their in-house FDM 3D printer produces small parts fast - not particularly high in strength, but perfect for testing. “Once we see that it works, we normally make a mold out of it,” Laurent adds. For larger parts, they usually order one or two CNC machined parts to experiment with.
Continuous design iterations
In particular, Goodall Design has been experimenting with their newest boat, the foiling VIPER convertible. With every new design and material iteration, there are 4 main factors that come into play: durability, cost, weight and appearance.
“Appearance is a huge reason for us,” remarks Laurent, “if someone is buying a new boat, they also want a nice-looking boat. For instance, a part that’s welded doesn’t compare to an aluminum CNC anodized part. Plus, if a part is smoother and more precise, it can also help make the boat faster.”
The rudder gudgeons (the part that attaches the rudder to the hull) are made from anodized aluminum. “The strongest material to go for would have been stainless steel,” explains Laurent, “but for larger parts, that can make the whole boat heavier. That’s why we chose aluminum here.” As the part has constant contact with the water, it was anodized to be more resistant to corrosion.
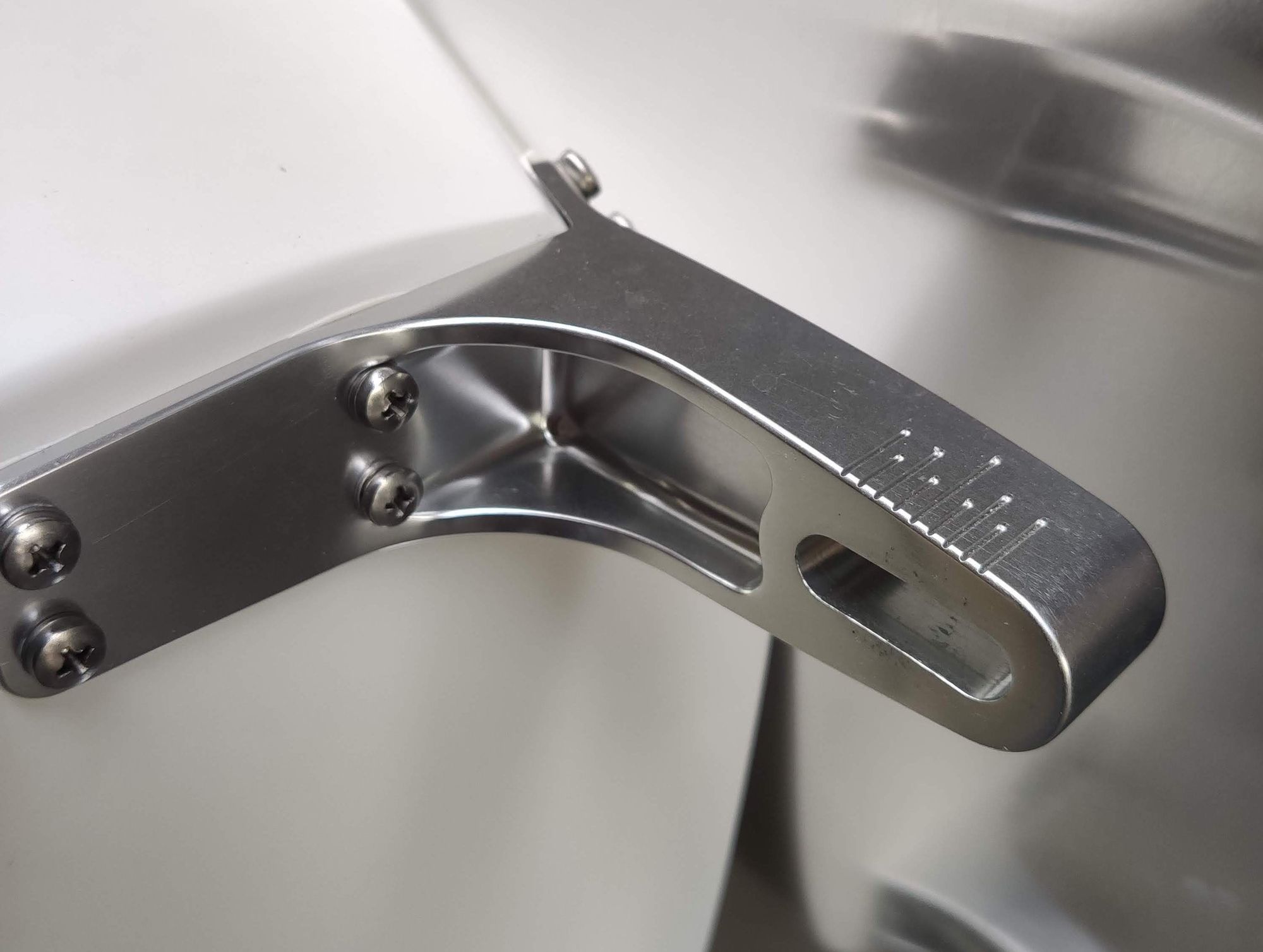
In the past, Goodall Design used to weld the rudder gudgeons, but switched to CNC machining to reduce the weight and improve the appearance. “What we found fantastic about CNC is the details you can also add to the part,” remarks Laurent, “like small markings that make it quicker and easier for the sailor to adjust the rudder to the right place. With these marks, sailors don’t need to measure every time or make their own marks. We try to add these small details to our boats to make it as easy as possible for the sailor,” he adds.
“The parts arrive completely finished with the markings,” says Laurent, “it’s very easy to customize and add a design and engravings to the parts - and we know that every part will have the same markings.”
For the spindle, and for other moveable parts that have regular contact with the water, Goodall Design opted for Delrin because of its resistance to corrosion and water absorption.
📕 Download our free engineering guide to CNC machining here
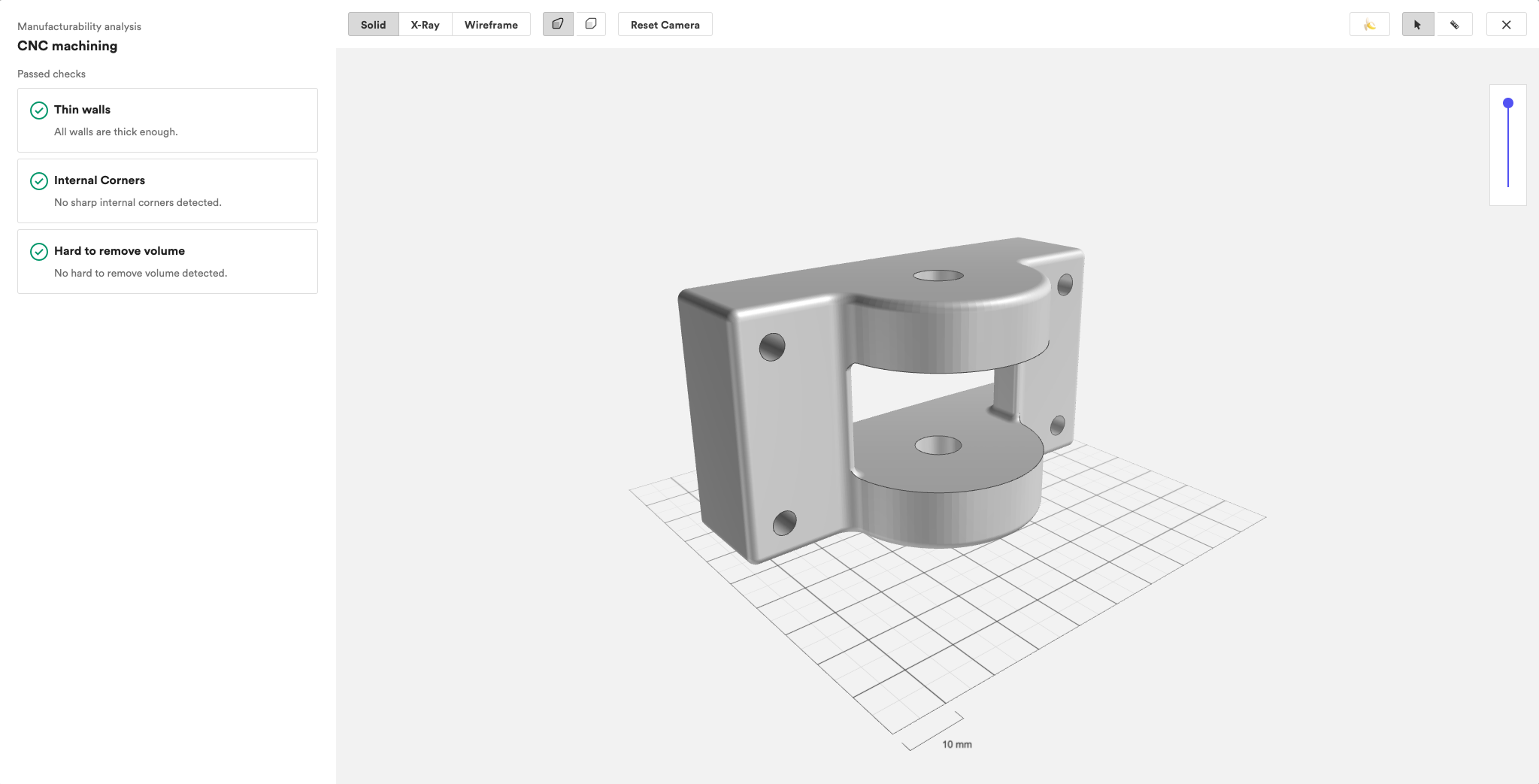
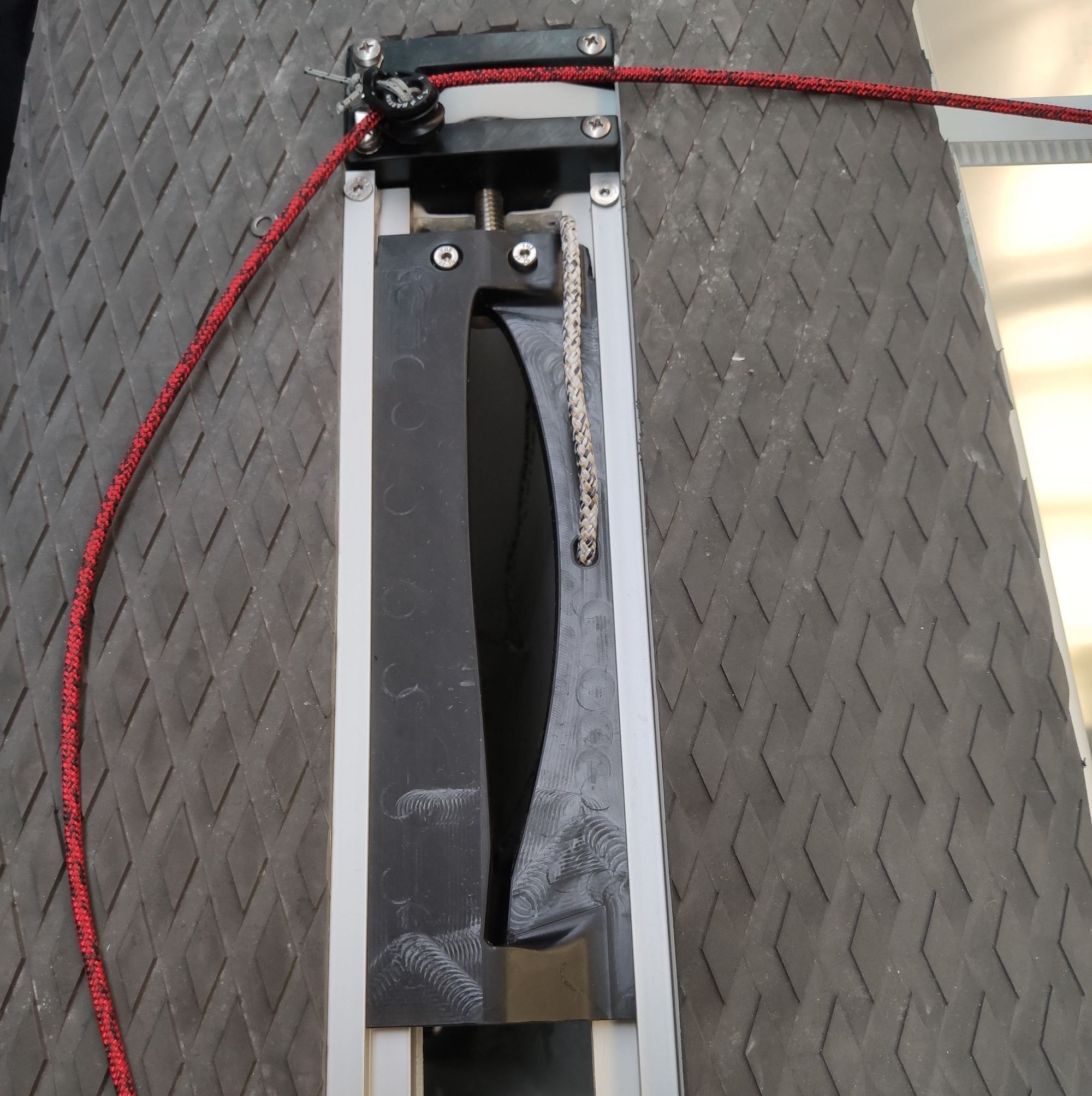
Delrin is hard and also affordable to machine. “We often have a combination of stainless steel, for things like screws and the riggers, and we use aluminum for the beams,” shares Laurent, “but for all the moveable parts, we prefer Delrin to make sure there’s no corrosion. Also, we can’t use materials that would absorb water as it would make the boat heavier.”
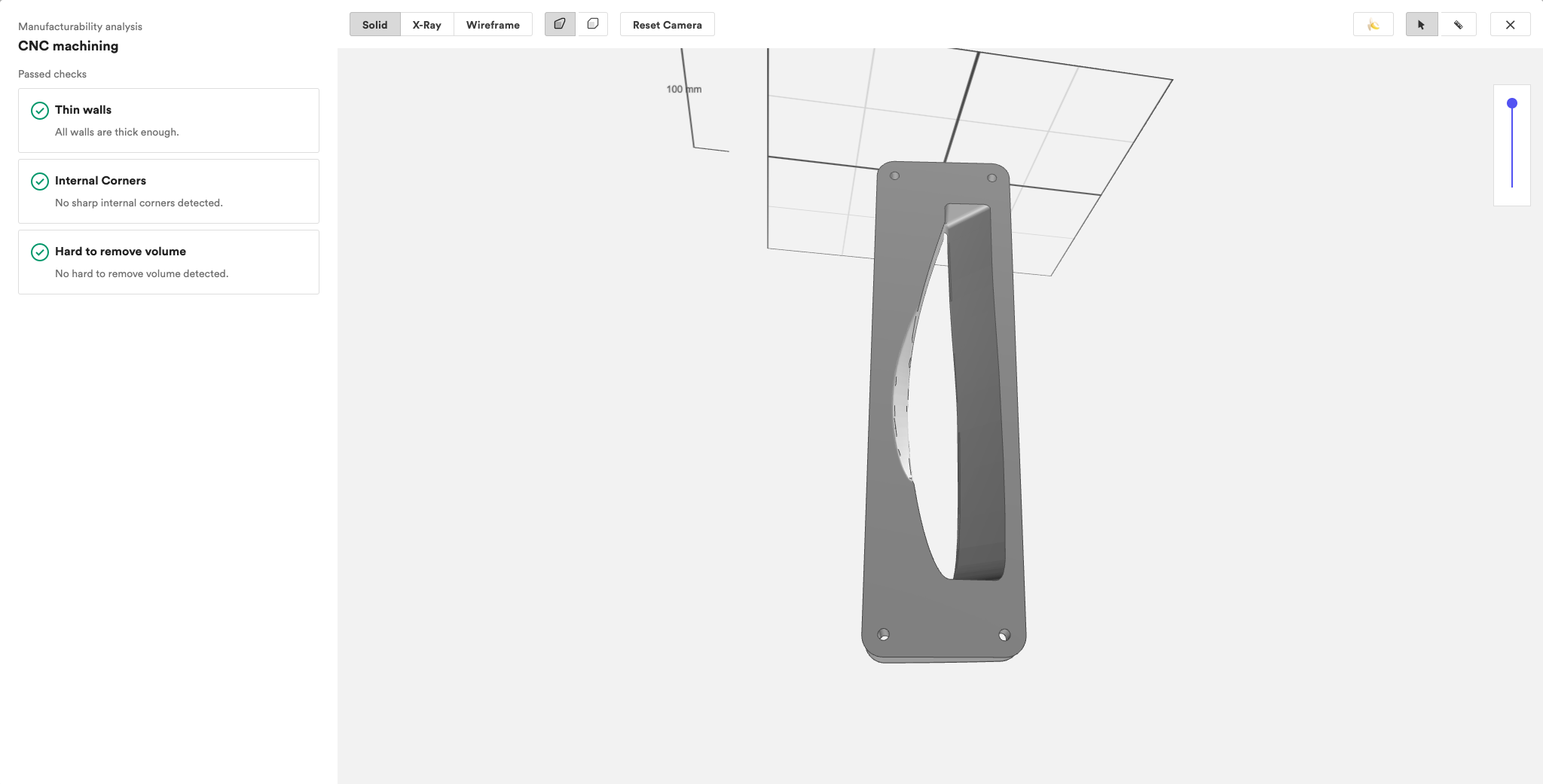
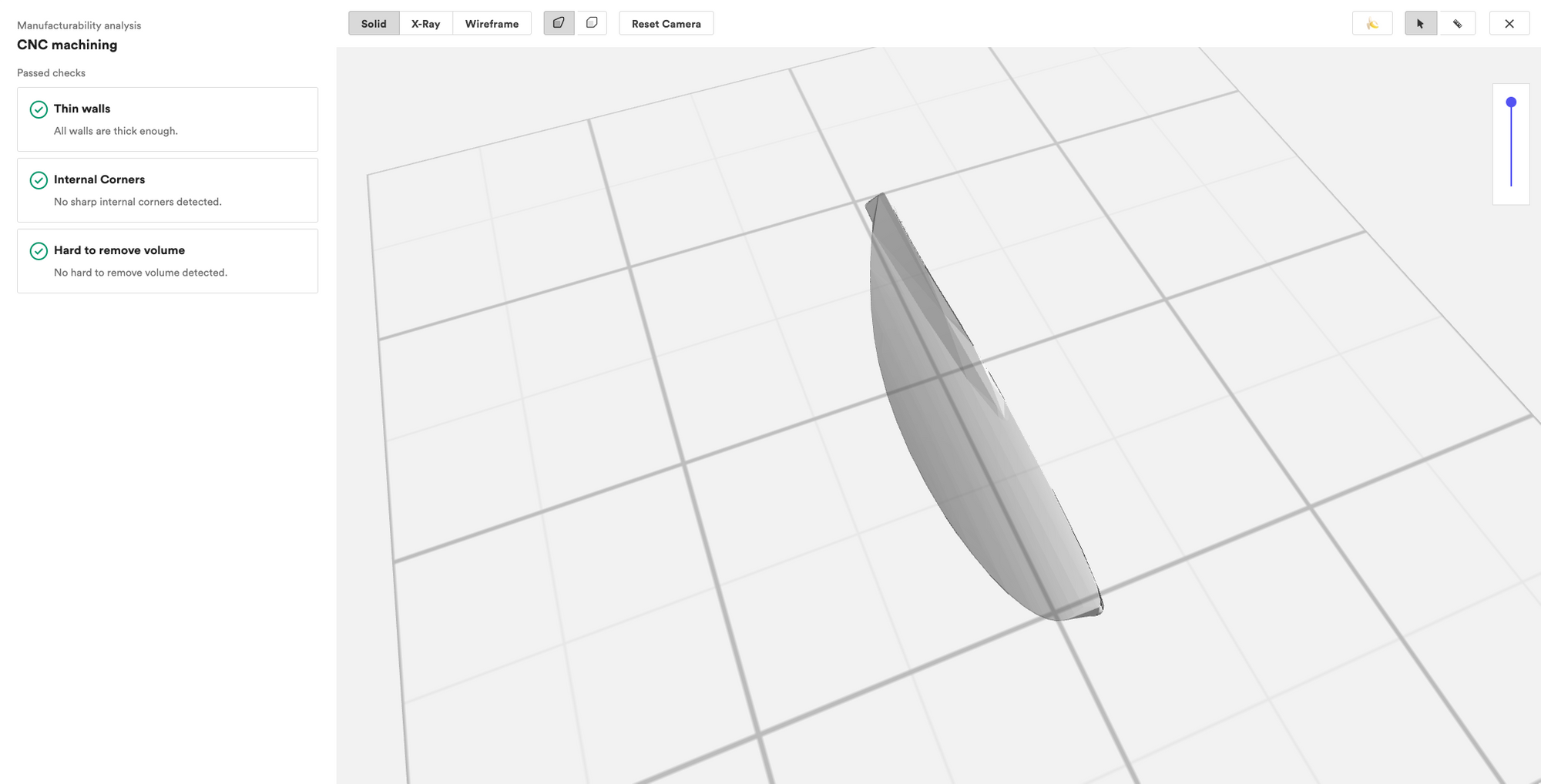
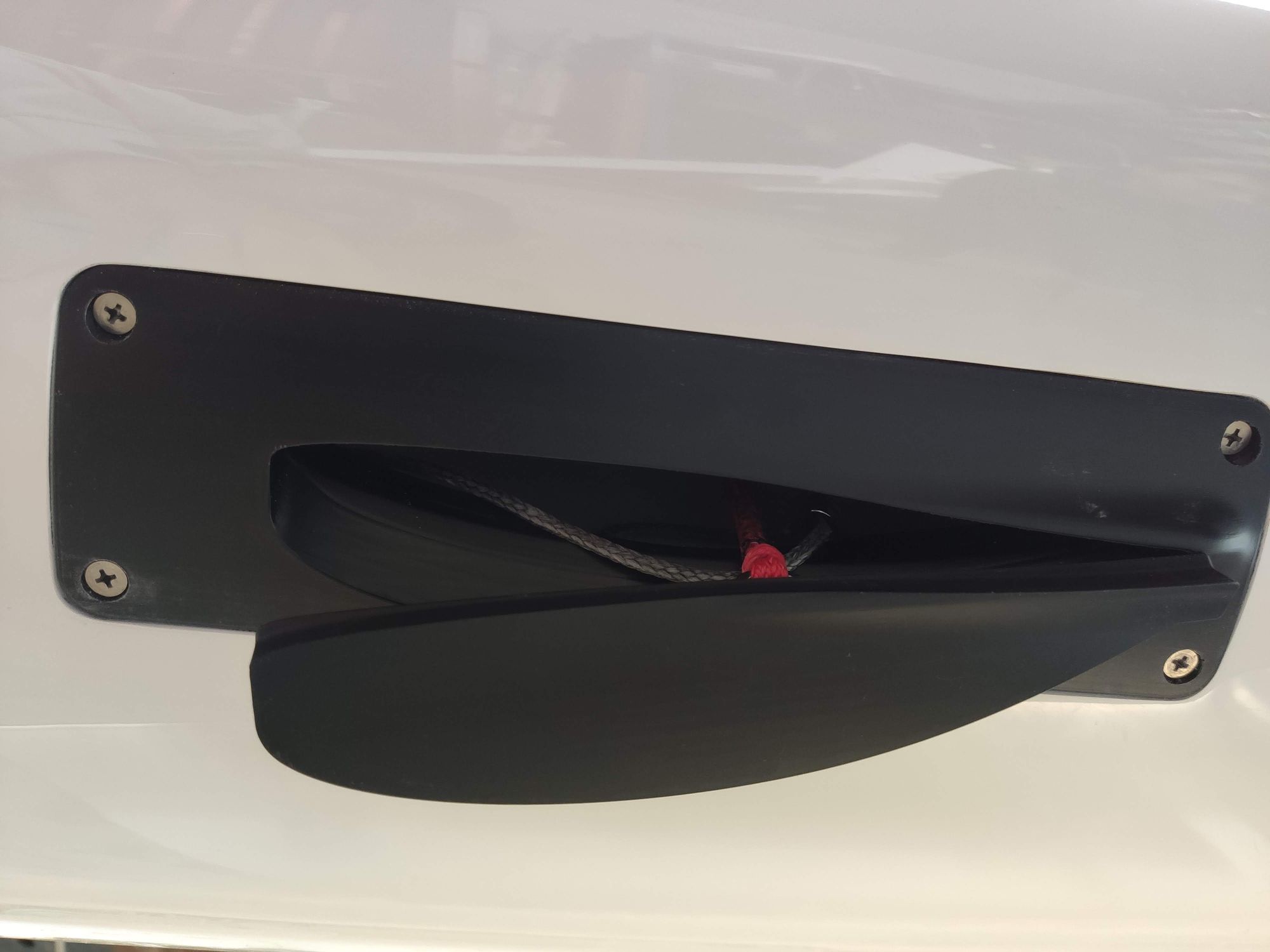
Inspired to design more
Laurent notes the team’s increased freedom to experiment in general, by using our network instant quoting tool: “In the past, we needed to email a company and ask to get quotes for different design and material variations. But at some point, you don’t feel comfortable asking for 20 different quotes from the same person. With the instant quoting, we don’t bother anyone. We just insert 20 different files and play around to see what’s possible and for what price.”
This energy to experiment more also stems from the shortened time between ordering a new part and testing it out. “If we try approaching a CNC company ourselves, we are just completely at the bottom of their priority list and it just takes a very long time. But with us, it’s very easy. You just order, even if it’s just one part, and manage everything in the same place. It makes the whole sourcing process very effective,” summarizes Laurent.
The Goodall Design team is also no longer held back by the quality of parts they receive. “What we really like is the internal quality control. If we are working with all different manufacturers, there are parts that start failing and you wonder if it’s because the design was bad or did they just didn’t pay enough attention to the part when they were making it,” Laurent describes, “We can just focus on the design of part itself, and not worry about the quality of the part.”
Read more customer stories:
- Manufacturing a fleet of drones to scale reforestation
- Learn how Kepler rapidly went from a sketch on a napkin to a satellite in space with our CNC machining
- Headphones that deliver the highest level of audio performance possible
Or upload a part to our platform to get an instant quote.